Зенковка — Википедия
Материал из Википедии — свободной энциклопедии
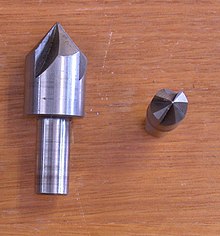
Зенко́вка — многолезвийный режущий инструмент для обработки отверстий в деталях с целью получения конических или цилиндрических углублений, опорных плоскостей вокруг отверстий или снятия фасок центровых отверстий. Применяется для обработки просверлённых отверстий под головки болтов, винтов и заклёпок.
Зенковки для цилиндрических углублений и опорных плоскостей часто называют цековками.
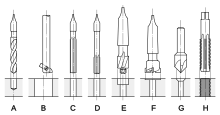
По форме режущей части зенковки подразделяются на:
- цилиндрические
- конические
- торцовые (цековки).
Цилиндрические зенковки состоят из рабочей части и хвостовика. Для обеспечения соосности отверстия и образованного зенковкой углубления имеют направляющую цапфу.
Конические зенковки также состоят из рабочей части и хвостовика. Для обеспечения соосности отверстия и образованного зенковкой углубления могут иметь направляющую цапфу. Бывают прямые и обратные-двухсоставные (используемые при отсутствии прямого подхода).
Цековки предназначены для зачистки торцевых поверхностей бобышек под шайбы, упорные кольца или гайки.
По диаметру обрабатываемых отверстий:
- для отверстий от 0,5 до 1,5 мм (простые)
- для отверстий от 0,5 до 6 мм (без предохранительного или с предохранительным конусом)
- для отверстий от 8 до 12 мм (с конусным хвостовиком)
- ГОСТ 14953—80 Зенковки конические. Технические условия
Чем отличается зенкование от зенкерования — сверление, инструмент, особенности зенкования
Зенкование и зенкерование, несмотря на схожесть названий, являются разными операциями металлообработки с соответствующим инструментом. Схожесть операций в типе обработки и обрабатываемой поверхности. И зенкование, и зенкерование подразумевает механическую обработку резанием внутренней поверхности отверстий. Различия в характере обработки и, соответственно, получаемом результате.
Зенкерование: инструмент и особенности
Зенкерование – это промежуточный процесс обработки отверстий располагаемый, как правило, между сверлением и разверткой. Это получистовая обработка отверстия с целью:
- повышения точности отверстия до 4-го и даже 5-го класса;
- улучшения шероховатости;
- придания строгой геометрической формы.
Также зенкерование применяется при обработке отверстий полученных литьём или обработкой давлением.
Обработка производится с помощью зенкера, инструмента внешне похожего на сверло, но имеющего ряд конструктивных отличий. Основные отличия – это увеличенная перемычка между режущими кромками, увеличенное количество рабочих кромок и срезанный угол. Всё это обеспечивает высокую устойчивость зенкера и его соосность с обрабатываемым отверстием. Так, наличие 3-4 режущих кромок обеспечивает плавное распределение сил в зоне контакта зенкера с обрабатываемой деталью. Геометрия режущей части обеспечивает обработку отверстия без съема металла в продольном направлении.
Зенкеры различаются по количеству зубьев (3 или 4) и конструкции – насадные, цельные и вставные. Выбор инструмента зависит от диаметра отверстия. Так, применение вставных зенкеров (с вставными ножами) рекомендуется для отверстий диаметром от 20 мм., цельные применяются для малых диаметров (от 12 мм.).
Для получения более точных и сложных поверхностей используются комбинированные типы инструмента с большим количеством режущих кромок (до 8). При этом сборные зенкеры применяются совместно с другим металлорежущим инструментом – сверлами, развертками и т. д.
Особенности зенкования
Зенкование – это механическая обработка отверстий с целью создания различных геометрических углублений для потайного размещения крепежных изделий. Также она применяется для нарезки внутренних фасок. Для этих целей есть специальный инструмент – зенковка, имеющие различную форму. Выбор зенковки зависит от необходимого конечного результата.
