Система | Марка сплава | Химический состав % (по массе) | Свариваемость (сварка плавлением) | Рекомендуемые марки сварочной проволоки | Горячеломкость | |||
без присадки | С присадкой, гр. А. | С присадкой гр. Б | Крестовая проба К, % | Проба МВТУ А, мм/мин | ||||
Алюминиевые сплавы. | ||||||||
А. Термические неупрочняемые | ||||||||
Аl | АД1 | 99,3 Аl | св | св | св | св. А97; св. А85 | 5,0 | 9,0 |
Аl-Мn | АМц | 1,3 Мn | св | св | — | св. | 0,7 | 7,0 |
Аl-Mg | AMгl | 1,1 Mg | св | св | — | св. АМн | 12,0 | 6,0 |
АМг2 | 2,2 Mg; 0,4 Мn | нс | нс | св | св. АМгЗ | 12 | 6,0 | |
АМг3 | 3,6 Mg; 0,6 Si; 0,5 Мn | св | св | — | св. АМгЗ | 8,0 | 8,0 | |
АМг4 | 4,3 Mg; 0,6 Мn; 0,06 Ti | св | св | св | св. АМг4 | 10 | 7,0 | |
АМг5 | 5,3 Mg; 0,6 Мn; 0,06 Ti | св | св | св | св. | 10 | 7,0 | |
АМг6 | 6,3 Mg; 0,6 Мn; 0,06 Ti | св | св | св | св. АМг6 | 8,0 | 8,0 | |
Б. Термически упрочняемые | ||||||||
Аl-Сu | Д20 | 6,5 Сu; 0,6 Мn; 0,15 Ti | св | св | — | Д20 | 15 | 6,0 |
1201 | 6,3 Сu; 0,3 Мn; 0,06 Ti; 0,17 Zr; 0,1 V | св | св | — | св. 1201 | 5,0 | 10 | |
1205 | 6,3 Сu; 0,6 Мn; 0,06 Ti; 0,11 Zr; 0,15 Cd | нс | нс | св | св. 1201 | 12 | 6,0 | |
Al-Mg-Si | АД31 | 0,6 Mg; 0,5 Si | нс | нс | св | св. | 15 | 6,0 |
АД33 | 1,1 Mg; 0,25 Сu; 0,6 Si; 0,25 Сг | нс | нс | св | св. АК5 | 12 | 6,0 | |
АД35 | 1,1 Mg; 1,0 Si; 0,7 Мn; 0,25 Сг | нс | нс | св | св. АК5 | 12 | 6,0 | |
АВ | 0,7 Mg; 0,3 Си; 0,85 Si; 0,25 Мn | нс | нс | св | св. АК5 | 10 | 7,0 | |
Al-Zn-Mg | В92ц | 4,4 Mg; 3,2 Zn; 0,8 Мn; 0,13 Zr; 0,14 Cr | св | св | нс | св. В92ц | 12 | 6,0 |
1915 | 1,1 Mg; 3,7 Zn; 0,4 Mn 0,18 Zr | нс | нс | св | св. | 10 | 7,0 | |
Al-Mg-Cu | ВАД1 | 2,5 Mg; 4,1 Cu; 0,6 Mn; 0,06 Ti; 0,15 Zr | св | св | нс | ВАД1 | 10 | 7,0 |
Д1 | 0,6 Mg; 4,3 Cu; 0,6 Mn | нс | нс | нс | D1 | 40 | 2,0 | |
Д16 | 1,5 Mg; 4,3 Cu; 0,6 Mn | нс | нс | нс | D16 | 50 | 1,0 | |
Д19 | 2,0 Mg; 4,0 Cu; 0,75 Mn | нс | нс | нс | Д19 | 45 | 2,0 | |
Al-Mg-Cu-Zn | В95 | 2,3 Mg; 1,7 Cu; 6,0 Zn; 0,4 Mn; 0,18 Cr | нс | нс | нс | В95 | 50 | 1,0 |
В96 | 2,6 Mg; 2,3 Cu; 8,5 Zn | нс | нс | нс | В96 | 60 | 1,0 | |
Al-Mg-Si-Cu | АК6 | 0,6 Mg; 2,2 Cu; 0,9 Si;0,6 Mn | нс | нс | нс | АК6 | 45 | — |
АК8 | 0,6 Mg; 4,3 Cu; 0,9 Si; 0,7 Mn | нс | нс | нс | АК8 | 50 | — | |
Al-Mg-Cu-Fe-Si | АК4 | 1,6 Mg; 2,2 Cu; 1,2 e; 1,3 Ni | нс | нс | нс | АК4 | 60 | — |
АК4-1 | 1,6 Mg; 2,2 Cu; 1,2 e; 1,2 Ni | нс | нс | нс | АК4 | 65 | — | |
Магниевые сплавы | ||||||||
А. | ||||||||
M-Мn | MA1 | 1,9 Мn | св | св | нс | MA1 | 10 | — |
MA8 | 1,9 Мn; 0,25 Се | нс | нс | св | MA2-1 | 20 | — | |
Mg-Zn | MA20 (ВМД8) | 1,25 Zn; 0,2 Се; 0,09 Zr | нс | нс | св | MA20-1 | 10 | — |
Mg-Al-Zn | MA2 | 3,5 Al; 0,5 Zn; 0,3 Мn | нс | нс | св | MA2-1 | 15 | — |
MA2-1 | 4,4 Al; 1,1 Zn; 0,4 Мn | св | св | нс | MA2-1 | 20 | — | |
Mg-Zn-Cd-La | MA15 (ВМД3) | 1,6 Cd; 3,0 Zn; 0,9 La; 0,7 Zr | нс | нс | нс | MA15 | 30 | — |
Mg-Zn-Cd-Nd | MA19 (ВМД6) | 0,6 Cd; 6,2 Zn; 1,7 Nd; 0,7 Zr | нс | нс | нс | MA19 | >30 | — |
Б. | ||||||||
Mg-Zn | MA14 (BM65-1) | 5,5 Zn; 0,6 Zr | нс | нс | нс | MA14 | >40 | — |
Mg-Nd | MA12 | 3,0 Nd; 0,6 Zr | св | св | нс | MA12 | 15 | — |
Mg-Al-Zn | MA5 | 8,5 Al; 0,5 Zn; 0,3 Mn | св | св | нс | MA5 | 20 | — |
Mg-Mn-Nd | МА11 | 3,0 Nd; 2,0 Mn: 0,2 Ni | нс | нс | нс | МА11 | >40 | — |
Свариваемость алюминия и его сплавов
Свариваемость алюминия и его сплавов [c.
Свариваемость алюминия и его сплавов в первую очередь определяется возможностью получения металла шва без трещин и пор при высоких механических свойствах п коррозионной стойкости сварных соединений. Кроме того, свариваемость алюминия и его сплавов характеризуется некоторыми затруднениями получения хорошего сплавления и плотного металла шва без шлаковых включений в связи с образованием в процессе сварки на поверхности металла шва пленки окиси алюминия и наличием ее на поверхности свариваемого металла. Пленка имеет значительно более высокую температуру плавления (2050°), чем алюминий (658°), и больший удельный вес (3,9), чем алюминий (2,7). При сварке алюминия и его сплавов необходимо учитывать высокую теплопроводность их (у алюминия в три раза больше, чем у железа), что вызывает быстрый отвод тепла от места сварки, Высокая теплопро- [c.572]
СВАРИВАЕМОСТЬ АЛЮМИНИЯ И ЕГО СПЛАВОВ [c.375]
Свариваемость алюминия и его сплавов. Проблемы металлургического характера-.
[c.378]
Особенности свариваемости алюминия и его сплавов. [c.127]
Свариваемость сталей — ОсноБНые характеристики 23 Сварка алюминия и его сплавов 27 [c.555]
При аргонно-дуговой и газовой сварке алюминия и его сплавов сварочная проволока и присадочные прутки следует применять того же или аналогичного состава, что и свариваемый металл. [c.29]
Для автоматической сварки сжатой дугой применяют установку УПС-501, рассчитанную на силу тока до 500 А. Для ручной сварки используют установку УПС-301, позволяющую сваривать на постоянном токе прямой и обратной полярности силой 4…315 А в непрерывном и импульсном режимах коррозионно-стойкие стали толщиной до 5 мм, медь и ее сплавы от 0,5 до 3 мм, алюминий и его сплавы толщиной 1…8 мм. Напряжение холостого хода этой установки 80 В, рабочее напряжение дуги 18…40 В. Плазмотрон установки УПС-301 имеет комплект сменных сопел с различными диаметрами канала и обеспечивает сварку на токах силой 25. ..315 А при прямой и 25…70 А при обратной полярности. Его конструкция обеспечивает возможность возбуждения дуги касанием свариваемого изделия.
[c.231]
Зависимость зазоров, расстояний между прихватками и их размеров от толщины свариваемых встык деталей из алюминия и его сплавов [c.340]
Электрошлаковую сварку алюминия и его сплавов осуществляют для толщин металла 50. .. 250 мм. Сварку ведут на переменном токе пластинчатыми электродами или плавящимися мундштуками. Применяют флюсы АН-301, АН-302 на основе галогенидов щелочных и щелочноземельных металлов. Формирование шва осуществляют медными водоохлаждаемыми или графитовыми кристаллизаторами. Плотность тока в электроде около 2,5 А/мм , скорость сварки 6. .. 8 м/ч. Прочность сварных соединений составляет 80. .. 100 % прочности основного металла. Технико-экономическая эффективность данного способа сварки возрастает с увеличением толщины свариваемых изделий. [c.448]
Сварка стали с алюминием и его сплавами. Процесс затруднен физико-химическими свойствами алюминия. Выполняется в основном аргонодуговая сварка вольфрамовым электродом. Подготовка стальной детали под сварку предусматривает для стыкового соединения двусторонний скос кромок с углом 70°, так как при таком угле скоса прочность соединения достигает максимального значения (см. рис. 13.7, б). Свариваемые кромки тщательно очищают механическим или пескоструйным способом или химическим травлением, затем на них наносят активирующее покрытие. Недопустимо применение дробеструйной очистки, так как при этом на поверхности металла остаются оксидные включения. Наиболее дешевое покрытие — цинковое, наносимое после механической обработки.
[c.499]
Алюминий и его сплавы сваривают автоматической сваркой по флюсу (рис. 93,6). Флюс с помощью дозирующего приспособления 1 непрерывно в процессе сварки насыпается впереди дуги 2 тонким слоем, при этом флюс не закрывает дугу, а слой жидкого флюса 4 надежно защищает сварочную ванну 3 и удаляет пленку окислов.
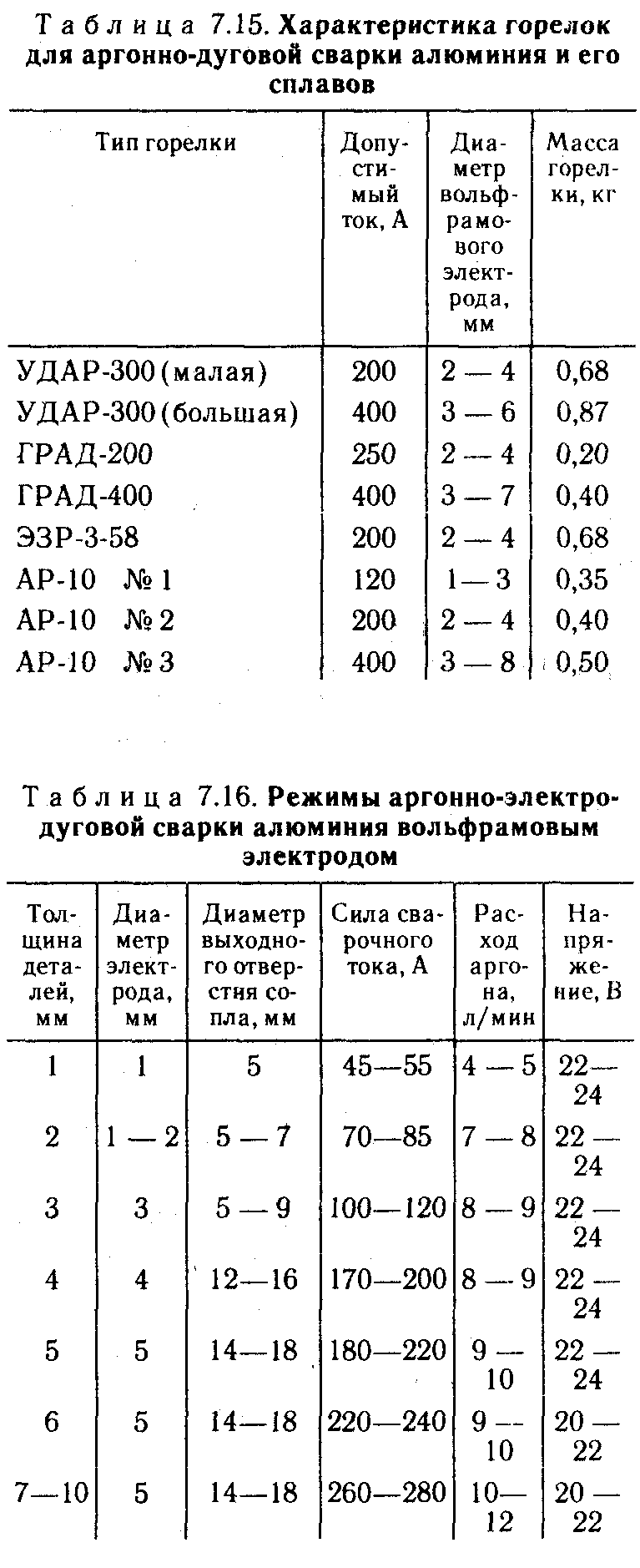
При сварке алюминия и его сплавов в качестве присадки применяют проволоку того же химического состава, что и химический состав свариваемого металла. Хорошие результаты при сварке сплава АМц и некоторых термически обрабатываемых алюминиевых сплавов дает применение присадочной проволоки марки АК, содержащей около 5% 51. Эта проволока обеспечивает повышенную жидкотекучесть металла шва и меньшую усадку его при остывании. [c.495]
При сварке алюминия и его сплавов угольным электродом берут присадочную электродную проволоку марок АО, А1 или прутки из сплава АК, содержащего 5 % кремния. Для растворения оксидной пленки служат специальные флюсы, в состав которых входят хлористые натрий, калий, литий, фтористые натрий и калий, сернокислый калий и криолит. Флюсы разводят на чистой питьевой воде и в виде кашицы наносят (окунанием или кисточкой) на присадочные стержни слоем 0,2—0,3 мм. После этого стержни сушат на воздухе при 20—25 °С в течение 25—30 мин. Флюс можно наносить также на свариваемые кромки.
[c.64]
Выбор мощности пламени при газовой сварке алюминия и его сплавов в зависимости от толщины свариваемого металла [c.517]
Газы — заменители ацетилена При сварке и резке металлов можно применять также другие горючие газы и пары горючих жидкостей. Для эффективного нагрева и расплавления металла при сварке необходимо, чтобы температура пламени примерно в два раза превышала температуру плавления свариваемого металла. Поэтому использовать газы — заменители ацетилена целесообразно только при сварке металлов с более низкой температурой плавления, чем сталь (алюминия и его сплавов, латуни, свинца) при пайке- и т. п. [c.35]
Сварка в инертных газах. Алюминий и его сплавы в инертных газах сваривают неплавящимся вольфрамовым электродом или плавящимся электродом. Сварку вольфрамовым электродом выполняют со сварочной проволокой или без нее. Состав электродной или сварочной проволоки принимается близким к составу свариваемого металла.
[c.407]
Технологические особенности сварки алюминия и его сплавов полуоткрытой дугой (по флюсу). Получение качественных сварных соединений из алюминия и его сплавов требует тщательного удаления перед сваркой жировой смазки со свариваемых кромок и электродной проволоки, а также обезжиривания поверхности металла на ширине 100—150 мм от кромки ацетоном или другими растворителями. Оксидную пленку, находящуюся под жировой смазкой на ширине 25—30. мм, удаляют механической зачисткой НЛП химическим травлением с последующей промывкой в проточной воде, осветлением, повторной промывкой и сушкой сжатым воздухом. Зачищенная поверхность алюминия сохраняет свои свойства в течение 3—4 дней. При более длительном хранении на зачищенной поверхности может образоваться оксидная пленка, адсорбирующая влагу из воздуха. [c.423]
Способность материалов свариваться ультразвуком различна. Хорошо свариваются медь, алюминий и его сплавы, титан и многие другие пластичные металлы хуже — жаропрочные стали к числу материалов, сваривающихся плохо, относятся инструментальные стали. Наибольшая толщина верхней свариваемой детали зависит в основном от подводимой к ней акустической мощности. Например, при мощности 2 кет удается сваривать плакированный дур-алюмин толщиной до 1—1,5 мм, а при мощности 4 кет до 2—2,5 мм.
[c.606]
Газовая сварка. Этот способ сварки алюминия и его сплавов малоэффективен. Основной его недостаток — необходимость применения флюсов и малая концентрация тепла по сравнению с дуговой сваркой. Мощность пламени выбирают в зависимости от толщины свариваемого металла [c.406]
Пламя должно быть строго нормальным. В качестве присадочного металла применяют сварочную проволоку из алюминия и его сплавов. Диаметр присадочной проволоки зависит от толщины свариваемого металла [c.408]
При сварке алюминия и его сплавов избыток кислорода не допускается, так как образуется при этом большое количество трудноудаляемой пленки окиси алюминия. При избытке образуется большое количество пор з сварном шве. Расход ацетилена зависит от толщины свариваемого металла (табл. 13).
