Простой ремесленный нож из напильника
Здравствуйте, уважаемые читатели и самоделкины!Многие из Вас очень интересуются различными самодельными ножами. На сегодняшний день в мире изготовлено такое количество их вариантов, что даже считать никто не возьмется.
В данной статье, автор YouTube канала «George Kosilov» расскажет Вам, как он изготовил мощный нож для различных ремесленных работ.

Этот нож похож на русский нож-косяк, он же сапожный нож. Его режущая кромка расположена на косой грани, и имеет односторонний спуск.
Материалы.
— Старый напильник

— Паракорд
— Наждачная бумага.
Инструменты, использованные автором.
— Газовая горелка
— Ленточный шлифовальный станок
— Болгарка, лепестковый зачистной диск
— Шуруповерт
Процесс изготовления.
Итак, автор нарисовал желаемую форму будущего ножа, и перенес ее на заготовку из напильника.


Зафиксировав напильник в тисках отрезает ненужные части. При этом необходимо постоянно охлаждать область, где будет режущая кромка. Иначе она потеряет прочность.

Затем срезает излишки металла в области рукоятки.


Выравнивает грани заготовки.

Устанавливает зачистной лепестковый диск, и зашлифовывает все поверхности.
Теперь отмечает будущую кромку спуска.

Далее дело за гриндером. Формирует спуск, и скругляет хвостовик.
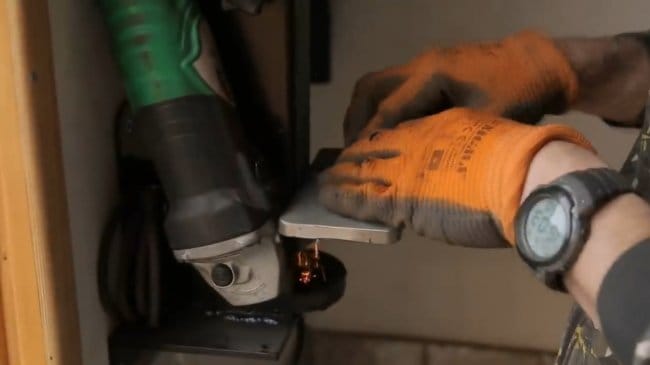
Затем разогревает хвостовик для облегчения его дальнейшей обработки. После остывания сталь станет мягче.

Кернит, сверлит отверстие в хвостовике, и раззенковывает его.
Зашлифовывает все грани наждачной бумагой 240-й гритности.
Остается заточить режущую кромку лезвия. Это можно сделать последовательно от 240-й до 600-й наждачной бумаги. При дальнейшей шлифовке, и увеличении гритности, следует смачивать наждачную бумагу водой.

Для оформления рукоятки мастер решил использовать паракорд, его потребуется около метра. Сложив шнур пополам, начинает завязывать узлы.


Это обычный узел, только завязывать его нужно с двух сторон рукоятки. Излишки шнура обрезаются, и приплавляются зажигалкой. Для пущей прочности шнур на рукоятке можно пропитать эпоксидной смолой, либо лаком.
Даже при не особо серьезной заточке вполне можно брить волосы. Да и карандаши прекрасно точит.
Более подробно технология термической обработки и заточки аналогичного ножа описана в недавней статье про японский нож киридаши.


Спасибо автору за идею простого, но мощного ножа для мастеровитых людей!


Всем хорошего настроения, удачи, и интересных идей!
Авторское видео можно найти здесь.
Источник
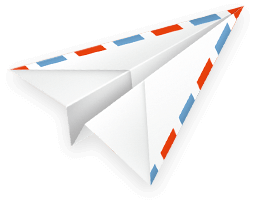
Получайте на почту подборку новых самоделок. Никакого спама, только полезные идеи!
*Заполняя форму вы соглашаетесь на обработку персональных данных
Становитесь автором сайта, публикуйте собственные статьи, описания самоделок с оплатой за текст. Подробнее здесь.Столярный нож из напильника своими руками
Здравствуйте, уважаемые читатели и самоделкины!Практически каждому из Вас весьма интересна тема ножей, особенно которые служат в мастерской незаменимым и надежным инструментом.
В данной статье, автор YouTube канала «Evgeniy Budilov» расскажет Вам, как он изготовил нож для работы с кожей, пластиком, или столярных работ.

Эта разновидность ножа весьма проста в изготовлении, и может быть повторена с небольшим количеством инструментов и станков.
Материалы.
— Старый напильник
— Силикатный кирпич
— Аэрозольная краска.
Инструменты, использованные автором.
— Газовая горелка
— Электрическая или газовая печь
— Струбцины
— Болгарка, отрезной диск
— Ленточный шлифовальный станок
— Инфракрасный цифровой термометр
— Точильный станок
— Дисковая металлическая щетка
— Заточной станок
— Маркер, керн, молоток.
Процесс изготовления.
Итак, основой для этого простого в изготовлении ножа послужит старый советский напильник. А как Вы наверное знаете, они изготавливаются из очень твердой, высококачественной инструментальной стали марок У10А, У13А.