Основные виды зенковок
- Цилиндрические зенковки. Применяются для получения цилиндрических выемок в просверленных отверстиях под установку болтов и винтов.
- Конические зенковки. Используются для вырезания отверстий конусной формы внутри детали, а также для зачистки острых кромок, снятия фасок и подготовки углублений под крепежные элементы. Чаще всего применяется инструмент с конусным углом 90° и 120°.
- Плоские или торцевые зенковки, также можно встретить название цековки. Преимущественно применяются для зачистки и обработки углублений перед установкой крепежных изделий.
Зенковка состоит из рабочей части и хвостовика со специальной цапфой выполняющей функцию направляющего пояса. Цапфа необходима для контроля соосности в процессе нарезки углублений.
Оборудование
Для зенкования и зенкерования используется, чаще всего, сверлильные станки различного типа. Также может быть использован обрабатывающий центр или токарный станок – практически тоже самое оборудование, на котором выполняются и операции сверления. Для обеих операций не рекомендуется использовать ручной инструмент из-за недостаточной точности позиционирования.
Зенковка — что это, виды и применение, конструкция, зенкование и ГОСТ.
Зенковка – это металлорежущий инструмент с несколькими рабочими лезвиями, предназначенный для обработки предварительно просверленных отверстий цилиндрической или конической формы. С помощью зенковки, при выборе необходимого типа инструмента, можно получить различные по конфигурации углубления в отверстиях обрабатываемых деталей. Не следует путать зенковку с зенкерованием, рассверливанием отверстий на всю длину для повышения качества поверхности.
Виды и применение зенковок
При обработке деталей на сверлильных и токарных станках зенковка по металлу применяется для:
- Формирование в предварительно подготовленных отверстиях углублений конической или цилиндрической формы требуемой длины.
- Формирование опорных плоскостей возле отверстий.
- Съём фаски в отверстиях.
- Обработка отверстий под крепеж.
Часто можно встретить и термин «цековка», так называют инструмент, предназначенный для рассверливания углублений цилиндрической формы и опорных плоскостей.
По конфигурации режущей части встречаются следующие виды зенковок:
- Цилиндрической конфигурации.
- Конические зенковки.
- Торцовые инструменты.
По диаметру обрабатываемых отверстий зенковки подразделяются на:
- Простые (от 0,5 до 1,5 мм).
- Для отверстий диаметром от 0,5 до 6 мм. Выпускаются с предохранительным или без предохранительного конуса.
- Зенковки с конусным хвостовиком. Применяются для отверстий диаметром от 8 до 12 мм.
Конструкция
Зенковка коническая состоит из двух основных элементов — рабочей части и хвостовика. Рабочая часть имеет конус со стандартным рядом углов на вершине от 60 до 120°. Количество режущих лезвий зависит от диаметра инструмента и может быть от 6 до 12 штук.
Цилиндрическая зенковка по своей конструкции похожа на сверло, но имеет больше режущих элементов. На торце расположена направляющая цапфа необходимая для фиксации положения инструмента в процессе обработки. Ограничитель может быть съёмным или быть часть тела инструмента. Первый вариант более практичен, так как расширяет возможности обработки. Также может быть установлена режущая насадка.
При необходимости рассверливания нескольких отверстий на равную глубину применяется инструмент с державками с вращающимся или неподвижным ограничителем. Перед обработкой зенковка фиксируется в державке таким образом, чтобы режущая часть выступала из упора на расстояние равное требуемой глубине обработки отверстий.
Инструмент изготавливается из инструментальных легированных, углеродистых, быстрорежущих и твердосплавных марок стали. Для обработки чугунных деталей чаще всего используются твердосплавные стали, для обычных сталей – быстрорежущие и инструментальные.
Особенности зенкования отверстий
Приведём некоторые рекомендации для металлообработки методом зенкования:
- При обработке твердых сплавов и чугуна необходимо использовать охлаждающие эмульсионные составы для отвода тепла.