[c.92]
Какова роль окисной пленки А12О3 при рассмотрении проблем свариваемости алюминия и его сплавов Каким образом эта пленка удаляется из зоны сварки [c.413]
Свариваемость алюминия и его сплавов. Алюминий и его сплавы имеют большую теплопроводность, теплоемкость и скрытую теплоту плавления. Теплопроводность алюминия в три раза выше теплопроводности низкоуглеродис-той стали при нагреве от 20 до 600°С разница в теплопроводности еще более возрастает. Следовательно, сварка алюминия и его сплавов должна выполняться с относительно мощным и концентрированным источником нагрева. [c.164]
Наиболее широко применяют сварку алюминия и его сплавов в атмосфере защитных газов неплавящимся (толщины 0,5—10 мм) и плавящимся (толщины более 10 мм) электродом. В этом случае получают более высокое качество сварных швов по сравнению с другими видами дуговой сварки. Применяют также автоматическую сварку плавящимся электродом полуоткрытой дугой по слою флюса, при которой для формирования корня шва используют медные или стальные подкладки. Возможна газовая (ацетилено-кислородная) сварка алюминия и его сплавов. Флюс наносят на свариваемые кромки в виде пасты или вводят в сварочную ванну на разогретом конце присадочного прутка. Алюминий и его сплавы также сваривают плазменной и электрошлаковой сваркой они достаточно хорошо свариваются контактной сваркой. Учитывая высокую теплопроводность и электропроводимость алюминия, для его сварки необходимо применять большие силы тока.
[c.237]
Таким образом, наиболее склонен к порообразованию алюминий и его сплавы. В сварочной технологии на возникновение пор влияет время пребывания сварочной ванны в жидком состоянии, что зависит от скорости сварки. При малой скорости сварки алюминия водород успевает покинуть ванну и наплавленный металл будет плотным, при больших скоростях сварки (Исв>50м/ч) водород не успевает выделиться из кристаллизующегося металла и образовать поры, а при скорости сварки 20 м/ч обычно возникают поры. При сварке алюминия и его сплавов типа АМгб требуются особые меры для очистки кромок свариваемых изделий и тщательная подготовка электродной проволоки, а также использование аргона, имеющего минимальную влажность (Г. Д. Никифоров).
[c.346]
Сварка алюминия и его сплавов. При сварке деталей из алюминия и его сплавов возникают трудности, связанные с тугоплавкостью пленки окислов (AI2O3) на поверхности деталей, температура плавления которой 2050 °С. Пленка мешает соединению свариваемых деталей, поскольку температура плавления алюминия 658 °С. Коэффициент линейного расширения алюминия в 2 раза, а теплопроводность в 3 раза больше, чем эти же параметры для стали, что приводит к значительным деформациям свариваемых деталей. [c.120]
Больщое значение при сварке алюминия и его сплавов имеет правильный выбор присадочного металла. Чтобы получить для металла шва свойства, близкие к свойствам основного металла (прочность, пластичность, коррозионная стойкость, теплофизические характеристики и т. д.), целесообразно использовать присадочный металл того же состава, что и основной. Однако из-за повышенной склонности большинства сплавов алюминия к кристаллизационным трещинам более рационально применять присадочный материал, который, отличаясь по составу от свариваемого сплава, обеспечил бы проведение эффективного комплексного легирования с использованием модификаторов.
[c.371]
При аргоно-дуговой сварке неплавящимся электродом (рис. У.14) через специальную горелку 4, в которой установлен вольфрамовый электрод 3, пропускают нейтральный газ — аргон (или гелий). Возбуждение дуги происходит между электродом и свариваемым изделием. Для заполнения разделки кромок в зону вводят присадочный пруток 2, химический состав которого близок к составу основного металла. Применяют электроды диаметром 2—6 мм. Аргон подается в горелку под давленпем 0,3—0,5 ат (0,03—0,05 МПа). Аргоно-дуговая сварка применяется для сварки легированных сталей, алюминия и его сплавов, титана, магниевых сплавов и дает хорошие результаты.
[c.275]
В качестве электродов или присадочного материала при сварке чистого алюминия и его сплавов используют прутки или проволоку, по химическому составу близкие к свариваемому металлу. В покрытия электродов или в флюс вводят хлористые и фтористые соли лития, калия, энергично растворяющиеся и ошлаковывающие оксид алюминия. Сварку ведут постоянным током обратной полярности, [c.79]
Сварка алюминия и его сплавов. Алюминий и его сплавы хорошо свариваются газовой сваркой только нормальным пламенем. Присадочную проволоку применяют такого же состава, как свариваемый металл. Для удаления пленки оксида алюминия используют флюсы АФ-4А, АН-4А, АН-А201, содержащие хлористые и фтористые соли лития, натрия, калия и бария. После сварки остатки флюса удаляют горячей водой. Оксидную пленку можно удалять так же, как при дуговой сварке, специальным скребком. В этом случае сварщик должен иметь большой навык, так как в шов могут попадать остатки оксидной пленки и вызывать не-сплавление металла.
[c.85]
ЭШС алюминия и его сплавов. Электрошлаковую сварку алюминия и его сплавов целесообразно осуществлять прн толщине металла свыше 40 мм. В этом случае экономический эффект составляет более 50 % затрат, имеющих место при многопроходипй механизированной дуговой сварке. С увеличение1М толщины свариваемого металла, как и при сварке других цветных металлов и сплавов, технико-экономическая эффективность процесса сварки возрастает. [c.492]
При газовой сварке алюминия и его сплавов пламя берется нормальное. Избыток кислорода и горючего газа не допускается, так как свободный кислород окисляет алюминий, а избыток горючего газа приводит к сильной пористости шва. Мощность сварочиого пламени выбирается из расчета расхода ацетилена 75 дм ч на 1 мм толщины свариваемого изделия. Расход ацетилена в зависимости от толщины свариваемого металла приведен ниже [c.261]
Основной трудностью при сварке алюминия является образование на поверхности алюминия тугоплавкой окис-ной пленки А1гОз с температурой плавления 2060° С, которая затрудняет плавление металла и сплавление свариваемых кромок. Другая трудность заключается в том, что при нагреве алюминий не меняет своего цвета и поэтому трудно уловить момент начала его плавления. От сваршика требуется большой навык и опыт по сварке алюминия и его сплавов. [c.92]
Влияние водорода на сварные соединения из алюминия гораздо сильнее, чем на медь и ее сплавы, так как растворимость водорода ничтожна в твердом алюминии и его сплавах, а изменение ее в процессе кристаллизации очень велико. В отличие от меди, алюминий почти не растворяет свой тугоплавкий окисел А1гОз, который всегда образуется на свариваемых кромках и на присадочном металле. Окисные включения (пленки) способствуют зарождению газовых пузырей и образованию пор. [c.335]
Свариваемость стали с алюминием и его сплавами
Рекомендуем приобрести:
Установки для автоматической сварки продольных швов обечаек — в наличии на складе!
Высокая производительность, удобство, простота в управлении и надежность в эксплуатации.
Сварочные экраны и защитные шторки — в наличии на складе!
Защита от излучения при сварке и резке. Большой выбор.
Доставка по всей России!
Применение комбинированных сварных узлов из стали и алюминия или его сплавов в конструкциях различного назначения (в судостроении, авиационной и химической промышленности, машиностроении, вагоностроении, кислородном аппаратостроении и пр.) весьма перспективно, так как этим достигается наибольшая эффективность работы конструкции при одновременном значительном снижении веса. Однако промышленного способа непосредственного соединения сваркой стали с алюминием или его сплавами пока нет. Существующие методы сварки обеспечивают прочность такого сварного соединения лишь на уровне прочности чистого алюминия. Это объясняется плохой свариваемостью алюминия со сталью.
Ниже приведены химико-физические свойства железа и алюминия:
Сопоставление кристаллохимических и физических свойств алюминия и железа свидетельствует о значительной их разнице. Несоответствие типов кристаллических решеток Fe-α и Аl (различие в параметрах ~ 22%) и близость атомных радиусов при резко отличных значениях атомного веса объясняют ограниченную взаимную растворимость этих металлов. Так, растворимость Fe в Аl ничтожна и при температуре 655° С составляет всего лишь 0,052%, а при 400°Сблизка к нулю. Разницей в электрохимических свойствах алюминия и железа можно объяснить способность этих металлов образовывать интерметаллические соединения. Кроме интерметаллида FeAl3, с увеличением в системе железа появляются соединения Fe2Al7, Fe2Al5, FeAl2, FeAl и другие, а на основе FeAl3 — эвтектика Al+FeAl3 с температурой плавления 655° С. По мере введения железа в алюминий непрерывно повышается предел прочности и твердость; пластичность сплавов резко снижается и при 12% Fe падает до нуля.
Разница в физических свойствах алюминия и железа также весьма существенна большое различие температур плавления, коэффициентов линейного расширения, теплопроводности и тепло емкости, наличие окисной пленки Аl2O3, создающей включения в сварном шве, ухудшают свариваемость этих металлов.
Однако основной проблемой свариваемости алюминия со сталью следует считать образование в зоне сплавления диффузионного слоя из хрупких и твердых интерметаллидных фаз типа FenAlm, снижающих технологическую и эксплуатационную прочность, а также коррозионную стойкость сварного соединения.Исследования фазового состава диффузионных слоев, возникающих в зоне сплавления стали с алюминием, показали, что по мере удаления от стали в глубь алюминиевого шва последовательность расположения фаз такая; Fe-α;FeAl5; Fe2Al5 + FeAl3; FeAl3; Al. При этом интерметаллид Fe2Al5(55% Al) — наиболее твердый (HV 1000—1100) и хрупкий, а у FeAl5 (59% Al) твердость и хрупкость несколько ниже (HV 820—980).
В результате многочисленных испытаний на прочность стале-алюминиевых соединений выяснилось, что их прочность тем выше, чем меньше толщина интерметаллидного слоя. Из этих соображений иногда допускают наличие слоя из интерметаллидных фаз, но не глубже 5 мкм, так как в более толстых слоях возникают поры и трещины, резко снижающие его прочность.
Пути решения сложной проблемы свариваемости стали с алюминием и его сплавами такие:
1) предварительно покрывать стальную составляющую алюминием, цинком или другими металлами, чтобы разобщить алюминиевую ванну со сталью;
2) легировать алюминиевую ванну различными добавками, замедляющими развитие диффузионных процессов в зоне ее контакта со сталью;
3) использовать для соединения алюминия со сталью вставки из биметалла (рис. 243).
Предварительно покрыть сталь некоторыми металлами можно гальванически или горячим погружением. Но получить сталеалюминиевые сварные соединения нужной прочности так не удается, поскольку и в этом случае успевают сформироваться прослойки из интерметаллидов той или иной толщины. Наиболее удовлетворительные результаты получены при нанесении комбинированных медно-цинкового и особенно никелево-цинкового покрытий.
Менее изучено влияние легирующих добавок. Известно, например, что если стальная поверхность оцинкована, то внесение в сварочную ванну Cu, Zn, и особенно Si, позволяет значительно уменьшить ширину иитерметаллидного слоя за счет снижения диффузионной подвижности атомов алюминия в железе. Наличие же Mg отрицательно влияет на свариваемость алюминия со сталью, так как магний резко увеличивает рост выпавших интерметаллидов.
Предотвратить образование хрупких интерметаллидных фаз можно лишь используя для соединения алюминия со сталью вставки из прокатанного биметалла (рис. 243). В этом случае свариваются между собой однородные металлы — сталь 1 со сталью и алюминий 2 с алюминием, но так, чтобы степень проплавления металла вставки не приближалась к границе схватывания более, чем это допустимо. Существенный недостаток таких соединений — неконструктивность сварных узлов.
Частые вопросы о сварке алюминия
Здесь мы постарались дать ответы на самые частые вопросы на тему сварки алюминия:
- Почему наплавленный металл имеет намного меньшую прочность по сравнению с основным?
- Какой защитный газ использовать для сварки алюминия?
- Какие электроды подходят для TIG-сварки алюминия?
- Как проводить предварительный подогрев перед сваркой алюминия?
- Как снимается остаточное напряжение после сварки алюминия?
- Как различать сплавы алюминия?
- Как вести сварку по алюминию переменной толщины?
-
Как вести сварку сплава 7075?
1. Почему наплавленный металл имеет намного меньшую прочность по сравнению с основным?
При сварке стали наплавленный металл можно сделать таким же прочным, как и основной. Но для алюминия это не так. Почти во всех случаях сварки алюминия наплавленный металл имеет меньшую прочность.
Чтобы лучше понять, из-за чего это происходит, давайте рассмотрим два типа алюминиевых сплавов: с тепловой обработкой и без нее. Для упрочнения сплавов второй категории проводится только холодная обработка, которая вызывает определенные физические изменения металла. Чем интенсивнее холодная обработка, тем прочнее становится сплав.
Но во время сварки сплава, прошедшего холодную обработку, вы производите локальный отжиг материала, он теряет закаливание и становится «мягким». Поэтому при сварке сплавов, не проходивших тепловую обработку, создать такой же прочный наплавленный металл, как и основной, можно только при условии изначально незакаленного материала.
При тепловой обработке алюминиевых сплавов на последнем этапе они нагреваются примерно до 200°C. Однако во время сварки материал в зоне теплового воздействия нагревается значительно выше этой отметки, и из-за этого теряет свои механические свойства. Поэтому, если после сварки не провести подогрев материала, зона вокруг соединения станет значительно менее прочной по сравнению с остальным алюминием — примерно на 30-40%. Если подогрев проводится, то он позволит улучшить характеристики сплава.
Ниже указано, какие серии алюминиевых сплавов проходят тепловую обработку, а какие — нет:
Проходят тепловую обработку: 2000, 6000, 7000.
Не проходят тепловую обработку: 1000, 3000, 4000, 5000.
2. Какой защитный газ использовать для сварки алюминия?
Для TIG (аргонодуговой) и MIG (в защитных газах) сварки материалов толщиной до 12,7 мм рекомендуется чистый аргон. При толщине выше 12,7 мм в смесь можно добавить от 25 до 75 процентов гелия, чтобы увеличить температуру дуги и глубину проплавления. Аргон подходит для этого лучше всего, потому что он обеспечивает более качественное очищающее действие дуги по сравнению с гелием и меньше стоит.
Никогда не используйте газовые смеси с содержанием кислорода или двуокиси углерода, так как это приведет к окислению алюминия.
3. Какие электроды подходят для TIG-сварки алюминия?
Для большинства материалов, в том числе стали, рекомендуется использовать электроды с 2-процентным содержанием тория. Но так как сварка алюминия происходит на переменном токе, а не постоянном, на вольфрамовый электрод поступает больше энергии. По этой причине для сварки алюминия рекомендуются электроды из чистого вольфрама или с добавлением циркония.
Кроме того, для сварки на переменном токе требуются электроды значительно большего диаметра. Рекомендуем начать с диаметра 3,1 мм и при необходимости попробовать другие варианты. Вольфрам с добавлением циркония позволяет работать на более высоких токах, чем чистый вольфрам. Также учтите, что при сварке на переменном токе удобнее работать электродом с затупленным концом — из-за острого конца дуга может отклоняться в стороны.
4. Как проводить предварительный подогрев перед сваркой алюминия?
Хотя предварительный подогрев в определенных пределах довольно полезен, слишком сильный нагрев может отрицательно сказаться на механических свойствах алюминия.
Как уже было упомянуто ранее, на последнем этапе тепловой обработки алюминий нагревается до 200°C, поэтому, если перед сваркой оператор нагреет алюминий до 175°C и будет удерживать эту температуру на протяжении всей работы, механические свойства алюминия снизятся.
В случае сплавов без тепловой обработки, например, серии 5000, даже если ограничить температуру до 90°C, материал окажется уязвим к коррозии под напряжением. В большинстве случаев небольшой предварительный подогрев для удаления влаги считается приемлемым, но он должен быть строго ограничен.
Многие неопытные сварщики воспринимают предварительный подогрев как некий костыль. Так как оборудование для сварки алюминия часто работает на максимальной мощности, считается, что подогрев поможет преодолеть ограничения оборудования. Алюминий имеет достаточно низкую температуру плавления — 650°C по сравнению с 1420°C для стали. Из-за низкой температуры плавления кажется, что для сварки алюминия нужно оборудование минимальной мощности. Но при этом алюминий имеет в 5 раз более высокую теплопроводимость по сравнению со сталью, т. е. тепло в этом случае рассеивается намного быстрее. Поэтому ток и напряжение для сварки алюминия должны быть еще выше, чем для стали, что требует использования более мощного оборудования.
5. Как снимается остаточное напряжение после сварки алюминия?
Из-за того, что расплавленный металл по мере застывания сжимается, в зоне сварки образуется остаточное напряжение. Более того, если после сварки изделие подвергнется механической обработке, это еще больше усилит деформации и разброс размеров. Чтобы этого избежать, сварщики проводят снятие напряжения, то есть нагревают материал до такой степени, чтобы атомы алюминия смогли более свободно перемещаться.
Если для стали температура снятия напряжения составляет 565-590°C, то для алюминия она ограничена 343°C. Это означает, что для того, чтобы снятие напряжения было хоть сколько-нибудь эффективным, материал придется нагреть до температуры, при которой он потеряет механические свойства. Поэтому для алюминия снятие напряжение после сварки не рекомендуется.
6. Как различать сплавы алюминия?