Первым делом автор складывает из силикатного кирпича небольшой горн. В одном верхнем кирпиче есть специальное отверстие, в которое устанавливается газовая горелка. Она подключается к газовому баллону при помощи шланга.
Полностью напильник не помещается в камере горна, поэтому он отрезает хвостовик болгаркой.


Для того, чтобы металл легче поддавался обработке, его необходимо разогреть в печи.

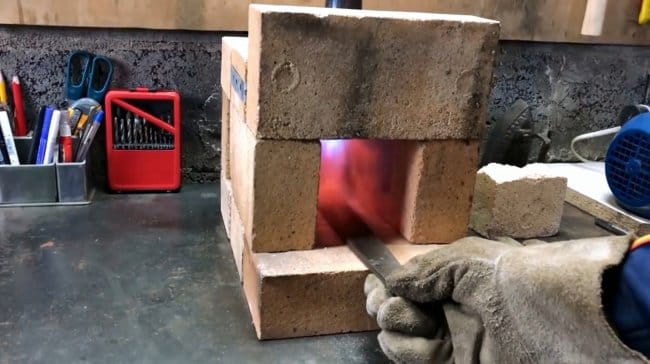
После полного прогрева до малинового цвета, автор закрывает камеру, и дает стали остыть.
Пока заготовка остывает, и происходит процесс отпуска, автор сделал небольшой набросок.
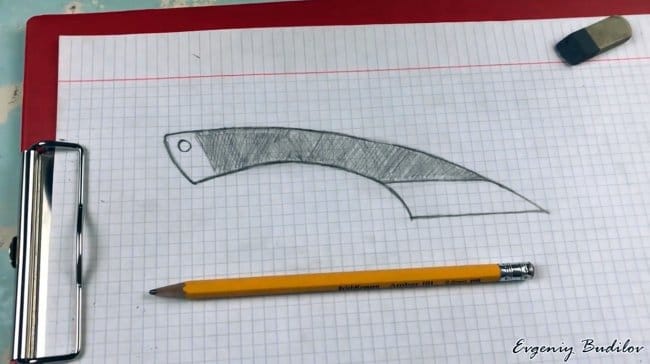
Попытавшись перенести контуры шаблона на заготовку с помощью маркера, стало ясно, что они плохо видны, и расплываются. Лучше сделать разметку при помощи белой аэрозольной краски.
Излишки материала удаляются, и заготовка отрезается.
Далее профиль будущего клинка обрабатывается при помощи ленточного шлифовального станка, периодически требуется охлаждать заготовку в воде.
Также выравнивается закругление рукоятки, и линия режущей кромки.


Теперь размечается и кернится хвостовик.


Отверстие в хвостовике высверливается сверлом с корундовой вставкой, обязательно использование смазки и низкие обороты станка.
Для того, чтобы точно сформировать спуски, мастер применяет хитрый прием. Он окрашивает край маркером, и прочерчивает линию кромки керном.
Теперь клинок фиксируется на специальном приспособлении, позволяющем наклонять заготовку под небольшим углом.
С помощью такого приспособления достаточно легко и точно можно сформировать спуски.


Первая сторона готова, заготовка разворачивается на 180 градусов, и формируется второй спуск.
Ножик получается весьма небольшой, но очень удобно лежит в руке. Лезвие разогревается в горне, и закаливается в машинном масле. Важно не просто опустить его в масло, а слегка помешивать, для более быстрого и равномерного остывания. Кроме того, критическая температура нагрева перед закалкой составляет 1300 градусов, при этом стальная заготовка будет светится белым цветом, а нормальный цвет — малиновый. Также можно контролировать достаточность прогрева при помощи магнита. При достижении необходимой температуры сталь теряет магнитные свойства. Вместо машинного масла лучше применять минеральное.
Итак, клинок остыл, и теперь выглядит вот так.


Теперь можно провести первый тест на качество закалки, для этого автор провел еще не заточенным лезвием по стеклянной бутылке. На ней остались весьма глубокие царапины.


После закалки клинок нужно отпустить в электрической или газовой печи при температуре около 200°C в течении двух часов. Затем печь отключается, и клинок остается в ней до полного остывания.


Поверхности клинка обрабатываются на точильном станке с дисковой металлической щеткой. Торцы и грани шлифуются при помощи гравировальной машинки.
Остается последний этап ручной заточки режущей кромки. Автор использует специальный станочек, который позволяет точно контролировать угол заточки.