- Очень важно правильно подобрать инструмент для проведения работ. Необходимо учесть материал заготовки и характер работ.
- При подбое зенковки особое внимание уделите заданным параметрам обработки – диаметр, потребная точность, размер углубления.
- Обратите внимание на способ фиксации на станке, при необходимости приобретите необходимую дополнительную оснастку.
Действующий ГОСТ
Определяет технические условия для конической зенковки ГОСТ 14953-80. Также, при металлообработке, следует руководствоваться другими стандартами регулирующими параметры используемых сходных инструментов – зенкеров, разверток и т. д. Подбор зенковок необходимо производить по таблицам в специальной литературе.
что это такое, особенности процесса, инструменты
При сборке конструкций и металлических узлов используют резьбовые соединения, заклепки. Иногда требуется спрятать головку болта, винта или соединения другого типа. В этих случаях используют так называемый потай. То есть в начале соединительного отверстия в металле делают небольшое углубление, куда и прячется головка. Выполнить такой потай можно, применив зенкование, – это определенный вид обработки начала отверстия, когда его расширяют в диаметре и углубляют на определенную высоту. Форма углубления может быть разной.
Зенкование не стоит путать с зенкерованием – это различные операции, которые выполняются разными инструментами. Но оборудование, которое приводит в движение такие резцы, может быть одинаковым.
Зенкование можно провести при помощи ручной электрической дрели. Отличием от заводского варианта здесь будет невысокий класс точности обработки, но получить потай в домашних условиях вполне реально.
Сущность процесса зенкования
Зенкование и сверление тесно связаны между собой. Обычно зенкование проводят по готовому отверстию, но бывают случаи, когда необходимо сделать углубление без предварительного сверления. И в том, и в другом вариантах используют инструмент зенковку разных конструкций.
Сам процесс зенкования очень прост: специальным резцом снимают фаску на отверстии. Чем больше металла снято, тем больше получается углубление. Форма зенковки обычно коническая. Здесь главное – соблюсти строгую центровку режущего элемента и отверстия: должна быть идеальная соосность. В противном случае будет наблюдаться смещение углубления относительно отверстия, и шляпка винта не сможет в него войти.
Чтобы выполнить операцию зенкования для получения фасок и для углублений, необходимо пройти следующие этапы технологического процесса:
- Измерить шляпку резьбового метиза, под который будет производиться углубление (имеются в виду как диаметр, высота, так и угол скоса, если шляпка имеет конструкцию под потай).
- Подобрать соответствующую зенковку и закрепить ее в сверлильном или токарном оборудовании.
- Строго соблюдая соотношение осей, закрепить напротив резца заготовку с отверстием.
- Включить сверлильное оборудование и выставить необходимое количество оборотов (если это позволяет схемотехника станка) или заведомо подобрать необходимый инструмент под параметры оборудования.
- Провести зенкование отверстия.
Назначение и особенности зенкования
Основная сфера применения зенкования – в технологических процессах при изготовлении станков, механизмов и сборке металлоконструкций. С помощью этой операции добиваются решения следующих задач:
- В предварительно изготовленных отверстиях получают углубления в форме цилиндра или конуса.
- Формируют плоскости опорного значения в районе отверстий.
- Зенкование отверстий позволяет получить каналы со снятой в них фаской.
- Формирование углублений для сокрытия элементов резьбового крепежа.
Зенкование отверстий имеет свои особенности; они обусловлены типом металла, который подвергается обработке, конструкцией резца и конечной задачей операции:
- Если проводится обработка чугунных деталей или металлов на основе твердых сплавов, то в рабочую область следует подавать специальную эмульсию для охлаждения.
- Рабочие обороты вала двигателя должны соответствовать рабочим оборотам зенковки. Для инструмента из быстрорежущей стали обороты всегда меньше, чем для инструмента с напайками из твердого сплава.