Существует достаточно много различных сплавов алюминия и для надежной сварки нужно знать, с каким сплавом вы работаете. Если эта информация недоступна, вы можете ориентироваться на следующее:
штампованные изделия обычно выполняются из сплавов серии 6000;
литые изделия часто представляют собой сочетание алюминия/кремния — некоторые из них поддаются сварке, некоторые — нет;
листовой металл, пластины и болванки обычно изготавливаются из сплавов 5000 и 6000;
Если вам нужна более точная информация, приобретите комплект для анализа, который поможет вам определить точный состав сплава.
7. Как вести сварку по алюминию переменной толщины?
Если вам требуется вести сварку по материалу переменной толщины, оборудование следует настроить для сварки части с самым большим сечением. Во время сварки будьте осторожны и сделайте большее тепловложение в части с большим сечением.
8. Как вести сварку сплава 7075?
Большинство сплавов алюминия поддается сварке, но некоторые для этого подходят плохо — в частности, сплав 7075. Мы выделили в этом примере именно 7075, потому что этот сплав имеет одно из самых высоких значений предела прочности. Когда проектировщики и сварщики начинают подбирать сплав алюминия, многие в первую очередь обращаются к таблице со сплавами алюминия и их пределами прочности. Но они не знают, что лишь немногие из сплавов с высокой ударной вязкостью поддаются сварке, особенно если они относятся к сериям 7000 и 2000, и их использования следует избегать.
Единственное исключение — это отрасль литья под давлением. В этом случае для ремонта штампов проводится сварка алюминия 7075 — однако он никогда не используется для изготовления металлоконструкций.
При выборе подходящего сплава алюминия можно опираться на следующие рекомендации:
Серия сплава | Основные элементы сплава |
Серия 1000 | Чистый алюминий |
Серия 2000 | Алюминий и медь (высокопрочный алюминий для аэрокосмической отрасли) |
Серия 3000 | Алюминий и марганец (сплавы с низкой и средней прочностью, например, используются в алюминиевых банках и трубах систем охлаждения) |
Серия 4000 | Алюминий и кремний (большинство сплавов этой серии — это заполняющие материалы для сварки и припоя) |
Серия 5000 | Алюминий и магний (эти сплавы в основном используются для создания металлоконструкций из листового материала и пластин — все сплавы серии 5000 пригодны для сварки) |
Серия 6000 | Алюминий, магний и кремний (эти сплавы поддаются тепловой обработке и часто используются для производства штампованных изделий, листового металла и пластин — все поддаются сварке, но могут быть склонны к растрескиванию. Не пытайтесь проводить сварку этих сплавов без буферного слоя) |
Серия 7000 | Алюминий и цинк (высокопрочные сплавы для аэрокосмической отрасли, которые могут содержать другие элементы). |
Если вам необходимо использовать высокопрочный алюминий, компания Lincoln рекомендует использовать сплавы серии 5000 с высоким содержанием магния вместо серий 2000 и 7000. Сплавы серии 5000 хорошо поддаются сварке и обеспечивают самые лучшие результаты.
Заключение
Компания Lincoln Electric предлагает полный спектр решений для сварки алюминия, например, аппараты Power Wave® 455M, специально разработанные для эффективной сварки алюминия, пуш-пульные механизмы Cobramatic® для подачи мягкой алюминиевой проволоки и сварочную проволоку SuperGlaze® премиум-класса со строгим контролем химического состава для стабильного качества сварки. Кроме широкого выбора продуктов, компания Lincoln гордится своим опытом работы с алюминием. Если вам нужен совет, напишите нам.
Сварка алюминия и его сплавов
Сварка алюминия и его сплавов
Категория:
Сварка различных металлов
Сварка алюминия и его сплавов
Алюминий обладает низкой прочностью; поэтому его не применяют для конструкций, работающих под динамической нагрузкой. Его употребляют в химическом аппарато-строении, рамных конструкциях, для оконных и дверных переплетов и декоративных изделий в строительстве. Он обладает малой массой (плотность 2,7 г/см3), повышенной коррозионной стойкостью и большой пластичностью по сравнению с низкоуглеродистой сталью.
Повышенную прочность имеют сплавы алюминия с марганцем, магнием, кремнием, цинком и медью.
Алюминий и его сплавы делят на литейные и деформируемые (катаные, прессованные, кованые). Деформируемые сплавы подразделяют на термически не упрочняемые, к которым относятся сплавы алюминия с марганцем и магнием, и термически упрочняемые, к которым относятся сплавы алюминия с медью, цинком, кремнием.
Наиболее высокой прочностью обладают термически упрочняем мые алюминиевые сплавы. Например, механические свойства дюр алюминия Д16 (3,8—4,9% меди, 1,2—1,8% магния, 0,3—0,9% мар ганца, остальное — алюминий) следующие: до термической обра-ботки — 6В = 22 кгс/мм2 и 6б = 2%; после термической обработки ств=42 кгс/мм2 и 65=18%. Наибольшей прочностью из термиче ски упрочняемых алюминиевых сплавов обладает сплав В95 (ав = 60 кгс/мм2, огт = 55 кгс/мм2 и 65 — около 12%), сплав по, строен на основе алюминий — медь — магний — цинк.
Однако термически упрочненные алюминиевые сплавы разуп рочняются при сварке со значительной потерей механических свойств. Применение этих сплавов для сварных конструкций воз» можно лишь при условии обеспечения термической обработки после сварки для повышения прочности сварных соединений.
Из термически неупрочняемых сплавов наибольшей прочностью обладают сплавы системы А1 — Mg — Ti, например сплав АМгб, механические свойства которого следующие: сгв = 32—38 кгс/мм2, стт = 1 б— 18 кгс/мм2, бБ= 15—20% и ак=3—4 кгс-м/см2. Конструкции из алюминиево-магниевого сплава АМгб изготовляются в основном сварными.
Свариваемость алюминия и его сплавов. Алюминий и его сплавы имеют большую теплопроводность, теплоемкость и скрытую теплоту плавления. Теплопроводность алюминия в три раза выше теплопроводности низкоуглеродистой стали; при нагреве от 20 до 600° С разница в теплопроводности еще более возрастает. Следовательно, сварка алюминия и его сплавов должна выполняться с относительно мощным и концентрированным источником нагрева.
Коэффициент линейного расширения алюминия в два раза выше, чем коэффициент расширения железа. Это способствует увеличенным деформациям и короблению при сварке алюминиевых изделий.
Низкая удельная плотность (2,7 г/см3) и температура плавления (660° С) алюминия по сравнению с высокой удельной плотностью окисла алюминия А120э (3,85 г/см3) и его температурой плавления (2060° С) затрудняют процесс сварки. Тугоплавкий и тяжелый окисел AI2O3 может оставаться в металле шва и снижать работоспособность сварного соединения. При сварке алюминия и его сплавов необходимо применять различные способы борьбы с окислом А1203. Во всех случаях поверхность металла изделия должна зачищаться непосредственно перед сваркой и процесс сварки должен протекать с защитой расплавленного металла от действия газов воздуха.
Используют три способа борьбы с окислом алюминия: сварка с растворителем окислов (электродные покрытия, флюсы), сварка без растворителей, но с так называемым катодным распылением, и сварка с механическим удалением окислов из сварочной ванны.
Растворителями окисла А1203 и других окислов являются галоидные соли щелочноземельных металлов (хлористый, фтористый литий и др.), которые растворяют окислы и вместе с ними подни-1аЮтся из сварочной ванны в сварочный шлак. Так как раствор обладает пониженной температурой плавления, меньшей удельной плотностью и меньшей вязкостью, чем каждый компонент в отдельности, то он выводится из металла шва в сварочный шлак.
Сущность катодного распыления состоит в том, что при дуговой сварке в аргоне на постоянном токе при обратной полярности происходит дробление окисной пленки А1203 с последующим распылением частиц окисла на поверхности сварного изделия. Тонкая окисная пленка, покрывающая сварочную ванну, разрушается под ударами тяжелых положительных ионов защитного газа аргона, образующихся при горении дуги. Так как положительный ион обладает большей массой, чем электрон, то образующийся поток ионов способен дробить окнсные пленки алюминия и магния, которые создаются при сварке. При этом надо учитывать большую скорость движения ионов, позволяющую распыленным окислам через защитную газовую среду выходить из сварочной зоны.
Другие газы, обладающие низкой атомной массой (например, 4 у гелия вместо 40 у аргона), не способны дробить и распылять окислы.
Механический способ удаления окисла А1203 из сварочной ванны заключается в том, что сварщик опускает в сварочную ванну стальной пруток диаметром 3—4 мм и вынимает его с прилипшим к поверхности прутка окислом, который легко отделяется от прутка при его встряхивании и легком ударе. Опытные рабочие, выполняющие газовую или дуговую сварку угольным электродом, часто используют этот способ, не прибегая к флюсам.
Алюминиевые сплавы обладают повышенной склонностью к образованию пор. Пористость металла при сварке алюминия и его сплавов вызывается водородом, источником которого служит адсорбированная влага на поверхности основного металла и особенно проволоки, а также воздух, подсасываемый в сварочную ванну. В этом случае алюминий в сварочной ванне взаимодействует с влагой по реакции 2А1+ЗН20->-А120з+6Н.
Для получения беспористых швов при сварке алюминия и его сплавов даже небольшой толщины иногда требуется подогрев, снижающий скорость охлаждения сварочной ванны и способствующий более полному удалению водорода из металла при медленном охлаждении. Так, например, при наплавке на лист алюминия толщиной 8 мм беспористый шов может получить при подогреве металла до 150 °С. При увеличении толщины металла до 16 мм даже подогрев до температуры 300 °С не обеспечивает беспористых швов.
Однако подогрев листов для сварки некоторых сплавов следует применять осторожно. Например, при сварке толстолистовых алю-миниево-магниевых сплавов допускается подогрев до температуры не выше 100—150 °С. Более высокая температура подогрева может усилить пористость шва за счет выделения из твердого раствора магния и образования при этом водорода по реакции Mg + h30-vMg0 + 2H. Кроме того, при сварке подогретого металла
Флюс АФ-4а разводят дистиллированной водой и наносят на свариваемые кромки и присадочный пруток.
При газовой сварке применяют присадочную проволоку той же марки, что и свариваемый металл.
Для получения и сохранения мелкозернистой структуры изделие после сварки в некоторых случаях, например при сварке литых деталей, подвергают отжигу при 300—350 °С с последующим медленным охлаждением.
—-
Алюминий обладает малой плотностью, хорошей тепло- и электропроводностью, высокой коррозионной стойкостью и пластичностью. В технике алюминий применяют в виде алюминия разной степени чистоты и в виде сплавов.
В зависимости от содержания примесей (Fe, Si, Си, Zn, Ti) алюминий бывает особой чистоты А999 (0,001 % примесей), высокой чистоты А995, А99, А97, А95 (0,005—0,5% примесей) и технической чистоты А85, А8 и др. (0,15—1,0% примесей). Технический алюминий, выпускаемый в виде деформируемого полуфабриката (листы, профили, прутки и др.), используют в сварных конструкциях, маркируется АД0 и АД1.
Из-за низкой прочности (сгв=804-110 МПа) алюминий применяют для ненагруженных деталей и элементов конструкций, когда от материала требуется легкость, свариваемость, пластичность, коррозионная стойкость (рамы, двери, трубопроводы, емкости, фольга и др.). Для нагруженных изделий используют сплавы алюминия. В качестве основных легирующих элементов алюминиевых сплавов применяют Си, Mg, Si, Mn, Zn, реже — Li, Ni, Ti, Be, Zr.
Алюминиевые сплавы классифицируют по технологии изготовления, способности к термической обработке и свойствам. В зависимости от технологии изготовления различают деформируемые (для полуфабрикатов и изделий обработкой давлением), литейные (для отливок) и спеченные сплавы. По способности к термической обработке они разделяются на термические неупрочняемые и термические упрочняемые.
К литейным сплавам относятся сплавы системы А1—Mg, А1— Si, А1—Си. Наиболее распространенными литейными сплавами с повышенным содержанием кремния (от 4 до 13%) являются силумины. Сварку литейных сплавов выполняют при ремонтных работах.
Материалы из спеченной алюминиевой пудры (САП) и спеченных алюминиевых сплавов (САС) состоят из порошков алюминия или его сплавов и окиси алюминия. Получают САП и САС последовательным брикетированием, спеканием и прессованием окисленной с поверхности алюминиевой пудры. Эти материалы свариваются очень плохо.
Сварные конструкции изготовляют из деформируемых алюминиевых сплавов. К деформируемым сплавам, не упрочняемым термообработкой, относятся алюминиевомарганцевый сплав АМц(А1+ 1,3%Мп) и группа сплавов системы А1—Mg (магналий): АМг, AMr1, АМг2, АМгЗ, АМг5В, АМг6. Эти сплавы обладают хорошей свариваемостью, в сварных соединениях они способны сохранять до 95% прочности основного металла при высокой пластичности и высокой коррозионной стойкости. алюминием (р=3,85 г/см3). Окисная пленка затрудняет сплавление, способствует непроварам и охрупчивает металл. Поэтому окисную пленку удаляют со свариваемых кромок механическими и химическими способами перед сваркой, во время сварки защищают зону сварки инертным газом, катодным распылением, применяют покрытия и флюсы на основе солей щелочных и щелочноземельных металлов (NaCl, NaF, КС1 и др.).
2. Склонность к образованию горячих трещин в связи с большой литейной усадкой кристаллизующегося металла, грубой столбчатой структурой сварного шва и наличием примесей. Для борьбы с горячими трещинами ограничивают содержание примесей в свариваемом металле, для измельчения структуры добавляют в металл и сварочную .проволоку модификаторы (Zr, Ti, В), регулируют режимы сварки.
3. Термически упрочняемые сплавы весьма чувствительны к термическому циклу сварки в связи с ростом зерна, распадом перенасыщенных твердых растворов, процессами старения, рекристаллизацией.
4. Для ряда сплавов, особенно содержащих в качестве основного легирующего элемента магний, характерна повышенная пористость при сварке, связанная с насыщением расплавленного металла водородом. Для уменьшения пористости рекомендуется тщательная подготовка свариваемых кромок и проволоки перед сваркой для удаления следов влаги с их поверхности; тщательная защита сварочной ванны, увеличение диаметра присадочной проволоки, чтобы уменьшить удельную поверхность присадки; предварительный подогрев, чтобы увеличить время существования сварочной ванны и чтобы пузырьки водорода успели выйти из ванны.
5. Высокие теплопроводность и теплоемкость алюминия требуют применения мощных источников тепла, а в ряде случаев подогрева. Высокий коэффициент линейного расширения и малый модуль упругости способствуют появлению значительных сварочных деформаций, что требует применения надежных зажимных приспособлений и устранения деформаций после сварки в ответственных конструкциях. В алюминии отсутствует пластическое состояние при нагреве и переходе из твердого в жидкое состояние, при этом алюминий не меняет своего цвета, а в области температур более 400—450 °С имеется провал прочности и пластичности, поэтому рекомендуется сварка на подкладках.
Высокий коэффициент вязкости и быстрый теплоотвод затрудняют формирование шва, поэтому требуется соблюдение необходимых разделок кромок. Все перечисленные трудности и особенности свар-; ки алюминия требуют тщательной подготовки под сварку и тщательное соблюдение технологии сварки.
Способы сварки алюминия и его сплавов. Основными способами сварки алюминия и его термонеупрочняемых сплавов являются сварка в инертных газах, по флюсу и под флюсом, ручная покрытыми электродами, контактная. Используют также газовую сварку, электрошлаковую сварку угольным электродом. Для термически упрочняемых сплавов применяют преимущественно механизированные способы сварки в инертных газах, электронно-лучевую, плаз-менно-дуговую.
Для тонколистового металла целесообразна сварка в импульсном режиме. Для толстолистового металла (6>10 мм) хорошие результаты дает трехфазная сварка неплавящимся электродом. Сварку плавящимся электродом в инертных газах выполняют при толщинах более 4 мм на постоянном токе обратной полярности /св = (120-г-160)da, где da — диаметр сварочной проволоки. Недостатком сварки плавящимся электродом является повышенная пористость.
Газовую сварку выполняют нормальным пламенем с использованием защитного флюса в виде порошка или пасты, наносимого на свариваемые кромки и присадочной проволоки типа АФ-4А (КО— 50%, LiCl — 14%, NaCl—28%. NaF—8%), с подогревом металла при сварке больших толщин. Ориентировочную мощность сварочного пламени выбирают из расчета расхода ацетилена 75 дм3/ч на 1 мм толщины свариваемого металла.
При использовании флюсовой защиты применяют следующие способы электрической сварки плавлением: дуговую автоматическую по флюсу и под флюсом и электрошлаковую. При сварке по слою флюса используют флюсы на основе солей щелочных и щелочноземельных металлов (например, АН-А1 системы Na3AlF3—КС1—NaCl), которые обладают высокой электропроводностью, поэтому погруженная дуга закорачивается и горит по слою флюса. Дополнительным параметром режима при сварке по слою флюса является высота насыпного слоя флюса перед дугой. Добавление во флюсы для сварки алюминия компонентов, уменьшающих электропроводность флюса, позволило разработать способ сварки под слоем флюса. В качестве такого компонента во флюс ЖА-64 введен кремнезем SiOa (система Na3AlF3—КС1—NaCl—Si02).
Контактную точечную и шовную сварку применяют для соединения листов и профильного проката преимущественно из деформируемых сплавов. Контактную стыковую сварку выполняют преимущественно методом оплавления. Тацгкак алюминий и его сплавы отличаются высокой тепло- и электропроводностью, то необходимо при электроконтактной сварке, особенно точечной, применение больших токов и мощных машин, для повышения эффективности нагрева целесообразно сваривать при малой длительности импульсов тока.
Пластичные сплавы алюминия хорошо свариваются другими видами сварки термомеханического и механического классов.
Реклама:
Читать далее:
Сварка титановых сплавов
Статьи по теме:
ТЕХНОЛОГИЧЕСКИЕ СВОЙСТВА И СВАРИВАЕМОСТЬ ЛИСТОВ АЛЮМИНИЕВОГО СПЛАВА СИСТЕМЫ Al-Mg-Si-Fe, СОДЕРЖАЩЕГО ЛЕГИРУЮЩИЕ ДОБАВКИ ЩЕЛОЧНОЗЕМЕЛЬНЫХ МЕТАЛЛОВ
ТЕХНОЛОГИЧЕСКИЕ СВОЙСТВА И СВАРИВАЕМОСТЬ ЛИСТОВ АЛЮМИНИЕВОГО СПЛАВА СИСТЕМЫ Al—Mg—Si—Fe, СОДЕРЖАЩЕГО ЛЕГИРУЮЩИЕ ДОБАВКИ ЩЕЛОЧНОЗЕМЕЛЬНЫХ МЕТАЛЛОВ
Грушко О.Е., Гуреева М.А., Фридляндер И.Н., Овчинников В.В.
(ФГУП «ВИАМ», ФГУП «РСК «МиГ», г.Москва, РФ)
Получение изделий сложной конфигурации и повышенной прочности по технологии, включающей операции штамповки с глубокой вытяжкой и сварки (подвесные баки, аккумуляторные баки, баллоны, бачки и др.) остается актуальной проблемой для самолетостроения и автомобильной промышленности. Сплавы системы Al-Mg-Si типа авиаль заметно превосходят по своим механическим свойствам, используемые в настоящее время для этих целей, сплавы системы Al-Mg. Предлагаемые сплавы имеют следующие механические свойства: σ0.2 = 270 МПа, σв = 360 МПа, σкр.=0,9 σ0.2 , МЦУ более 100 Кц при σmax =157 МПа. В то же время у сплавов АМг2 и АМг6 значения σ0.2 равны 120 и 180 МПа, соответственно. Помимо этого, листы из сплавов системы Al-Mg-Si-Fe значительно более герметичны, по сравнению со сплавами системы Al-Mg. Это позволяет использовать значительно более тонкие листы для изготовления герметичных изделий, что существенно снижает массу конструкции (самолета или автомобиля).
Достижение хорошей способности листов из сплавов системы Al-Mg-Si-Fe к формоизменению и сварке возможно только в случае формирования в них оптимизированных структурных состояний (однородная мелкозернистая структура, благоприятная текстура, наличие дисперсных выделений упрочняющих фаз, сдерживающих также рост зерен и возникновение вредных кристаллографических ориентировок). Выполненные нами исследования эволюции структуры, процессов текстурообразования, протекающих в технологическом цикле изготовления листов из сплавов типа авиаль, и влияния на них добавок щелочноземельных металлов, позволили предложить сплав (В1341), по своим характеристикам превосходящий обычные сплавы системы Al-Mg-Si-Fe [1].
В настоящее время ставится задача применения этого сплава для изготовления указанных выше изделий и возникает необходимость более детального изучения его технологических характеристик таких, как формуемость при штамповке с глубокой вытяжкой, способность к гибке, свариваемость и др.
Возможность получения деталей типа полусфер из листов сплава В1341 при холодной штамповке оценивали на образцах в виде дисков диаметром 200 мм. Для холодной штамповки использовали доработанный штамп, применяемый для штамповки днищ расширительного бака из сплава АМг4. Штамповку выполняли за один ход штампа. Для штамповки днищ использовали пресс марки PKNT315 фирмы WEINORTEN. Данный пресс имеет рабочий ход 315 мм; усилие удерживания 500 КН; усилие выталкивания 80 КН.
Были получены детали в виде полусфер диаметром 150 мм (с технологическим припуском) и высотой 60 мм (рис.1) . Внешним осмотром полученных полусфер установлено отсутствие видимых трещин и морщин на их поверхности. Это позволяет заключить, что сплавы системы Al-Mg-Si обладают хорошей технологичностью после ТМО в условиях холодной штамповки. Это позволяет получать из него различные гофрированные панели.
Рисунок 1 — Днища баллонов с технологическим припуском после холодной штамповки из листа сплава В1341
Для изготовления различных герметичных конструкций (типа баллонов и баков) наибольший интерес представляет сварка плавлением сплава В1341и уровень свойств получаемых соединений. Для получения сварных соединений листов сплава В1341 использовали установку для автоматической сварки на базе АДСВ-7, оснащенную клавишным пневматическим приспособлением для фиксации деталей и источником переменного тока марки ИСВУ-400. Сварку осуществляли на токе дуги 60-75А при скорости сварки 12-15 м/ч. Присадочную проволоку диаметром 1,2 мм подавали в сварочную ванну со скоростью 20-22 м/ч. Защиту расплавленного металла сварочной ванны и проплава шва осуществляли аргоном. При сварки образцов использовали присадочную проволоку марки Св.1217, Св.АК5 и Св.АМг63.
На первом этапе исследований свариваемости сплавов системы Al-Mg-Si-Fe определялось влияние содержания кальция на склонность сплава к образованию трещин. Сварку образцов осуществляли без присадки и с присадочной проволокой. Для оценки склонности сплава к образованию трещин использовали крестовую пробу, пробу «рыбий скелет» (образцы Хоулкрофта) и методику испытаний на машине ЛТП1-10. Анализ полученных результатов показал, что введение в сплав кальция позволяет снизить коэффициент трещинообразования и существенно повысить критическую скорость деформации. При этом оптимальное количество кальция составляет 0,12-0,35%. Применение присадочной проволоки дополнительно снижает склонность сплава к образованию трещин при сварке плавлением. Примененные проволоки (св.АК5, св.1217, св.АМг63) примерно равноценны по влиянию на склонность сплава к образованию трещин при сварке.
Результаты механических испытаний сварных соединений, полученных с использованием различных марок присадочных проволок, представлены в табл.1. Анализ данных табл.1 показывает, что прочность сварных соединений, испытанных с проплавом и усилением шва, а также со снятым проплавом и усилением при использовании проволок Св.1217, Св.АК5 и АМг63, практически одинакова и составляет 0,60-0,62 от предела прочности основного металла в состоянии Т1. Разрушение образцов, сваренных в закаленном состоянии, при испытании на статическую прочность происходит по основному металлу на расстоянии 6-10 мм от линии сплавления. В то же время значения угла загиба у соединений, выполненных с проволокой Св.АК5, примерно в 2-3 раза меньше, чем у соединений, сваренных с проволокой Св.1217.
Таблица 1 – Механические свойства сварных соединений листов сплава В1341, выполненных автоматической аргонодуговой сваркой
Образец |
Марка проволоки |
Термообработка |
σв, МПа |
σ02, МПа |
δ, % |
α, град |
|
соединение |
шов |
||||||
Основной металл |
нет |
З |
296 |
— |
176 |
25,8 |
— |
З + ИС |
332 |
— |
309 |
10,6 |
— |
||
Сварное соединение |
Св.1217 |
З + ИС + Св. |
206 |
207 |
114/129 |
7,3/5,8 |
62 |
З + Св. + ИС |
284 |
284 |
185/228 |
1,0/1,8 |
32 |
||
Св.АК5 |
З + ИС + Св. |
226 |
217 |
115/132 |
7,8/6,2 |
30 |
|
З + Св. + ИС |
304 |
282 |
210/264 |
0,9/1,6 |
13 |
||
Св.АМг63 |
З + ИС + Св. |
224 |
220 |
123/143 |
6,9/4,7 |
44 |
|
З + Св. + ИС |
290 |
250 |
199/234 |
1,0/2,2 |
23 |
||
Примечание: 1. Обозначения: З – закалка, ИС – искусственное старение, Св. – сварка. 2. Числитель – база измерения 15 мм, знаменатель – база измерения 20 мм. |
Проведение искусственного старения после сварки (1700С, 14 час) приводит к повышению прочности сварного соединения до уровня 284-304 МПа. При этом прочность металла шва при использовании проволок Св.АК5 и Св.1217 практически одинакова и составляет 282-284 МПа. Разрушение образцов с усилением и проплавом при испытаниях происходит по зоне сплавления, а при испытаниях образцов с удаленным усилением и проплавом — по металлу сварного шва.
Следует обратить внимание на тот факт, что искусственное старение приводит к значительным снижениям показателей угла загиба (до 13° для проволоки Св.Ак5). Это связано с выпадением избыточных упрочняющих фаз, содержащих медь, по границам зерен в металле шва.
Металлографические исследования показали, что при испытаниях образцов, которые не подвергались старению после сварки, разрушение происходило по зоне основного металла. Указанная зона соединения при сварке подвергается нагреву в диапазоне температур 300-3300С. Нагрев сплава В1341 в состаренном состоянии до 300-3300С приводит к значительному снижению относительного удлинения при практически неизменной прочности.
Полученные результаты показывают, что для сварных соединений сплава В1341 предпочтительно применение присадочной проволоки Св.1217 и Св.АМг63 в сочетании с искусственным старением сварных соединений после сварки. В этом случае коэффициент прочности сварного соединения составляет 0,78-0,80 от прочности основного материала в искусственно состаренном состоянии. Операция искусственного старения сплава В1341 отличается высокой продолжительностью. Это существенно влияет на производительность технологических процессов, особенно в отраслях с большим объемом выпускаемых изделий. Поэтому в данной работе исследовалось влияние температуры и времени искусственного старения на механические свойства основного металла и сварных соединений сплава В1341.
Известно, что сушка лакокрасочных покрытий при производстве различных деталей из алюминиевых сплавов обычно осуществляется при температурах 170-200°С с выдержкой от 20 до 60 мин. Исследования показали, что при 170°С и выдержке 30 мин сплав имеет такие же свойства, как после естественного старения. Чтобы обеспечить требуемый уровень свойств, время выдержки при сушке лакокрасочных покрытий при 170°С должно быть не менее 3 ч. Такая длительная выдержка при сушке лакокрасочного покрытия технологически неоправданна и не всегда может быть принята. В связи с этим было исследовано влияние старения при более высоких температурах с выдержкой 20-60 мин на свойства сплав В1341. Старение листов сплава В1341 при 190-200°С в течение 30 мин приводит к существенному повышению механических свойств; σв = 303-326 МПа, σ0,2 = 185-236 МПа, δ = 14,9-19,3% . Эти режимы могут совмещать операции сушки лакокрасочного покрытия и искусственного старения деталей из сплава В1341.
Таким образом, полученные результаты показали перспективность применения сплава В1341 в сварных конструкциях из алюминиевых сплавов вместо сплавов АМг2 и АМг6.
Литература
1. Патент РФ №2255133 МКП С 22 С 21/04. Деформируемый сплав на основе алюминия и изделие, выполненное из этого сплава (Фридляндер И.Н., Грушко О.Е., Шевелева Л.М., Шамрай В.Ф., Овчинников В.В.). Приоритет изобретения 19 декабря 2003.
ArticleName | Повышение свариваемости термоупрочненных алюминиевых сплавов | ArticleAuthorData | Московский государственный технический университет им. Н. Э. Баумана, Москва, Россия: Б. Ф. Якушин, профессор кафедры «Технологии сварки и диагностики»
А. В. Бакуло, главный сварщик, эл. почта: [email protected] | Abstract | Термоупрочненные алюминиевые сплавы являются новым и весьма перспективным материалом для сварных конструкций. Они отличаются от сплавов, упрочненных наклепом (Al – Mg), наличием двухфазного строения (твердый раствор + интерметаллиды), что двукратно повышает как прочность, так и другие эксплуатационные свойства (твердость, жесткость, жаропрочность) и тем самым позволяет снизить массу металлоконструкций и одновременно сократить расход алюминия как основы сплавов. Особенно значимо снижение массы изделий в аэрокосмической и транспортной технике, являющихся основными потребителями легких сплавов. Несмотря на очевидную целесообразность термоупрочнения и наличие стандартных марок высокопрочных сплавов (В96, В92, 1201,1420 и др.) все основные конструкции изготавливают из нетермоупрочняемого АМг6. Это связано с резким снижением свариваемости термоупрочненных сплавов, т. е. меньшей пригодностью для сварки, являющейся в настоящее время ведущим технологическим процессом изготовления металлоконструкций. При сварке этих сплавов стандартными методами снижается коэффициент прочности K = σсс /σом вследствие перегрева и разупрочнения в зоне термического влияния сварки, деградации упрочняющих фаз, а также охрупчивания и снижения коррозионной стойкости сварных соединений в результате технологического наследования дефектов в многостадийных технологических процессах. Однако следует учитывать и несомненный прогресс в области технологии и металлургии сварочных процессов, который расширяет ряд свариваемых сплавов за счет несвариваемых в результате разработки и расширяющегося применения высокоскоростной импульсно-дуговой сварки плавящимся электродом в защитных газах, лазерной и электронно-лучевой сварки, принципиально нового способа сварки трением с перемешиванием, а также новых сплавов и сварочных материалов, микролегированных редкоземельными элементами и модифицированных наноструктурными добавками скандия и циркония. | keywords | Термоупрочненные сплавы, свариваемость, жаропрочность, лазерная сварка, импульсно-дуговая сварка, модифицирование шва, недендритная кристаллизация, равноосная литая структура металла шва | References | 1. ГОСТ 26389–84. Соединения сварные. Методы испытаний на сопротивляемость образованию горячих трещин при сварке плавлением. — Введ. 1986–01–01. 11. Зайцев В. И., Дружинин А. Т., Якушин Б. Ф. О преимуществах импульсно-дуговой MIG-сварки высокопрочных алюминиевых сплавов // Сварка и диагностика. 2010. № 2. С. 4–39. |
Свариваемость материалов — алюминиевые сплавы
Знание профессии 21
Алюминий и его сплавы используются в производстве из-за их небольшого веса, хорошей коррозионной стойкости и свариваемости. Хотя обычно они имеют низкую прочность, некоторые из более сложных сплавов могут иметь механические свойства, эквивалентные сталям. Идентифицированы различные типы алюминиевых сплавов и даны рекомендации по изготовлению компонентов без ухудшения коррозионных и механических свойств материала или появления дефектов в сварном шве.
Щелкните здесь, чтобы увидеть наши последние подкасты по технической инженерии на YouTube .Типы материалов
Поскольку чистый алюминий относительно мягкий, в него добавляются небольшие количества легирующих элементов для получения ряда механических свойств. Сплавы сгруппированы в соответствии с основными легирующими элементами, определенные коммерческие сплавы имеют четырехзначное обозначение в соответствии с международными спецификациями для деформируемых сплавов или буквенно-цифровой системой ISO.
Сплавы можно дополнительно классифицировать в соответствии со способами, с помощью которых легирующие элементы развивают механические свойства, нетермообрабатываемые или термообрабатываемые сплавы.
Сплавы без термической обработки
Прочность материала зависит от эффекта наклепа и упрочнения твердого раствора таких легирующих элементов, как магний и марганец; легирующие элементы в основном встречаются в сплавах серий 1ххх, 3ххх и 5ххх. При сварке эти сплавы могут потерять эффект наклепа, что приводит к размягчению ЗТВ, прилегающей к сварному шву.
Термообрабатываемые сплавы
Твердость и прочность материала зависят от состава сплава и термообработки (термообработка на твердый раствор и закалка с последующим естественным или искусственным старением приводит к тонкой дисперсии легирующих компонентов). Основные легирующие элементы определены в сериях 2ххх, 6ххх и 7ххх. Сварка плавлением перераспределяет упрочняющие компоненты в ЗТВ, что локально снижает прочность материала.
Процессы
Большинство марок ковки марок 1xxx, 3xxx, 5xxx, 6xxx и средней прочности 7xxx (e.грамм. 7020) можно сваривать плавлением с использованием процессов TIG, MIG и кислородно-топливной сварки. В частности, сплавы серии 5ххх обладают отличной свариваемостью. Высокопрочные сплавы (например, 7010 и 7050) и большая часть сплавов серии 2xxx не рекомендуются для сварки плавлением, поскольку они склонны к ликвации и растрескиванию при затвердевании.
Метод сварки трением с перемешиванием особенно подходит для алюминиевых сплавов. Он способен производить качественные сварные швы для многих сплавов, включая те термически обрабатываемые сплавы, которые склонны к горячему растрескиванию во время сварки плавлением.
Присадочные сплавы
Состав присадочного металла определяется по:
- Свариваемость основного металла
- Минимальные механические свойства наплавленного металла
- коррозионная стойкость
- требования к анодному покрытию
Номинально соответствующие присадочные металлы часто используются для нетермообрабатываемых сплавов. Однако для материалов с низким содержанием сплавов и термообрабатываемых сплавов используются несовместимые наполнители для предотвращения растрескивания при затвердевании.
Выбор состава присадочного металла для различных свариваемых сплавов определен в BS EN 1011 Pt 4: 2000 для сварки TIG и MIG; Рекомендуемые составы присадочных металлов для наиболее часто используемых сплавов приведены в таблице Таблица .