- Для выборки под потайную шляпку винта используют конический резец с углом торцевых ножей, равным углу конуса шляпки.
Зенковку делают на самом последнем этапе после зенкерования и развертки.
Отличия зенкерования от зенкования
Зенкование и зенкерование – совершенно разные операции по обработке отверстий. Процесс зенкерования связан с воздействием на весь просверленный канал. И цель зенкерования в том, чтобы выровнять это отверстие, сделать его более качественным с точки зрения всех геометрических показателей и чистоты поверхности канала. Для зенкерования разработан свой специализированный инструмент (зенкер), основные ножи которого расположены по спирали вдоль всего тела инструмента (длина тела, как правило, превышает длину канала отверстия).
Зенковка работает только с частью отверстия в его начале. Ее основная задача – сделать потай или снять фаску. Поэтому в инструменте предусмотрены в основном ножи на торце. Единственное, что общего между зенкером и зенковкой, – они приводятся в движение при помощи одинаковых станков.
Оборудование и инструменты
Главный инструмент, которым выполняют зенкование, называется зенковкой. Это тип резца, состоящий из рабочей части и хвостовика. Рабочая часть имеет несколько режущих кромок, за хвостовик инструмент крепится в патроне оборудования. Бывают резцы конической и цилиндрической формы. Сырьем для изготовления зенковок служит сталь инструментальная углеродистая либо легированная.
Зенковки конического типа характеризуются углом наклона ножа. Наиболее используемые элементы с углами конуса 120, 90, 60 и 30 градусов. Резцы цилиндрического типа на торце имеют зубья. Этих зубьев может быть от 8 до 4 штук. Кроме этого, у цилиндрического инструмента есть направляющий по отверстию элемент, который называется цапфой. Благодаря такому элементу цилиндрический резец всегда имеет соосность с отверстием, которое он обрабатывает.
Для зенкования отверстий разработаны также специальные державки, куда вставлены зенковки. У них могут быть ограничители вращающегося и невращающегося типа.
Обозначение зенковки на чертеже
На производстве зенкование отверстий выполняют по чертежу. Зенковка на чертеже отображается прописными и заглавными латинскими буквами и арабскими цифрами. Значение букв и цифр следующее:
- d1 – указывает на основной диаметр канала;
- d2 – на диаметр зенкования;
- L1 – отображает показатель длины цилиндрического канала;
- L3 – это глубина зенкования;
- L4 – указывает на глубину фаски;
- j – это размер угла зенкования центральный;
- α (альфа) – размер угла фаски.
Уважаемые посетители сайта: инженеры машиностроения, мастера и просто ориентирующиеся в теме, – поддержите обсуждение в комментариях! Нам очень важны ваши профессиональные замечания.
В чем отличие зенковки от цековки
При сборке конструкций и механизмов часто возникает необходимость в подготовке и высокоточной обработке опорных поверхностей под головки крепежных болтов или винтов. Для этого существует специальный металлорежущий и металлообрабатывающий инструмент – зенковки и цековки. Несмотря на схожую геометрию, они имеют разное предназначение.
Что такое зенкование?
Зенкование – расширение входной части круглого отверстия для винтов с цилиндрическими или коническими (потайными) головками. Этот технологический процесс выполняется зенковкой соответствующей формы. Конические создают опорную поверхность с углом скоса 60, 75, 90, 120 градусов. Как подобрать коническую зенковку по размеру крепежа, можно узнать из предыдущей статьи.
Цилиндрические зенковки формируют углубление в форме цилиндра под винты с внутренним шестигранником DIN 912 или под винты с полукруглыми и шестигранными головками, которые согласно проекту должны быть утоплены в теле детали. Инструмент имеет зубья на торце и направляющую цапфу для точного центрирования режущей части относительно оси отверстия.
Что такое цекование?