Обозначение сплава | Химическое обозначение | Классификация | Наполнитель | Применение |
---|---|---|---|---|
EN AW-1080A | EN AW-Al 99.8 (А) | NHT | R-1080A | Химический завод |
EN AW-3103 | EN AW-Al Mn1 | NHT | R-3103 | Здания, теплообменники |
EN AW-4043A | EN AW-Al Si5 (A) | – | – | Присадочная проволока / пруток |
EN AW-5083 | EN AW-Al Mg4,5Mn0,7 | NHT | R-5556A | Суда, вагоны, мосты |
EN AW-5251 | EN AW-Al Mg2Mn0.3 | NHT | R-5356 | Автомобили дорожные морские |
EN AW-5356 | EN AW-Al Mg5Cr (A) | – | – | Присадочная проволока / пруток |
EN AW-5556A | EN AW-Al Mg5Mn | – | – | Фильтровальная проволока / пруток |
EN AW-6061 | EN AW-Al Mg1SiCu | HT | R-4043A R-5356 | Конструкционный, трубы |
EN AW-7020 | EN AW-Al Zn4.5Mg1 | HT | R-5556A | Строительные, транспортные |
HT = термообрабатываемый, NHT = нетермический |
Дефекты сварных швов
Алюминий и его сплавы легко свариваются при соблюдении соответствующих мер предосторожности. Наиболее вероятные дефекты сварных швов плавлением:
- пористость
- растрескивание
- Плохой профиль сварного шва
Пористость
Пористость часто рассматривается как неотъемлемая черта сварных швов MIG; Типичный вид мелкодисперсной пористости в сварном шве TIG показан на фотографии.Основная причина пористости — поглощение водорода в сварочной ванне, который образует дискретные поры в затвердевающем металле сварного шва. Наиболее распространенными источниками водорода являются углеводороды и влага из загрязняющих веществ на поверхностях основного материала и присадочной проволоки, а также водяной пар из атмосферы защитного газа. Даже следовые количества водорода могут превышать пороговую концентрацию, необходимую для образования пузырьков в сварочной ванне, поскольку алюминий является одним из металлов, наиболее подверженных пористости.
Для минимизации риска необходимо проводить тщательную очистку поверхности материала и присадочной проволоки.Подходят три метода очистки; механическая очистка, обезжиривание растворителем и очистка химическим травлением.
При сварке в среде защитного газа следует избегать вовлечения воздуха, убедившись, что имеется эффективный газовый экран и дуга защищена от сквозняков. Также следует принять меры, чтобы избежать улавливания водяного пара из газовых линий и сварочного оборудования; Рекомендуется продуть сварочную систему примерно за час перед использованием.
Механическая очистка
Для удаления оксидов и загрязнений с поверхности можно использовать проволочную щетку (щетина из нержавеющей стали), соскабливание или опиливание.Перед механической очисткой необходимо провести обезжиривание.
Растворители
Для удаления жира, масла, грязи и незакрепленных частиц можно использовать погружение, опрыскивание или протирание органическими растворителями.
Химическое травление
Для очистки партии можно использовать 5% раствор гидроксида натрия, но после этого следует промыть его в HNO 3 и воде для удаления продуктов реакции с поверхности.
Трещины затвердевания
Растрескивание возникает в алюминиевых сплавах из-за высоких напряжений, возникающих в сварном шве из-за высокого теплового расширения (вдвое больше, чем у стали), и значительного сжатия при затвердевании — обычно на 5% больше, чем в эквивалентных стальных сварных швах.
Трещины затвердевания образуются в центре сварного шва, обычно во время затвердевания распространяются вдоль осевой линии. Трещины затвердевания также возникают в кратере сварного шва в конце операции сварки. Основные причины трещин затвердевания следующие:
- Неправильная комбинация присадочная проволока / основной металл
- неправильная геометрия сварного шва
- Сварка в условиях повышенного давления
Риск растрескивания можно снизить, используя неподходящий, устойчивый к растрескиванию наполнитель (обычно из сплавов серий 4ххх и 5ххх).Недостатком является то, что полученный металл сварного шва может иметь более низкую прочность, чем основной металл, и не поддаваться последующей термообработке. Наплавленный валик должен быть достаточно толстым, чтобы выдерживать напряжения сжатия. Кроме того, степень ограничения сварного шва может быть минимизирована за счет правильной подготовки кромок, точной настройки соединения и правильной последовательности сварки.
Щелочное растрескивание
Ликвационное растрескивание происходит в ЗТВ, когда на границах зерен образуются пленки с низкой температурой плавления.Они не могут противостоять сжимающим напряжениям, возникающим при затвердевании и остывании металла шва. Термообрабатываемые сплавы, особенно сплавы серий 6ххх и 7ххх, более подвержены этому типу растрескивания.
Риск можно снизить, используя присадочный металл с более низкой температурой плавления, чем основной металл, например, сплавы серии 6ххх свариваются с присадочным металлом 4ххх. Однако присадочный металл 4xxx не следует использовать для сварки сплавов с высоким содержанием магния (например, 5083), поскольку на границе плавления может образовываться избыточный силицид магния, снижающий пластичность и повышающий чувствительность к трещинам.
Плохой профиль сварного шва
Неправильная настройка параметров сварки или плохая техника сварки могут привести к дефектам профиля сварного шва, таким как отсутствие проплавления, проплавление и поднутрение. Высокая теплопроводность алюминия и быстро затвердевающая сварочная ванна делают эти сплавы особенно чувствительными к дефектам профиля.
Эта статья Job Knowledge была первоначально опубликована в Connect в октябре 1996 года. Она была обновлена, поэтому веб-страница больше не отражает в точности печатную версию.
Какой алюминий лучше всего подходит для сварочных работ?
Алюминий, как и сталь, можно производить с множеством различных физических и химических свойств. Некоторые марки хорошо реагируют на сварку. Другие требуют большего опыта или вообще не должны свариваться. Итак, как выбрать лучший алюминий для сварки ?
Лучший алюминий для сварки: что нужно знать
Прежде всего, знайте, что с алюминием , как правило, труднее работать, чем с углеродистой сталью или нержавеющей сталью .Он ведет себя по-другому — обычно суетливее.
Вот проблемы, которые обычно возникают при сварке алюминия:
- Если после сварки деталь необходимо придать квадратной форме, она может треснуть (из-за тепловой деформации).
- Он менее податлив, чем сталь.
- Легко поддается воздействию тепла.
- Для сварки требуется больше навыков.
Поскольку алюминий относительно дорогой, вы потратите много денег, указав марку с низкой свариваемостью.
Несмотря на это, многие инженеры по-прежнему предпочитают алюминий. Он легкий, что делает его идеальным для многих приложений. Поскольку это цветной металл, алюминий также менее коррозионный и не ржавеет (хотя он все равно коррозирует по-своему, только медленнее).
Когда вы все же выбираете марку алюминия, используйте широко производимую марку алюминия для максимальной рентабельности. Если на рынке много предложения, вы получите гораздо лучшую цену.
Лучшие марки алюминия для сварки
Когда вы покупаете «алюминий», вы на самом деле покупаете алюминиевый сплав — там есть и другие металлы. Эти другие металлы придают алюминию свойства, которые варьируются в зависимости от сорта .
Сорта разделены на серии, начиная с 1XXX и заканчивая 7XXX. Как правило, более высокие числа означают более высокий процент магния.
ПРИЛОЖЕНИЕ | РЕКОМЕНДУЕМЫЕ МАРКИ АЛЮМИНИЯ | ||||
Самолет (конструкционный, трубчатый) | 2014 | 2024 | 5052 | 6061 | 7075 |
Архитектура | 3003 | 6061 | 6063 | ||
Автозапчасти | 2014 | 2024 | |||
Рамы и прицепы для автомобилей | 2024 | 5052 | 6061 | 6063 | |
Лодки | 5052 | 6061 | |||
Строительные изделия | 6061 | 6063 | |||
Химическое оборудование | 1100 | 6061 | |||
Строительство | 2024 | 6061 | 7075 | ||
Кухонная утварь | 3003 | 5052 | |||
Тянутые и формованные детали | 1100 | 3003 | |||
Электрооборудование | 6061 | 6063 | |||
Крепеж и фурнитура | 2024 | 6061 | |||
Производство общего назначения | 1100 | 3003 | 5052 | 6061 | |
Обработанные детали | 2011 | 2014 | |||
Морской | 5052 | 6061 | 6063 | ||
Трубопровод | 6061 | 6063 | |||
Сосуды под давлением | 3003 | 5052 | |||
Рекреационное оборудование | 6061 | 6063 | |||
Винтовое оборудование | 2011 | 2024 | |||
Обработка листового металла | 1100 | 3003 | 5050 | 5052 | 6061 |
Резервуары | 3003 | 6061 | 6063 |
Серии, которые лучше всего подходят для сварки, — это 5XXX и 6XXX .»Можно ли сваривать алюминий 6061?» — один из самых частых вопросов, которые мы получаем. Чаще всего мы используем алюминий 5050 или 6061 , поэтому ответ — «Однозначно». Эти два металла очень распространены, поэтому доступность и цена не должны быть проблемой.
Почему именно эти сплавы? Они самые снисходительные. В них меньше магния, они не такие толстые и с меньшей вероятностью трескаются.
- Алюминий 5XXX полезен, если вам нужно сваривать высокопрочный материал для конструкционных и тяжелых условий эксплуатации (т.е.е. судостроение). Однако из-за большого количества магния их НЕ следует сваривать с присадочным металлом 4XXX.
- 6XXX Серия включает сплавы с магнием и кремнием. Эта серия наиболее широко используется для сварки конструкций и достаточно прочна для зданий и других конструкций. 6XXX также хорошо поддается термообработке.
Хорошие, но не оптимальные оценки
В зависимости от вашего проекта могут подойти и другие сплавы:
- Сплавы серии 1XXX на 99% состоят из алюминия — настолько чистый, насколько это возможно.Он не очень прочный, но очень устойчивый к коррозии. Перевод: не используйте его, чтобы поддерживать здание, но используйте его, чтобы противостоять химическим веществам.
- 3XXX серия Алюминий содержит марганец. Они податливы и легко поддаются сварке, и их часто используют в устройствах, связанных с нагревом (посуда; теплообменники в транспортных средствах и электростанциях). Их посредственная прочность не позволяет использовать их в конструкции.
- 4XXX Сплавы хорошо свариваются, но их чаще используют в качестве присадочных материалов для других марок.
Даже не думай об этих оценках
- 7XXX series Алюминий марки должен обрабатываться опытными сварщиками из-за их плохой реакции на сварку (за некоторыми исключениями). Фактически, вы можете полностью отказаться от сварки алюминия серии 7000. Горячее растрескивание и коррозия под напряжением являются распространенными проблемами. В частности, сплавы 7075 являются отличными сплавами для морского применения благодаря их низкой плотности и стальной прочности. Но они также темпераментны и дороги, так что для сварки они не подходят.Другими словами, , отличный сплав для вашего применения, не может быть равным высокосвариваемому сплаву .
- 2XXX Алюминий также плохо реагирует на сварку, поэтому старайтесь не указывать их. Хотя сплав 2024 года очень распространен и чрезвычайно прочен, он чрезвычайно чувствителен к образованию трещин.
Обратитесь к продавцу
Алюминиевые сплавы серий5ХХХ и 6ХХХ лучше всего подходят для сварки в целом. Помните, что ваш проект и приложение в конечном итоге определят, какая оценка будет работать лучше всего.
При таком большом количестве видов алюминия на выбор лучше всего, если на этапе проектирования вы будете сотрудничать с поставщиком, который знает все их плюсы и минусы. И не забудьте выбрать подходящий присадочный металл — возможно, вы сможете сэкономить!
( Примечание редактора: Эта статья была первоначально опубликована в сентябре 2017 года и недавно была обновлена.)
Сварка алюминия | Технология изготовления пресс-форм
Алюминий, который раньше рассматривался строго как прототип инструментального материала, становится все более популярным вариантом для изготовления пресс-форм.При рассмотрении этого варианта важно сначала взглянуть на различия между сталью и алюминием, а затем определить, как лучше всего использовать преимущества повышенной теплопроводности алюминия без ухудшения качества деталей. Также важно учитывать вопросы, связанные с ремонтом плесени. Изготовить качественную деталь из алюминиевой формы относительно легко, но ремонт этих форм может вызвать проблемы. Чтобы гарантировать успешный ремонт алюминиевой формы, необходимо понимание различий между сталью и алюминием и вариантами алюминиевых сплавов, а также знания о сварочной проволоке и правильных методах сварки.
Алюминий и сталь
Доступные сегодня высокопрочные алюминиевые сплавы являются реальной альтернативой стали для изготовления инструментов. Первоначально используемый в основном для изготовления прототипов из-за своей более низкой стоимости, алюминий предлагает несколько других преимуществ, которые делают его жизнеспособным вариантом для изготовления пресс-форм.
Прежде всего, алюминиевые формы могут стоить примерно половину стоимости стальных форм, и их можно поставить примерно в два раза быстрее, благодаря различным основным характеристикам материалов.Например, несмотря на то, что сталь значительно прочнее алюминия, алюминий весит только одну треть меньше, и некоторые алюминиевые материалы можно обрабатывать для получения прочности, сопоставимой со сталью. Поскольку алюминий мягче стали, его легче резать. Сочетание высокой прочности и малого веса делает алюминий привлекательным для использования в различных отраслях промышленности, включая аэрокосмическую, автомобильную и промышленную.
Еще одним преимуществом алюминия перед сталью является его высокая устойчивость к коррозии.Когда алюминий подвергается воздействию воздуха, образуется тонкий слой оксида алюминия, обеспечивающий повышенную защиту от коррозии. Кроме того, алюминий не становится хрупким при понижении температуры, как сталь. Фактически он увеличивает прочность на разрыв и сохраняет прочность.
Алюминий, как известно, проводит тепло и электричество примерно в шесть раз лучше, чем сталь, а его более высокая теплопроводность играет решающую роль при сварке и ремонте пресс-форм, в результате чего сварные швы затвердевают быстрее.Это также способствует более «практичному» сварному шву, лучшему удержанию металла на месте и упрощению ремонта на месте. Высокая теплопроводность означает, что тепловая энергия, приложенная к одному участку металла, быстро передается другим участкам. Это позволяет материалу сохранять стабильность, выдерживая более высокие температуры. Однако, чтобы избежать ухудшения качества деталей, алюминий требует сварки с более интенсивным нагревом и с большей скоростью, поскольку тепло отводится быстро.
Варианты сплавов
Если вы решите использовать алюминий для следующего проекта пресс-формы, важно выбрать соответствующий алюминиевый сплав.Сплавы создаются, когда к основному алюминию добавляются такие элементы, как медь, магний и цинк. Каждый добавленный элемент придает индивидуальные полезные свойства, улучшающие алюминий.
Есть две основные классификации алюминиевых сплавов: деформируемые и литые. Деформируемые сплавы сначала отливают в виде заготовок, а затем подвергают механической обработке горячими или холодными методами, такими как прокатка, ковка, экструзия и формование, для достижения желаемых форм. Прокатка используется для производства алюминиевых листов, фольги или пластин; ковка используется для производства сложных форм с превосходными свойствами, а экструзия используется для производства труб или стержней.Литые сплавы непосредственно отливаются в желаемую форму, что делает их хорошо подходящими для применений, связанных со сложными формами.
Деформируемые и литые сплавы далее подразделяются на термически обрабатываемые и нетермообрабатываемые. Термообрабатываемые сплавы содержат легирующие элементы, которые увеличивают прочность и растворимость материала за счет термической обработки, но зона термического влияния (ЗТВ) обычно не будет полностью отожжена, что может повлиять на прочность любого сварного шва. Сплавы без термической обработки упрочняются методами холодной обработки.
Эти классификации являются важными факторами, влияющими на свариваемость и ремонт пресс-формы из алюминиевого сплава. Некоторые материалы лучше подходят для определенных сварочных процессов, поэтому необходимо учитывать и метод сварки, поскольку производитель пресс-форм выбирает оптимальный материал.
Некоторые из наиболее часто используемых в производстве алюминиевых сплавов относятся к семейству 7000. Эти сплавы привлекательны для формовщиков, поскольку они обычно обладают высокой прочностью, сравнимой со сталью, и более долговечны, чем другие серии.Цинк является основным легирующим элементом в этих алюминиевых сплавах, и это в сочетании с другими элементами, такими как магний и медь, способствует тому, что они становятся одними из самых прочных сплавов при температуре окружающей среды. Добавление цинка также делает алюминий поддающимся термообработке, что позволяет проводить дисперсионное твердение — метод нагрева, используемый для увеличения предела текучести. Посредством дисперсионного твердения сплавы серии 7000 могут достигать предела прочности на разрыв до 700 МПа (мегапаскалей), что является самым высоким показателем среди всех алюминиевых сплавов.Термическая обработка наиболее эффективна после того, как легирующие элементы были диспергированы посредством прокатки и ковки. Комбинация всех трех процессов создаст свойства, необходимые для высокопрочного алюминия. Хотя сплавы серии 7000 обладают хорошей усталостной прочностью и обрабатываемостью, они менее устойчивы к коррозии, чем другие алюминиевые сплавы, что делает их подверженными коррозионному растрескиванию под напряжением и, в свою очередь, трудными для сварки.
Другим популярным выбором для изготовления пресс-форм являются сплавы серий 2000, 5000 и 6000.Сплавы серии 2000, как и серия 7000, могут быть подвергнуты дисперсионному упрочнению до прочности, аналогичной стали, за счет добавления меди, но сплавы серии 2000 обладают более низкой коррозионной стойкостью, что делает их еще более уязвимыми к коррозионному растрескиванию под напряжением, чем те, что в серии 7000. Многие сплавы серии 2000 считаются несвариваемыми из-за этой уязвимости.
Сплавысерии 5000 имеют добавку магния, которая обеспечивает упрочнение твердого раствора и улучшенное деформационное упрочнение, что придает им наивысшую прочность без термической обработки среди алюминиевых сплавов.Однако из-за этих качеств сплавы серии 5000 являются одними из самых сложных и дорогих для экструзии. В основном они изготавливаются в виде листов и пластин и лишь изредка используются в качестве опции для формования.
Алюминий серии 6000 легирован магнием и кремнием, образуя поддающиеся термообработке, прочные и легко экструдируемые сплавы с хорошей коррозионной стойкостью. В то время как сплавы серии 6000 являются одними из наиболее часто используемых для универсального применения, они не могут достичь высокой прочности сплавов серий 2000 и 7000.
Эти другие семейства сплавов обычно производятся на тех же заводах, которые производят заготовки для семейств сплавов серии 7000, однако они не подвергаются прокатке, ковке и термообработке для повышения прочности. Вместо этого эти сплавы непосредственно отливают в их окончательную форму, что позволяет им определять свои свойства, в том числе прочность и свариваемость, на основе состава сплава, а не в процессе производства. Поскольку литые сплавы не нужно сначала подвергать прокатке или ковке в пластины или листы, их можно более экономично использовать для изделий сложной формы.Однако они не будут обладать таким же уровнем прочности, как их свернутые или кованые аналоги. Литые сплавы — популярный выбор для изготовления прототипов, потому что они стоят примерно вдвое дешевле сплава серии 7000, а для прототипа приемлем более слабый сплав. Модифицированный сплав серии 2000 также доступен в катаной или кованой форме, предлагая хороший баланс между прочностью и сварочными характеристиками. Обе формы сплавов легко свариваются в соответствии с их индивидуальными свойствами.
Желательные качества, присущие каждой серии сплавов, будут определять производственные области, для которых они лучше всего подходят.Из-за своей высокой прочности сплавы серии 7000 чаще всего используются для высокопроизводительных применений, таких как аэрокосмическая промышленность, бронетехника и спортивное оборудование. Сравнительно прочные сплавы серии 2000 чаще всего используются в самолетах или аэрокосмической отрасли, в то время как сплавы серии 5000 более свариваются и обладают прочностью, не поддающейся термической обработке, что делает их полезными для различных структурных применений, таких как мосты, здания, грузовики. или составы поездов, судостроение и сосуды под давлением. Сплавы серии 6000 являются самыми легкими и наиболее экономичными для экструзии, что делает их пригодными для сварки, а также для изготовления широкого спектра экструдированных форм.
Варианты сварочной проволоки
Для успешной сварки для разных алюминиевых сплавов требуются разные сварочные проволоки. Характеристики проволоки должны соответствовать характеристикам конкретного сплава, к которому она будет свариваться, а также следует учитывать способность проволоки к сопоставлению цветов, прочность и влияние на ЗТВ. Кроме того, сварочная проволока должна иметь температуру плавления, аналогичную температуре плавления ее основного материала, чтобы сварка была наиболее эффективной.Например, алюминиевые сплавы с более высокой концентрацией магния следует сваривать с присадочным сплавом, который также содержит более высокие уровни магния. Каждая категория сварочной проволоки имеет свой собственный динамический химический состав, который дает более эффективные результаты с алюминиевым сплавом со схожими характеристиками. Помимо повышения эффективности производства, сварочная деформация должна уменьшиться.
Ремонт производственных форм, изготовленных из нескольких сплавов серии 7000, является сложной задачей, поскольку их склонность к горячему растрескиванию или коррозионному растрескиванию под напряжением делает эти сплавы несвариваемыми с использованием методов дуговой сварки.Исключением из этого правила являются экструзионные сплавы 7003 и 7005 и пластинчатый сплав 7039. Сварка подходящих сплавов серии 7000 может быть выполнена с использованием сварочной проволоки из сплава 5356 или 2319, причем обе из них могут создавать беспористые сварные швы приемлемой прочности, которые могут соответствовать целостности алюминиевого сплава. Из этих сварочных проволок чаще всего используется проволока 5356, поскольку она жесткая, обеспечивает приемлемую прочность и непрерывную подачу, а проволока 2319 поддается термообработке и обеспечивает высокую прочность и хорошую пластичность. Проволока 5356 также имеет наполнитель с содержанием магния 5%, который снижает чувствительность к растрескиванию сварных швов.Чем выше количество магния, тем меньше риск растрескивания.
Два завода по производству алюминиевых сплавов серии 7000 помогли разработать запатентованную сварочную проволоку для сплавов, которая предназначена для работы со сплавами серии 7000. Эти продукты еще не широко доступны, но все первые результаты тестирования показывают улучшенное соответствие цветов по сравнению с проводами 2319 и 5356. Однако ЗТВ вокруг зоны ремонта сварного шва, которая является общей для всех термообработанных сплавов во время ремонта, остается проблемой для этих новых проволок.
Проволока 2319 лучше всего подходит для сварки форм из сплавов серии 2000. Деформируемые сплавы серии 2000 могут подвергаться термообработке для достижения их высокой прочности на разрыв, которая может достигать примерно 448 МПа. Они легированы медью, что позволяет улучшить сварочные характеристики. Испытания показали, что проволока 2319 обеспечивает превосходное качество сварки и соответствие цветов, что делает ее наиболее популярным вариантом, когда подбор цвета имеет большое значение. Сплавы серии 2000 из-за их высокого старения и отпуска также более устойчивы к термической усталости, чем их аналоги серии 7000, а это означает, что тепло от сварного шва не приведет к потере прочности свариваемого материала.
Сплавы серии 6000 — это деформируемые термически обрабатываемые сплавы, которые имеют ЗТВ вокруг сварных участков. Подходящей проволокой для сварки алюминиевых сплавов серии 6000 является проволока 4043, которая является одной из наиболее удобных в обращении, имеет более низкую температуру плавления и лучшую текучесть, что делает ее менее чувствительной к растрескиванию сварных швов. Этот тип проволоки подходит для применений, в которых прочность зоны сварки и соответствие цвета наиболее важны. Однако, если основной материал будет анодирован после ремонта, сварочная проволока 5356 является лучшим вариантом и будет обеспечивать гораздо более точное соответствие цвета, потому что 4043 станет темно-серым после анодирования.
Поскольку литые сплавы имеют более прочную структуру зерна, а деформируемые сплавы более пористые, они с большей вероятностью будут демонстрировать более прочный ремонт при сварке. Хорошим выбором для алюминиевых сплавов серии 5000 является сварочная проволока 5356, в то время как проволока 2319 подходит для сплавов серии 2000. Эти проволоки лучше всего сочетаются по цвету со сплавами, потому что они имеют более низкое содержание кремния, сохраняя анодированный серебристый цвет, который хорошо сочетается, а не черный цвет, который является очевидным и непривлекательным. В качестве изделий без термической обработки литые сплавы не имеют ЗТВ вокруг сварного шва, поэтому область сварки не видна на готовой поверхности формы.
Методы ремонта
После выбора правильной проволоки необходимо переключиться на правильную технику сварки сплава для литейной формы. Это самый большой вклад в успешный ремонт сварного шва. Правильная техника требует большего, чем просто сварка; он также должен учитывать условия окружающей среды и предварительный нагрев материала, который удалит конденсат и повысит его свариваемость.
Обычно для сварки алюминия используется переменный ток (AC), однако постоянный ток (DC) может дать лучшие результаты при ремонте литейных сплавов.Переменный и постоянный ток относятся к полярности электрического тока, протекающего через электрод. Выбор электрода с соответствующей полярностью существенно повлияет на прочность и качество сварного шва.
Как упоминалось ранее, когда алюминий подвергается воздействию воздуха, образуется тонкий слой оксида алюминия. Если этот оксидный слой не удалить, это отрицательно повлияет на правильное плавление и текучесть сварного шва. Для удаления этого слоя требуется гораздо более высокая температура, чем температура, необходимая для плавления основного алюминия.Переменный ток течет в одном направлении половину времени, а в другом — вторую половину. Поскольку переменный ток меняет полярность так часто (120 раз в секунду при токе 60 Гц), сначала удаляется оксидный слой, что позволяет основному металлу затем плавиться и плавиться быстрее. Для достижения наилучших результатов необходим равный и сбалансированный ток в обоих направлениях.
Постоянный ток течет только в одном направлении, обеспечивая постоянную полярность. Импульсная сварка постоянным током, при которой дуга колеблется между высоким пиковым и низким фоновым током, сужает ЗТВ и тепло, прикладываемое к основному материалу, сохраняя исходные свойства металла.Использование импульсной сварки на переменном токе делает зону сварки более пористой, а также приводит к плохому цветовому соответствию. Пористость возникает, когда газы захватываются завихрением при сварке при слишком низком сварочном токе. На алюминии сварку следует выполнять быстро, чтобы предотвратить проникновение тепла в основной блок. Если его выполнять слишком медленно, возрастает риск чрезмерного прожога.
По мере увеличения использования алюминиевой оснастки стоимость отдельных деталей будет снижаться, что, в свою очередь, сделает использование алюминиевой оснастки еще более распространенной.Выбор оптимальной сварочной проволоки и методов облегчит потенциально сложные процессы и обеспечит превосходные результаты сварки.
Точная сварка
Clinton Алюминий и нержавеющая сталь
7 вещей, которые следует учитывать при выборе алюминия марки
Категория: Алюминий, Советы и подсказкиОпубликовано:
Алюминий бывает разных форм и марок.Тип сплава алюминия, который вы выберете, в конечном итоге зависит от того, как вы собираетесь его использовать. Ваше предполагаемое использование позволяет ранжировать характеристики каждой степени от наиболее важных до наименее важных. Это поможет вам сузить список подходящих сортов. Например, если свариваемость наиболее важна для вашего проекта, а прочность — нет, возможно, имеет смысл выбрать сплав 1100, поскольку этот сорт алюминия имеет отличную свариваемость, но обычно не используется для высокопрочных приложений или приложений с высоким давлением.
Воспользуйтесь краткой справочной таблицей в конце этой статьи, чтобы быстро и легко найти марку алюминия, которая подходит именно вам.
При выборе марки алюминия учитывайте следующие факторы:
- Формуемость или обрабатываемость
- Свариваемость
- Обработка
- Коррозионная стойкость
- Термическая обработка
- Прочность
- Типовые приложения для конечного использования
Является ли формуемость или технологичность (детализация путем механической деформации) важным фактором?
Является ли свариваемость алюминия важным фактором?
Является ли обработка алюминия важным фактором?
- Сплав 1100 — Хорошая обрабатываемость (лучше всего при закалке)
- Сплав 2011 — отличная обрабатываемость
- Сплав 2024 — удовлетворительная обрабатываемость (лучшее состояние в отожженном состоянии)
- Сплав 3003 — Хорошая обрабатываемость
- Сплав 5052 — Хорошая обрабатываемость (лучше при твердом закалке)
- Сплав 6061 — хорошая обрабатываемость (только температуры T4 и T6)
- Сплав 6063 — удовлетворительная обрабатываемость
- Сплав 7075 — удовлетворительная обрабатываемость (лучшее состояние в отожженном состоянии)
Является ли коррозионная стойкость алюминия важным фактором?
Является ли термообработка алюминия важным фактором?
Является ли прочность алюминия важным фактором?
Типичные области конечного использования алюминия марок:
Краткая справочная таблица — выбор марки алюминия
Формуемость или технологичность | Свариваемость | Обработка | Коррозионная стойкость | Термическая обработка | Прочность | Типичные области применения | |
Сплав 1100 | Отлично | Отлично | Хорошо | Отлично | Нет | Низкая | Прядение металла |
Сплав 2011 | Хорошо | Плохо | Отлично | Плохо | Есть | Высокая | Общая обработка |
Сплав 2024 | Хорошо | Плохо | Ярмарка | Плохо | Есть | Высокая | Аэрокосмическое приложение |
Сплав 3003 | Отлично | Отлично | Хорошо | Хорошо | Нет | Средний | Химическое оборудование |
Сплав 5052 | Хорошо | Хорошо | Ярмарка | Отлично | Нет | Средний | Морское применение |
Сплав 6061 | Хорошо | Хорошо | Хорошо | Отлично | Есть | Средний | Применение в конструкциях |
Сплав 6063 | Хорошо | Хорошо | Ярмарка | Хорошо | Есть | Средний | Архитектурные приложения |
Сплав 7075 | Плохо | Плохо | Ярмарка | Среднее значение | Есть | Высокая | Аэрокосмические приложения |
Заявление об ограничении ответственности: обратите внимание, что эта информация не должна использоваться в целях проектирования, и ни при каких обстоятельствах MSFFC не несет ответственности за любой ущерб, возникший в результате неправильного использования этой информации.
Металлические Супермаркеты
Metal Supermarkets — крупнейший в мире поставщик мелкосерийного металла с более чем 100 магазинами в США, Канаде и Великобритании. Мы эксперты по металлу и обеспечиваем качественное обслуживание клиентов и продукцию с 1985 года.
В Metal Supermarkets мы поставляем широкий ассортимент металлов для различных областей применения. В нашем ассортименте: низкоуглеродистая сталь, нержавеющая сталь, алюминий, инструментальная сталь, легированная сталь, латунь, бронза и медь.
У нас в наличии широкий ассортимент форм, включая стержни, трубы, листы, пластины и многое другое. И мы можем разрезать металл в точном соответствии с вашими требованиями.
Посетите одно из наших 100+ офисов по всей Северной Америке сегодня.
(PDF) Свариваемость алюминиевых сплавов с помощью мощного диодного лазера
161-с
WELDING JOURNAL
ИССЛЕДОВАНИЕ СВАРКИ
Таблица 1, можно установить, что содержание кремния
умеренно способствует увеличению проплавление шва.Таким образом, сплавы 6082 и
2017 имеют более низкое содержание магния
и более высокое содержание кремния, чем 2024. Pro-
Учитывая, что сплавы 6082, 2017 и 2024 имеют одинаковую свариваемость, вычитается, что
меньше Содержание магния компенсируется повышенным содержанием кремния
. Однако, как и влияние содержания цинка
, Si, по-видимому, оказывает гораздо меньшее влияние
, чем магний, на свариваемость алюминиевых сплавов
минимум.
В итоге, порядок свариваемости ob-
для шести алюминиевых сплавов был
следующим образом: 5083> 7075> 2017 = 2024 =
6082> 1050. Магний был
, как считается наиболее влиятельный легирующий элемент на улучшение свариваемости алюминиевых сплавов
минимум. Цинк и кремний
также улучшают свариваемость, хотя
влияние этих последних легирующих элементов кажется ниже, чем магния.
Об этих элементах обычно сообщается, что
уменьшают теплопроводность и температуру плавления
, причем оба эффекта
благоприятны для повышения свариваемости.
Выводы
В данной работе шесть алюминиевых сплавов (1050,
,2017, 2024, 5083, 6082 и 7075) были сварены в режиме проводимости
с использованием мощного лазерного диода. Стыковые соединения с высоким проплавлением
могли быть достигнуты
в каждом сплаве при оптимизации экспериментальных условий
.Фактически, были получены сварные швы шести сплавов
с более высоким проплавлением, чем у тех
, о которых ранее сообщалось в режиме проводимости
.
Глубина и ширина полученных
сварных швов были подогнаны к простому математическому уравнению, предложенному авторами. Выражение
позволило оценить глубину сварного шва
для каждого сплава при различных условиях лазерной сварки
, принимая во внимание ac-
, считая только входные значения мощности лазера
и скорости сварки, обеспечивая приемлемую подгонку
к измеренным экспериментальным значениям проницаемости
.
Наконец, свариваемость шести алюминиевых сплавов
minum была сравнена с учетом глубины, формы и объема плавления
, измеренных на сварных швах между валиком и пластиной,
. Порядок свариваемости
, учитывающий как
проникающую способность сварного шва, так и склонность к образованию трещин при затвердевании, составил
: 5083> 7075> 2017 = 2024 = 6082>
1050. Содержание магния. Наблюдается, что
является наиболее влиятельным легирующим элементом
на свариваемость алюминиевых сплавов.Цинк
и кремний также улучшают свариваемость
, хотя и в меньшей степени, чем магний
. Эти элементы уменьшают теплопроводность
и температуру плавления, тем самым повышая сварочную способность алюминиевых сплавов.
Благодарности
Настоящая работа финансово поддержана
Министерством образования и науки
(проект DELATIAL, ссылка MAT2008-
06882-C04-02 и проект LENTEC, исх.PTQ-
09-01-00629) и Хунта Андалусии (pro-
ject SOLDATIA, Ref. TEP-6180). Авторы
хотели бы поблагодарить студентов Xavier Bouchon и
Maëlys Le Coz из Политехнической школы
l’université de Nantes за их активное сотрудничество в этих проектах.
Ссылки
1. Санчес-Амая, Дж. М., Дельгадо, Т.,
Гонсалес-Ровира, Л., и Ботана, Ф. Дж. 2009.
Лазерная сварка алюминиевых сплавов 5083 и 6082
в режиме проводимости.Прил. Серфинг. Sci.
255 (23): 9512–9521.
2. Санчес-Амая, Дж. М., Дельгадо, Т., Де
Дамборенеа, Дж. Дж., Лопес, В., и Ботана, Ф. Дж.
2009. Лазерная сварка образцов AA 5083 диодным лазером высокой мощности
. Sci. Technol. Сварка. Присоединиться. 14 (1):
78–86.
3. Дин Р. Г., Оджо О. А. и Чатурведи,
М. С. 2007. Микроструктура металла сварного шва лазерным лучом в модифицированном иттрием сплаве на основе Ni3Al
с направленной твердостью.Интерметаллиды 15: 1504–1510.
4. Ахтер, Р., Иванчев, Л., и Бургер, Х. П.
2007. Влияние термообработки до / после Т6 на механические свойства
сваренного лазером литого алюминиевого сплава SSM
A356. Мат. Sci. Англ. A – Struct.
447: 192–196.