Цекование – это следующий этап подготовки отверстия, который заключается в чистовой обработке (выравнивание, зачистка) плоского дна уже сформированного углубления в теле детали. Цековка тоже имеет торцевые зубцы и цапфу, а на боковой поверхности стружечные канавки. Цапфа может быть сменной или постоянной.
Цекование позволяет получить абсолютно гладкие, ровные опорные плоскости под упорные кольца, плоские шайбы или головки крепежных деталей, а также позволяет добиться идеальной перпендикулярности между опорной плоскостью и осью отверстия.
По сути цековка по металлу выполняет ту же работу, что и зенкер, только зенкер обрабатывает стенки отверстия, а цековка – торцы. Именно поэтому ее часто называют торцевым зенкером. Еще ее применяют для проточки клапанов, подрезания и зачистки торцов бобышек под шайбы, упорные кольца, гайки. Ею можно подравнивать заглубленные уступы, сформированные в результате сверления ступенчатых отверстий.
Вывод:
— Если нужно расширить входную часть просверленного отверстия для посадки головок крепежа – используйте цилиндрическую зенковку.
— Если необходимо повысить качество обработки торцевой части изготовленного углубления – выбирайте цековку.
Какова оптимальная скорость резания?
При зенковании или цековании скорость резания устанавливается в зависимости от обрабатываемого материала. Оптимальные значения приведены ниже.
Источник – «Энциклопедия по машиностроению XXL».
Сталь HB ≤ 180 | 10-18 м/мин |
Сталь HB ≥ 180 | 7-12 м/мин |
Чугун твердый | 7-12 м/мин |
Чугун средней твердости, бронза | 12-23 м/мин |
Алюминиевые сплавы | 40-65 м/мин |
Примечание: Наименьшие значения скорости соответствуют инструменту большего диаметра, а наибольшие значения – меньшему диаметру. При использовании твердосплавных зенковок и цековок возможно увеличение скорости в 1.8-2 раза.
Другие параметры, задаваемые на обрабатывающем станке, такие как глубина резания, подача, поправочные коэффициенты, мощность, являются расчетными и определяются по табличным данным из действующих в отрасли нормативных документов.
Полезные советы 13.09.2019 12:28:11
Отзывы могут оставлять только зарегистрированные пользователи. Пожалуйста, зарегистрируйтесь
Написать отзыв
Зенкерование — Википедия
Материал из Википедии — свободной энциклопедии
Текущая версия страницы пока не проверялась опытными участниками и может значительно отличаться от версии, проверенной 29 марта 2018; проверки требуют 4 правки. Текущая версия страницы пока не проверялась опытными участниками и может значительно отличаться от версии, проверенной 29 марта 2018; проверки требуют 4 правки.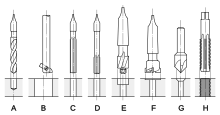
Зенкерование (от нем. senken «проходить, углублять <шахту>») — вид механической обработки резанием, в котором с помощью специальных инструментов (зенкеров) производится обработка цилиндрических и конических отверстий в деталях с целью увеличения их диаметра, повышения качества поверхности и точности. Зенкерование является получистовой обработкой резанием. По конструкции зенкеры бывают цельными или насадными, могут иметь различные направления угла спирали(правое, левое, прямое)
Не следует путать зенкерование с зенкованием — обработкой фаски (краев отверстия).
Зенкерование как получистовая и, отчасти, чистовая операция механической обработки имеет следующие основные назначения:
- Очистка и сглаживание поверхности отверстий: перед нарезанием резьбы или развёртыванием;
- Калибрование отверстий: для болтов, шпилек и другого крепежа.
Зенкерование выполняется в литьевых отверстиях с припуском для последующего развертывания или нарезания резьбы(зенкером N1 — в минусе от номинала) , либо получения проходного отверстия с квалитетом h21 и выше (зенкером N2).Возможна также предварительная обработка зенкером отверстий после сверления как правило перед развёртыванием для получения отверстий с необходимым квалитетом в особо ответственных деталях или сложнообрабатываемых материалах.