5. Куо Т. Ю. и Линь Х. С. 2006. Влияние уровня импульса
Nd-YAG-лазера на свойства при растяжении
и формуемость лазерных сварных деталей в автомобильных алюминиевых сплавах
.Мат. Sci. Англ. A – Struct. 416:
281–289.
6. Ян, Дж., Цзэн, X., Гао, М., Лай, Дж., И Лин,
T. 2009. Влияние сварочной проволоки на микроструктуру
и механические свойства 2А12 из алюминиевого сплава
в гибридной сварке CO2-лазером-MIG. Прил.
Прибой. Sci. 255 (16): 7307–7313.
7. Кампана Г., Аскари А., Фортунато А.,
и Тани Г. 2009. Гибридная лазерная сварка MIG
алюминиевых сплавов: влияние защитных газов
.Прил. Серфинг. Sci. 255 (10): 5588–5590.
8. Tobar, MJ, Lamas, IM, Yáñez, A.,
Sánchez-Amaya, JM, Boukha, Z., and Botana,
FJ 2010. Экспериментальные и имитационные исследования
лазерной кондуктивной сварки AA5083 alu-
не менеесплавов. Физика 5: 299–308.
9. Duley, W. W. 1998. Laser Welding, Chapter
3 и 4. Нью-Йорк, Нью-Йорк: John Wiley & Sons.
10. Окон, П., Дирден, Г., Уоткинс, К., Шарп,
М., and French, P. 2002. Proc. 21-е межд. Конг. on
Applications of Lasers and Electro-Optics (ICA-
LEO 2002). Скоттсдейл, Аризона, октябрь 2002 г.,
Laser Institute of America, стр. 233–241.
11. Чжао, Х., Деброй Т. 2001. Сварка
Изменение состава металла во время проводимости
Режим лазерной сварки алюминиевого сплава 5182. Met-
все. Матер. Пер. В 32В: 163–172.
12. Ши, Й., Чжонга, Ф., Ли, Х., Гонг, С., и
Чен, Л.2007. Влияние лазерной сварки на разрывную вязкость
листа из алюминиевого сплава 1420 толщиной
. Мат. Sci. Англ. A – Struct. 465: 153–159.
13. Бассани П., Капелло Э., Коломбо Д., Pre-
Витали Б. и Ведани М. 2007. Влияние параметров процесса
на свойства валика A359 / SiC
ГМК сваренные лазером. Compos. Часть A-Прил. С.
38: 1089–1098.
14. Spina, R., Tricarico, L., Basile, G., и
Sibillano, T.2007. Термомеханическое моделирование
лазерной сварки листов АА5083. J. Mater.
Процесс. Tech. 191: 215–219.
15. Ancona, A., Sibillano, T., Tricarico, L.,
Spina, R., Lugara, PM, Basile, G., and Schi-
avone, S. 2005. Сравнение двух различных noz-
zles для лазерной сварки сплава алюминия
АА5083. J. Mater. Процесс. Tech. 164–165: 971–977.
16. Сибиллано, Т., Анкона, А., Берардия, В.,
Шингаро, Э., Basilea, G., и Lugara, P. M.
2006. Исследование влияния защитного газа на лазерную сварку
алюминиевых сплавов AA5083
с помощью спектроскопических исследований в процессе. Опт.
Лазеры Eng. 44: 1039–1051.
17. Tricarico, L., Spina, R., Sorgente, D., An-
,cona, A., Sibillano, T., and Basile, G. 2007. Ex-
, периментальный анализ стыковых соединений AA5083. сваренный
СО2лазером. Key Eng. Мат. 344: 745–750.
18.Haboudou, A., Peyre, P., Vannes, A. B.,
и Peix, G. 2003. Снижение пористости
, возникающей при лазерной сварке Nd: YAG алюминиевых сплавов A356
и AA5083. Мат. Sci. Англ. A–
Struct. 363: 40–52.
19. Абэ Н., Цукамото М., Маеда К.,
Намба К. и Моримото Дж. 2006. Сварка алюминиевого сплава
с использованием мощного прямого диодного лазера
. J. Laser Appl. 18 (4): 289–293.
20. Ховард К., Лоусон, С., и Чжоу, Ю.
2006. Сварка алюминиевого листа с использованием диодного лазера высокой мощности
. Сварочный журнал 85 (5):
101–110.
21. Мартуканиц, Р. П., Ян, Р., Армао, Ф. Г.,
Пикеринг, Э. Р., и Балдантони, А. 1994. Лазерная сварка
лучевой сваркой алюминиевых сплавов для автомобилей
. Труды Международного конгресса автомобильных инженеров
и позиция Ex-
, Общество автомобильных инженеров, SAE
, технический документ 940158.
22. Мартуканиц Р. П. и Смит Д. Дж. 1995.
Разработка процесса лазерной сварки
алюминиевых сплавов. Труды 6-й международной конференции по сварке алюминия
ments. Американское сварочное общество, стр. 309–323.
23. Мартуканиц, Р. П., Альтшуллер, Б.,
Армао, Ф. Г., и Пикеринг, Э. Р. 1996. Проп-
свойства и характеристики лазерных сварных швов
автомобильных сплавов.Материалы Международного конгресса
инженеров автомобильной промышленности
и выставка Общества инженеров автомобильной промышленности
neers, Технический документ SAE 960168.
24. Ван Хорн, К. Р. 1978. Алюминий. Met-
als Park, N.Y .: ASM, pp. 167–177.
25. Сакамото, Х., Шибата, К., и
Даусингер, Ф. 2003. Влияние легирующих элементов
на свойства сварных швов при лазерной сварке СО2 алюминиевых сплавов
минимум. Сварочный журнал 82 (7): 509–513.
26. Луиджендийк Т. 2000. Сварка алюминиевых сплавов диссими-
лар. J. Mater. Процесс. Tech. 103:
29–35.
27. Чен Б. К., Томсон П. Ф. и Чой С.
К. 1992. Компьютерное моделирование микроструктуры
во время горячей плоской прокатки алюминия. Матер. Sci.
Тех. 8: 72–77.
28. Ahmed, H., Wells, MA, Maijer, DM,
Howes, BJ, and van der Winden, MR 2005.
Моделирование эволюции микроструктуры во время
горячей прокатки AA5083 с использованием внутреннего состояния
вариативный подход, интегрированный в модель FE.
Мат. Sci. Англ. A – Struct. 390 (1-2): 278–290.
29. Чжао, Х., Уайт, Д. Р., и Деброй, Т.
1999. Текущие проблемы и проблемы лазерной сварки
автомобильных алюминиевых сплавов. Int.
Матер. Ред. 44 (6): 238–266.
30. www.esabna.com/us/en/education/knowl-
edge / qa /. Как и почему в алюминий добавляют легирующие элементы
. Автор: Т. Андерсон, ESAB,
2010.
31. Чжан Ю., Ван X. и Ву Дж.2009.
Международная конференция по электронной упаковке —
ing Technology & High Density Packaging
(ICEPT-HDP), стр. 708–712.
Sanchez-Amaya Май 2012 автор corr_Layout 1 4/13/12 9:32 AM Страница 161
Контроль фазы с помощью наночастиц для дуговой сварки несвариваемого алюминиевого сплава 7075
Результаты дуговой сварки
Присадочный пруток AA7075, обработанный нанотехнологиями, был изготовлен путем включения 1,7 об.% наночастиц TiC 40–60 нм в AA7075 с использованием включения наночастиц с помощью соли и горячей экструзии (см. Методы).Основным преимуществом этого процесса производства перед присадочными стержнями с покрытием из частиц или присадочными трубками с ядром из наночастиц является состояние, в котором наночастицы вводятся в ванну расплава во время сварки. За счет включения диспергированных наночастиц в алюминиевую матрицу до фактического процесса сварки переход арматуры в зону плавления становится более эффективным. В целях сравнения мы провели эксперименты по дуговой сварке с использованием стандартного наполнителя AA5356 (Al-5Mg), чистого наполнителя AA7075 и нашего обработанного нанотехнологиями стержня AA7075 для сплавления двух листов AA7075 размером 152.4 × 76,2 × 3,175 мм каждый, как показано на рис. 1а (см. Методы). Сварные швы, выполненные с использованием этих трех различных присадочных материалов, показаны на рис. 1b – d. Следует отметить, что параметры сварного шва с относительно высоким подводимым теплом и относительно низкой скоростью сварки были выбраны для увеличения термического напряжения, а также усадки при затвердевании и, таким образом, демонстрируют влияние присадочных материалов на склонность к трещинам затвердевания.
Рис. 1Дуговая сварка вольфрамовым электродом в газовой среде (GTAW) AA7075. a Два листа AA7075 152,4 × 76,2 × 3,175 мм были сварены дуговой сваркой с использованием трех различных типов присадочных материалов для сварного шва (фиолетовый). b и c Макроскопические трещины затвердевания в зонах плавления валика в сварных швах, выполненных с использованием обычных присадочных материалов AA7075 и ER5356, соответственно. d При использовании AA7075 + 1,7 об.% TiC в качестве присадочного материала сварной шов получается ровный сварной шов без признаков растрескивания. Шкала 10 мм
На рис. 1b показан сварной шов, выполненный с использованием чистого присадочного материала AA7075.Непрерывная макроскопическая трещина на центральной линии соединения указывает на склонность AA7075 к растрескиванию при затвердевании при сварке плавлением. Сварка, выполненная с использованием ER5356, показана на рис. 1c. Этот тип наполнителя обычно используется для уменьшения возникновения трещин при затвердевании при сварке материалов, менее подверженных растрескиванию, таких как AA6061 и AA7005. Тем не менее, в нашем эксперименте эффект этого присадочного материала был неудовлетворительным и не подавлял растрескивание при затвердевании в AA7075.Соединение показало ту же картину ошибок, что и на рис. 1b. Третий сварной шов, выполненный с наноразмерным присадочным материалом AA7075, показал удивительно иную картину. Шайба, показанная на рис. 1d, не имела макроскопических дефектов и была сварена с теми же параметрами, что и два обычных присадочных материала.
Влияние наночастиц на морфологию зерен в зоне плавления
Чтобы лучше понять эти результаты, мы провели исследования микроструктуры с использованием оптической микроскопии (ОМ) и реагента Века, чтобы выявить морфологию зерен различных зон плавления.На рис. 2а очевидны недостатки сварки AA7075 с аналогичным присадочным материалом.
Рис. 2Оптический микроскоп: характеристика горизонтальных поперечных сечений сварных швов в плоскости свариваемых опорных пластин, как показано на рис. 1. a , c и e Морфология зерна выполненных сварных швов с AA7075, ER5356 и наночастицами AA7075 в качестве наполнителя соответственно. Черные пунктирные линии обозначают линию сплавления зоны плавления (MZ) и зоны частично плавления (PMZ), а белые пунктирные линии указывают на переход криволинейного роста зерна, прилегающего к линии сплавления, и столбчатый, следящий за ростом зерна в центре сварного шва. . b Дендрит произошел от линии слияния. d Столбчатые зерна в центральной части сварного шва. f Шаровидные зерна в MZ нанообработанного сварного шва AA7075. Шкала 200 мкм для a , c , e , 50 мкм для b , d , 10 мкм для f
Из-за широкой полутвердой зоны сплава и нелинейности кривая зависимости твердой фракции от температуры, зона плавления затвердевает в виде больших дендритов, следуя за подводимым теплом.На вставке рис. 2b показаны изогнутые дендритные зерна, прилегающие к линии сплавления, со средним размером 116,5 ± 68,7 мкм, в то время как ближе к центральной линии сильно дендритные зерна достигают длины в сотни микрометров. Во время затвердевания эти дендриты образуют канавки с жидкостью, в которые должна поступать жидкость из МЗ, постепенно переходя из жидкого состояния в твердое. Если эти канавки путем самопроизвольного зарождения на входе или слияния фронтов затвердевания отсекаются от MZ, оставшаяся жидкая фракция образует карман.Объемная усадка захваченной жидкости вызовет перпендикулярное напряжение относительно направления сварки. Если давление внутри этой траншеи падает ниже давления кавитации, образуется пустота, инициирующая трещину, которая следует за MZ. Было обнаружено, что это явление сильно зависит от скорости затвердевания производственного процесса 26 .
На рис. 2с показана зона плавления, приваренная присадочным прутком ER5356. Было обнаружено, что размер зерна, прилегающего к линии плавления, уменьшается в среднем до 70.5 ± 44,5 мкм, в то время как столбчатый рост дендритных зерен, показанный на вставке рис. 2d, остается аналогичным сварному шву, выполненному с присадочным материалом AA7075. Целью сварки с разными присадочными материалами является сильное разбавление чувствительного к трещинам основного материала менее чувствительным к трещинам присадочным материалом. Однако при таком подходе необходимо пойти на несколько компромиссов. При разбавлении зоны плавления разнородными присадочными сплавами концентрация упрочняющих компонентов сплава AA7075 уменьшается. Это приводит к снижению прочности после сварки, а также к снижению чувствительности к термообработке после сварки.Кроме того, использование этих присадочных стержней увеличивает вероятность ликвационного растрескивания. Kou et al. обнаружили, что обычные алюминиевые сплавы-наполнители, такие как ER5356, вызывают затвердевание зоны плавления раньше, чем зона частично плавления, прилегающая к ванне расплава. Точнее, твердая фракция состава ванны расплава становится больше, чем твердая фракция чистого AA7075 в зоне частично расплавленного металла при той же температуре. Это вызывает растяжение ослабленного PMZ по направлению к центру ванны расплава и в конечном итоге приводит к ликвационным трещинам 27 .Этот режим разрушения не наблюдался в этом исследовании из-за снятия напряжения, вызванного растрескиванием при затвердевании.
С нашим нанообработанным присадочным материалом был успешно реализован альтернативный подход, который потенциально может коренным образом изменить механизмы затвердевания материала, что позволяет выполнять сварку плавлением AA7075 без каких-либо из вышеупомянутых недостатков. На рис. 2д показано горизонтальное поперечное сечение шва, сваренного с использованием AA7075, обработанного присадочным прутком с 1,7 об.% TiC.Рисунок 2e показывает однородную морфологию зерна по всей MZ, сильно отличающуюся от ранее представленных традиционных сварных швов. Зерна сильно равноосны, средний размер 9,4 ± 5,0 мкм, границы зерен гладкие. Однако при добавлении наночастиц эпитаксиальное зародышеобразование на границе раздела жидкость-твердое тело остается благоприятным. В процесс затвердевания вводятся несколько полезных механизмов, вызывающих эту особую морфологию зерна. Во-первых, присутствие TiC замедляет фронт затвердевания и, следовательно, снижает скорость роста дендритных зерен, происходящих на границе раздела жидкость-твердое тело.Замедленный рост зерен делает возможным образование области, прилегающей к границе раздела, с повышенным переохлаждением, где присутствие наночастиц добавляет гетерогенное зародышеобразование к процессу затвердевания. Этот эффект усиливается для алюминия и TiC, имеющих фактор рассогласования решеток 5,8%, что указывает на полную эпитаксию зерна алюминия, зарождающегося на поверхности наночастиц 28 . Наконец, наночастицы изменяют внешний вид этих неоднородно зародышевых зерен. Как недавно было показано Guo et al., наночастицы оказывают сильное влияние на рост равноосных дендритных зерен 19 . Авторы заметили, что наночастицы SiC модифицировали структуру α-зерен в сплаве Mg-25Zn-7Al, давая почти глобулярные зерна, похожие на внешний вид зерен, показанный на вставке рис. 2f. Это отсутствие направленного роста дендритных зерен является важным показателем преимуществ, которые наносыпученные присадочные материалы привносят в процесс сварки алюминиевых сплавов, подверженных образованию горячих трещин. Кроме того, использование аналогичного наполнителя исключает возникновение ликвационного крекинга.
Модификация вторичной фазы AA7075
Чтобы лучше понять влияние наночастиц TiC на поведение затвердевания AA7075, были использованы сканирующая электронная микроскопия (SEM) и просвечивающая электронная микроскопия (TEM) для исследования морфологии вторичной фазы зон плавления, сваренных с чистый AA7075 и наноразмерный наполнитель AA7075. На рис. 3а показано типичное распределение вторичной фазы в зоне плавления чистого AA7075. Как видно на изображениях ОМ, появление вторичной фазы в чистом алюминиевом сплаве указывает на дендритное затвердевание зерен α-алюминия.В центре сварного шва этот режим затвердевания приводит к относительно длинным и непрерывным сегрегациям на границах зерен в направлении сварки.
Рис. 3СЭМ-характеристика горизонтальных поперечных сечений сварных швов, представленных на рис. 2, зон плавления чистого AA7075 и наночастиц AA7075. a и c Микроструктура вторичной фазы зоны плавления, сваренной с присадочным материалом AA7075. b , d и e Модифицированная вторичная фаза из сплава AA7075, сваренная с нанообработанным присадочным материалом. f Образец просвечивающего электронного микроскопа, показывающий поперечное сечение модифицированной вторичной фазы с помощью наночастиц наполнителя. г Типичное электронно-микроскопическое изображение границы раздела между наночастицей TiC и вторичной фазой (обозначено как MgZn 2 ) с высоким разрешением. ч Фурье-фильтрованное изображение ПЭМ высокого разрешения, соответствующее g . Масштабные линейки, 10 мкм в a , b , 1 мкм в c , d , e , f и 2 нм в g , h
Как указано ранее, рост дендритных зерен нежелателен, так как он может вызвать макроскопические или микроскопические полости и трещины.Кроме того, такие непрерывные продольные особенности вторичной фазы приводят к тому, что MZ имеет низкую прочность на растяжение перпендикулярно направлению сварки. При большем увеличении на рис. 3с наблюдается, что вторичная фаза чистого сплава затвердевает в больших эвтектических областях Mg (Zn, Cu, Al) 2 , особенно в тройных стыках границ зерен. На рис. 3б показана типичная вторичная фаза в присутствии наночастиц TiC. Здесь вторичная фаза сегментирована, а ее фрагменты ориентированы случайным образом, более мелкие и более короткие, чем ее аналоги в чистом сплаве.На рис. 3d показаны области локально более крупных интерметаллидов в зоне плавления, обработанной наночастицами. Здесь продвигающиеся границы зерен накапливают TiC на конечных стадиях затвердевания, что приводит к локально более высокому объемному процентному содержанию наночастиц во вторичной фазе. Таким образом, возникновение и размер эвтектических особенностей резко сократились. На вставке рис. 3д показана одна из немногих пластинчатых фаз Mg (Zn, Cu, Al) 2 , образующихся во время затвердевания. Наночастицы изменили его регулярный пластинчатый узор, разорвав связи внутри структуры.Эти данные согласуются с пониженной склонностью к растрескиванию в зоне плавления. Более мелкие, беспорядочно ориентированные сегрегации и уменьшенный размер разделенных эвтектических элементов в сочетании с круглыми и равноосными зернами предполагают высокую текучесть вторичной фазы вплоть до конечной стадии затвердевания. Следовательно, захват жидких карманов вторичной фазы, которые ответственны за растрескивание при затвердевании, маловероятен.
Чтобы четко выявить границу раздела между наночастицами TiC и вторичными фазами Mg (Zn, Cu, Al) 2 , был использован анализ ПЭМ в атомном масштабе.На рис. 3f показано СЭМ-изображение образца ПЭМ, вырезанного из наночастиц эвтектики Mg (Zn, Cu, Al) 2 , содержащих наночастицы TiC. Как показано на рисунке, наблюдается, что большинство наночастиц TiC остается либо внутри вторичной фазы, либо на границе между матрицей Al и фазой Mg (Zn, Cu, Al) 2 . Это указывает на то, что наночастицы TiC предпочитают оставаться в фазах Mg (Zn, Cu, Al) 2 во время затвердевания и эффективно изменять размер, форму и распределение вторичных фаз в MZ.На рисунке 3g показана типичная граница раздела между наночастицами TiC и вторичной фазой. Рисунок 3h — это ПЭМ-изображение с атомным разрешением, прошедшее фильтр Фурье, соответствующее рисунку 3g. Наблюдаемая вторичная фаза была идентифицирована как фаза MgZn 2 по ее атомной структуре. Как показано на рис. 3h, плоскости (11 \ (\ bar 20 \)) и (1 \ (\ bar 2 \) 10) MgZn 2 были идентифицированы под углом 120 °. Фаза MgZn 2 ориентирована по направлению к оси зоны [0001]. Кроме того, плоскости (111), (\ (\ bar 1 \) 11) и (200) наночастиц TiC идентифицированы и отмечены в атомной структуре.Наблюдаемая наночастица TiC ориентирована по направлению к оси зоны \ ([01 \ bar 1] \). Плоскости (111) TiC параллельны плоскостям (11 \ (\ bar 20 \)) MgZn 2 . Плоскости (\ (\ bar 1 \) 11) TiC имеют угол примерно 10 ° между плоскостью (1 \ (\ bar 2 \) 10) MgZn 2 . Планарные расстояния (\ (\ bar 1 \) 11) TiC и (1 \ (\ bar 2 \) 10) MgZn 2 составляют 0,2499 нм и 0,2609 нм соответственно. Таким образом, рассогласование на границе раздела TiC-MgZn 2 рассчитано приблизительно равным 5.6%, что указывает на полукогерентный интерфейс. Хорошее соответствие решеток также объясняет, почему наночастицы TiC имеют тенденцию присоединяться к вторичной фазе MgZn 2 и эффективно изменять MgZn 2 для улучшения качества сварки.
Термический анализ процесса затвердевания
Чтобы лучше интерпретировать изменения, которые наночастицы TiC вносят в морфологию α-зерна AA7075 и морфологию вторичной фазы, образцы зон плавления соединений, сваренных с использованием чистого и наночищенного присадочного стержня AA7075, были проанализированы с использованием дифференциальной сканирующей калориметрии (ДСК). ).При сравнении двух кривых охлаждения на рис. 4а пики тепловыделения при зарождении α-зерен существенно различаются. Кривая, представляющая чистый материал, показывает крутое увеличение и крутое уменьшение до и после достижения его первого минимума. Это указывает на хорошо изученный взрывной рост α-зерен после их успешного зарождения. Напротив, амплитуда α-пика наноразмерного образца примерно на 20% ниже, в то время как наклон после достижения максимума оказывается менее крутым. Это говорит о том, что рост альфа-зерен наноразмерного сплава замедлился, как предполагалось ранее, что привело к более непрерывному зародышеобразованию.
Рис. 4Анализ ДСК зон плавления чистого AA7075 и наночастиц AA7075. a Кривые охлаждения ДСК, показывающие нормированный тепловой поток образцов зоны плавления, взятых из соединений, сваренных с использованием присадочного материала AA7075 и нанообработанного присадочного материала AA7075. b Кривые зависимости твердой фракции от температуры, полученные из результатов ДСК
Сравнивая кривые твердой фракции, полученные из кривой теплового потока, показанной в 4b , это явление становится более очевидным.Резкая точка поворота на кривой твердой фракции чистого образца характерна для неблагоприятных механизмов затвердевания материала. Для образца, сваренного с наполнителем, содержащим 1,7 об.% TiC, эта точка оборота сглаживается и показывает непрерывный рост зерна до критических конечных стадий затвердевания, на которых начинается растрескивание при затвердевании. Кроме того, начало зародышеобразования вторичной фазы задерживается почти на 12 ° C для сплава, обработанного наночастицами. Эта задержка в сочетании с закрепленным и ограниченным ростом α-зерен подтверждает теорию улучшенной текучести жидкого расплава в процессе затвердевания в зоне плавления.
Механические свойства
Для демонстрации влияния нанообработанного присадочного материала AA7075 на механические свойства сварного шва были проведены испытания на микротвердость и растяжение. Чтобы подчеркнуть превосходные характеристики этого присадочного материала по сравнению с обычным присадочным материалом ER5356, карты микротвердости поперечного сечения для сварных швов, выполненных с использованием присадочного материала ER5356 и наночастиц AA7075, показаны на рис. 5a. Высокая микротвердость зоны плавления последнего в состоянии после сварки по сравнению с обычным присадочным прутком может быть объяснена измененным химическим составом и общеизвестными механизмами упрочнения в нанокомпозитах с металлической матрицей, такими как эффект Холла-Петча 29 и Орован усиление 30 .Поскольку параметры поддерживались постоянными для всех экспериментов по сварке, следует также отметить, что деградация PMZ и HAZ снижается при сварке с наноразмерным присадочным материалом. Объяснение этому можно найти в исследовании Ма нанокомпозитов никеля, обработанных лазером 18 . Несмотря на то, что в текущем исследовании только зона плавления содержит наночастицы, ожидается, что изменение вязкости и теплопроводности зоны плавления приведет к изменению теплового потока в системе.
Рис. 5Механические свойства нанообработанных сварных швов AA7075. a Испытания на микротвердость проводились по средней линии поперечных вертикальных сечений. На графике сравниваются значения твердости по Виккеру сварных швов, выполненных с присадочным материалом ER5356 и нанообработанным присадочным материалом AA7075 в условиях термообработки после сварки и после сварки. b слева направо, синие полосы показывают выбор обычно сваренных GTAW высокопрочных алюминиевых сплавов 36, 37 , AA7075, сваренных с присадочным материалом ER5356. 11 и AA7075, сваренных с нанообработанным присадочным материалом AA7075.Красные столбцы показывают модифицированную непрямую электродуговую сварку AA7075 (MIEA) с ER5356 в качестве присадочного материала 38 и AA7075, сваренные с наноразмерным присадочным материалом AA7075 после такой же PWHT. Полосы ошибок показывают s.d. из 4 испытанных образцов
Дополнительное важное преимущество нанообработанного присадочного материала AA7075 становится очевидным при сравнении результатов микротвердости двух образцов после термообработки после сварки (см. Методы). Поскольку стержень из нанокомпозитного наполнителя имитирует химический состав основного материала, зона плавления становится полностью термообработанной и даже превышает уровень твердости основного материала из-за армирования наночастицами.Кроме того, закрепляющий эффект наночастиц ограничивает рост зерна в зоне плавления во время термообработки, в результате чего размер зерна после термообработки составляет 13 ± 6,2 мкм. Напротив, при сварке обычного ER5356 в виде V-образной канавки только около 20% упрочняющих легирующих компонентов основного материала растворяется в зоне плавления. Следовательно, увеличение твердости в пределах MZ после термообработки гораздо менее значимо.
Для дальнейшего изучения применимости этого присадочного материала из сварного шва были вырезаны поперечные растягивающие стержни и испытаны в состоянии после сварки и после термообработки.На рис. 5b показан выбор сварных высокопрочных алюминиевых сплавов, а также результаты настоящего исследования. Для случая после сварки предел прочности на разрыв достиг максимума 392 МПа (в среднем 376 ± 15 МПа) при удлинении на 1,5%, что значительно выше, чем свойства при растяжении, указанные при использовании обычного ER5356.
Хотя PMZ могла бы быть обозначенной зоной разрушения, учитывая ее твердость, образец разрушился в зоне плавления. Улучшение механических характеристик можно ожидать, если уменьшить количество сварочных дефектов и оптимизировать общие параметры сварки.
Как уже указывалось на микротвердости поперечного сечения, истинное достоинство наноразмерного наполнителя в отношении механических свойств становится очевидным при термообработке стержней на растяжение до состояния Т6. Испытания на растяжение термообработанного образца достигли предела прочности при растяжении 551 МПа (в среднем 531 ± 19 МПа), что находится в пределах 93% от деформируемого значения 31 AA7075-T6 при удлинении 5,21%. Примечательно, что образец, демонстрирующий наивысшие свойства при растяжении, разрушился в начале калибра стержня на растяжение на большом расстоянии от MZ и PMZ.Это указывает на то, что при термообработке полученное сварное соединение, возможно, будет таким же прочным, как и исходный деформируемый материал. Сводные данные о пределе прочности на растяжение в поперечном направлении сварных швов AA7075, подвергнутых нанообработке, по сравнению с сваркой AA7075, сваренной с присадочным материалом ER5356 и другими обычно свариваемыми алюминиевыми сплавами, можно найти на рис. 5b.
Сварка алюминиевых сплавов
Особые свойства, влияющие на сварку, — это его оксид. характеристики, его тепловые, электрические и немагнитные характеристики, отсутствие изменения цвета при нагревании и широкий диапазон механических свойств и температур плавления, который в результате сплавления с другими металлами…
Алюминий и его сплавы можно соединить большим количеством способов, чем любой другой металл, но алюминий имеет несколько химических и физических свойств, которые необходимо понять при использовании различных процессов соединения.
Специфические свойства, влияющие на сварку, — это его оксидные характеристики, тепловые, электрические и немагнитные характеристики, отсутствие изменения цвета при нагретый, а также широкий диапазон механических свойств и температур плавления, которые в результате сплавления с другими металлами.
Оксид. Оксид алюминия плавится примерно при 2050 ° С o ° C, что намного выше чем температура плавления основного сплава. Если оксид не удален или не вытеснен, результат — неполное слияние. В некоторых процессах соединения хлориды и фториды используются для удаления оксида. Хлориды и фториды должны быть удаляется после операции соединения, чтобы избежать возможной проблемы с коррозией в услуга.
Растворимость в водороде. Водород очень быстро растворяется в расплавленном алюминии. Однако водород почти не растворяется в твердом алюминии, и он был определено как основная причина пористости в сварных швах алюминия. Высокие температуры сварочной ванны позволяют абсорбировать большое количество водорода, а также затвердевает, растворимость водорода сильно снижается. Водород, превышающий эффективный предел растворимости образует газовую пористость, если он не выходит из затвердевающий сварной шов.
Электропроводность. Для дуговой сварки важно, чтобы алюминий сплавы обладают высокой электропроводностью — у чистого алюминия 62% от чистого алюминия. медь. Высокая электропроводность позволяет использовать пистолеты с длинными контактными трубками, потому что резистивный нагрев электрода не происходит, как это происходит с электроды из черных металлов.
Тепловые характеристики. Теплопроводность алюминия около 6
раз больше стали.Хотя температура плавления алюминиевых сплавов составляет
значительно ниже, чем у ферросплавов, требуются более высокие тепловыделения для
сваривать алюминий из-за его высокой удельной теплоемкости.
Высокая теплопроводность делает алюминий очень чувствительным к колебаниям тепла.
ввод сварочного процесса.
Формы алюминия. Большинство форм алюминия можно сваривать. Все кованые
формы (листы, плиты, штампы, поковки, стержни, стержни и ударные штампы), а также
можно сваривать как в песчаные формы, так и в постоянные формы.Сварка на обычных
литье под давлением создает чрезмерную пористость как в сварном шве, так и в основном металле
рядом со сварным швом из-за внутреннего газа. Однако вакуумное литье под давлением
была сварена с отличными результатами. Детали порошковой металлургии (P / M) также могут пострадать
от пористости при сварке из-за внутреннего газа.
Состав сплава — гораздо более важный фактор, чем форма в
определение свариваемости алюминиевого сплава.
Критерии выбора присадочного сплава
При выборе оптимального присадочного сплава необходимо учитывать область применения (конечное использование) сварного деталь и ее желаемые характеристики должны быть первоочередными соображениями.Многие сплавы и Комбинации сплавов могут быть соединены с использованием любого из нескольких присадочных сплавов, но только один наполнитель может быть оптимальным для конкретного применения.
При выборе присадочного сплава для сварки обычно учитываются следующие основные факторы:
- Легкость сварки
- Прочность сварного шва на растяжение или сдвиг
- Пластичность сварного шва
- Рабочая температура
- Коррозионная стойкость
- Соответствие цвета сварного шва и основного сплава после анодирования
- Чувствительность к растрескиванию сварного шва.
Простота сварки — это первое, на что обращают внимание на большинство сварочных работ. В Как правило, нетермообрабатываемые алюминиевые сплавы можно сваривать с присадочным сплавом. того же основного состава, что и базовый сплав.
Термически обрабатываемые алюминиевые сплавы несколько более сложны в металлургическом отношении и более чувствителен к «горячим коротким» трещинам, возникающим в зоне термического влияния (HAZ) ликвидация при сварке.Как правило, разнородный сплав наполнитель с более высоким содержанием растворенных веществ (например, медь или кремний) используется в Это дело.
- Высокочистые сплавы серий 1ххх и 3003 легко свариваются с основным сплавом. наполнитель, сплав 1100 или наполнитель из сплава алюминия и кремния, например 4043.
- Сплав 2219 демонстрирует лучшую свариваемость среди основных сплавов серии 2ххх и является легко сваривается с присадками 2319, 4043 и 4145.
- Алюминий-кремний-медный присадочный сплав 4145 обеспечивает наименьшую восприимчивость к растрескивание сварных швов деформируемыми медными подшипниковыми сплавами серии 2ххх, а также отливки из алюминиево-медных и алюминиево-кремний-медных алюминиевых сплавов
- Растрескивание сварных швов из алюминиево-магниевого сплава уменьшается по мере того, как магний содержание сварного шва увеличивается выше 2%.
- Базовые сплавы серии 6xxx легче всего свариваются с алюминиево-кремниевым сплавом. типа присадочных сплавов, таких как 4043 и 4047. Однако алюминиево-магниевый тип присадочные сплавы также могут удовлетворительно использоваться с подшипником с низким содержанием меди 6xxx сплавы, когда требуются более высокая прочность на сдвиг и пластичность металла шва.
- Сплавы серии 7xxx (алюминий-цинк-магний) демонстрируют широкий диапазон трещин.
чувствительность при сварке. Сплавы 7005 и 7039 с низким содержанием меди
(
Сварочные процессы
Процесс GTAW (газовая дуговая сварка) использовался для сварки толщиной от От 0,25 до 150 мм и может использоваться во всех положениях сварки.Потому что это относительно медленный, он очень маневренный для сварки труб, трубопроводов различной формы. Это обеспечивает превосходный контроль проплавления и позволяет производить сварные швы с отличной прочностью. Кратеры окончания сварки могут быть легко заполнены, поскольку ток снижается с помощью ножная педаль или электронное управление.
Процесс ac — GTAW обеспечивает действие дуговой очистки для удаления поверхности оксида во время положительного электрода половины цикла и проникающей дуги, когда электрод работает с отрицательной полярностью.
Постоянный ток — процесс GTAW. Постоянный ток отрицательной полярности может быть применяется для сварки алюминия ручным и механизированным способом.
Другие процессы дуговой сварки включают дуговую сварку в среде защитного металла (SMAW), т.к. а также электрошлаковая и электрогазовая сварка (ESW, EGW). SMAW со стержнями, покрытыми флюсом был в значительной степени заменен процессом GMAW.
В процессе кислородно-газовой сварки (OFW) используется флюс или оксиацетилен. или пламя кислородно-водородного газа.Когда используется кислородно-ацетиленовое пламя, немного снижается требуется пламя, которое вызывает углеродистые отложения, закрывающие сварной шов и замедляет скорость движения.
Электронно-лучевая сварка (EBW) в вакуумной камере дает очень глубокую, узкий проплав при высоких скоростях сварки.