Выполнение зенкерования. Виды зенкеров[править | править код]
Зенкерование является точной операцией механической обработки и требует высокой мощности, соответственно, является машинной операцией и выполняется на следующих станках:
- Сверлильные станки всех типов: наиболее часто.
- Станки токарной группы: наиболее часто.
- Расточные станки: часто как вторичная операция.
- Фрезерные (горизонтальные и вертикальные): редко. В основном на фрезерных с ЧПУ (как часть программы).
- Агрегатные станки: как одна из операций в автоматической линии.
Зенкерование выполняется зенкерами. Зенкер представляет собой многолезвийный (3—12 лезвий) инструмент, имеющий ось вращения, при вращении которого его лезвиями производится обработка отверстия.
Основные виды зенкеров:
- Зенкеры машинные цельные с метрическим конусом либо конусом Морзе;
- Зенкеры насадные.
Зенкеры изготовляют преимущественно из быстрорежущих сталей или оснащёнными пластинами твёрдых сплавов. При зенкеровании широко применяются смазочно-охлаждающие вещества.
- Кожевников Д.В., Кирсанов С.В. Металлорежущие инструменты. Учебник (гриф УМО). Томск: Изд-во Томского ун-та. 2003. 392 с. (250 экз.).
- Кожевников Д.В., Кирсанов С.В. Резание материалов. Учебник (гриф УМО). М.:Машиностроение. 2007. 304 с. (2000 экз.).
Зенкер — Википедия
Материал из Википедии — свободной энциклопедии
Текущая версия страницы пока не проверялась опытными участниками и может значительно отличаться от версии, проверенной 6 апреля 2019; проверки требует 1 правка. Текущая версия страницы пока не проверялась опытными участниками и может значительно отличаться от версии, проверенной 6 апреля 2019; проверки требует 1 правка.Зенкер (нем. Senker) — многолезвийный (3 и более режущих кромок) режущий инструмент для обработки цилиндрических и конических отверстий в деталях с целью увеличения их диаметра, повышения качества поверхности и точности. Работа зенкером называется зенкерование. Зенкерование является получистовой обработкой резанием.
Зенкеры бывают с припуском для последующего развертывания (зенкер N1) или с квалитетом h21 (зенкер N2).
Часто зенкером ошибочно называют другой режущий инструмент — зенковку.
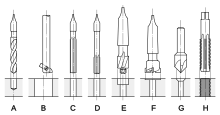
Зенкерование как получистовая и, отчасти, чистовая операция механической обработки имеет следующие основные назначения:
- Очистка и сглаживание поверхности отверстий: перед нарезанием резьбы или развёртыванием;
- Калибрование отверстий: для болтов, шпилек и другого крепежа.
Выполнение зенкерования. Виды зенкеров[править | править код]
Зенкерование является точной операцией механической обработки и требует высокой мощности, соответственно, является машинной операцией и выполняется на следующих станках:
- Сверлильные станки всех типов: наиболее часто.
- Станки токарной группы: наиболее часто.
- Расточные станки: часто как вторичная операция.
- Фрезерные (горизонтальные и вертикальные): редко. В основном на фрезерных с ЧПУ (как часть программы).
- Агрегатные станки: как одна из операций в автоматической линии.
Основные виды зенкеров:
Зенкеры машинные цельные внешним видом напоминает сверло и состоит из тех же элементов, но имеет большее количество режущих кромок и спиральных канавок.
Зенкеры изготовляют преимущественно из быстрорежущих сталей или оснащёнными пластинами твёрдых сплавов. При зенкеровании широко применяются смазочно-охлаждающие вещества.
- Кожевников Д. В., Кирсанов С. В. Металлорежущие инструменты. Учебник (гриф УМО). Томск: Изд-во Томского ун-та. 2003. 392 с. (250 экз.).
- Кожевников Д. В., Кирсанов С. В. Резание материалов. Учебник (гриф УМО). М.:Машиностроение. 2007. 304 с. (2000 экз.).