Вот такой небольшой, но весьма функциональный инструмент получился у мастера.
Даже предварительный проект почти полностью совпал с готовым результатом.
Благодарю автора за простой, но интересный мастер класс по изготовлению ножа для мастерской!
Всем хорошего настроения, удачи, и интересных идей!
Авторское видео можно найти здесь.
Источник
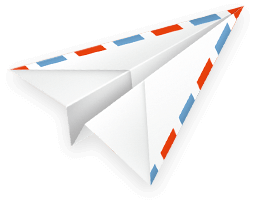
Получайте на почту подборку новых самоделок. Никакого спама, только полезные идеи!
*Заполняя форму вы соглашаетесь на обработку персональных данных
Становитесь автором сайта, публикуйте собственные статьи, описания самоделок с оплатой за текст. Подробнее здесь.Кухонный нож из старого напильника
Приветствую, Самоделкины!Сегодня мы вместе с автором YouTube канала «TEXaS TV», сделаем кухонный нож из старого напильника, а также попутно сделаем еще парочку полезных самоделок.

Вот из этого напильника и будем сегодня делать нож:

Это самое подходящее, что нашлось в гараже автора. Ширина напильника составляет 18,5 мм, толщина 4,5 мм.


Для начала делаем предварительную разметку. Все будем делать экспромтом, так будет интереснее, что получится в итоге.

С помощью болгарки вырезаем черновую заготовку клинка. Автор честно признается, что раньше не делал ножи, это будет первый опыт.


Теперь полученную заготовку нужно немного окультурить и гриндер в этом сильно поможет.

Снимаем всю структуру и выравниваем все грани напильника, чтобы получилось чистая и гладкая заготовка. Дело это конечно не минутное, поэтому нужно запастить терпением. Также не забываем охлаждать деталь. Получилась вот такая заготовка:


Теперь чтобы продолжить делать нож, нам понадобится приспособление, с помощью которого делают спуски. Его изготовлением сейчас и займемся. Сперва от 63-го уголка отрезаем заготовку 180 мм, это будет основная часть приспособления.

Полученную деталь зажимаем в тиски и наносим разметку для того, чтобы как можно точнее отрезать одну полку уголка. Немного зачистим заусенцы и подровняем торцы.
Теперь на одной из полученных заготовок делаем разметку под сверление отверстий. Размеры произвольные, но симметричные. Предварительно все это дело нужно накернить и сделать это достаточно точно.


Теперь можно заняться сверлением.

На удивление все пошло достаточно быстро. Резьбу нарезаем под болт м6. Получилась вот такая деталь с 18-ю отверстиями:


Теперь эти 2 заготовки необходимо скрепить через петли.


Петли будем делать из удлиненных гаек и болтов такого же диаметра. Гайку сверлим под диаметр болта и все — петля готова.
Петли приварены таким образом, что деталь получилась неразъемной и без люфтов. Собственно, вот так выглядит устройство для изготовления спусков на клинке по заданному углу.



Клинок устанавливается на вкрученные изнутри болтики и фиксируется струбцинкой. И сейчас мы будем делать эту струбцинку из вот этой вот гайки на 36:

Для этого с помощью ножовки по металлу выпиливаем сегмент, чтобы гайка выглядела как полумесяц.

На одной из граней гайки делаем резьбу М8. И в итоге получаем струбцинку нужного нам размера.


Вот так выглядит струбцинка и клинок, установленные на приспособление:


Ну что, нужный угол выставили и можно начинать обработку. Работа не быстрая, да и в принципе торопиться не стоит, нужно почувствовать инструмент и понять весь процесс, как говорится, изнутри.


Заготовку не перегреваем и по необходимости охлаждаем. Одна сторона готова, в итоге получилось вроде неплохо.


Теперь нужно его повернуть и сделать то же самое, с другой стороны. Кстати, автор попробовал фиксировать клинок при помощи пластиковой стяжки и хочет заметить, что вариант вполне себе рабочий, если часто не переставлять клинок.


Черновая обработка почти закончена, сейчас пройдемся зерном помельче, к сожалению, у автора самая мелкая это сотка, дальше сбиваем риску от гриндера уже вручную, пока не исчезнут все поперечные риски.


Чтобы не испортить плоскости, делаем это на притирочной плите. Вот так выглядит клинок после проделанной операции:
Поперечных рисок нет. Хотелось бы еще пройтись наждачкой помельче, но к сожалению, под рукой у автора только 240-ая, а в магазин ехать было уже поздно. Поэтому он решил исправить это полировкой. Специальных паст у автора нет, так как заранее он к этому не готовился, поэтому полирует по старинке пастой ГОИ.

Одна сторона почти готова, получилось вроде неплохо:

Тоже проделываем со второй стороной и на выходе получаем вот такой вот клинок:

Теперь можно переходить к изготовлению больстера. Автор будет его делать из какой-то дюралевой крышки, в общем из того, что нашел в гараже. Также больстер можно изготовить из монеты. Сделаем отверстия по диаметру хвостовика клинка.

Теперь отрезаем ножовкой по металлу с запасом и приводим все в надлежащий вид с помощью наждачки и полировки.


Перед дальнейшей работой клинок необходимо заклеить малярной лентой во избежание лишних царапин и потертостей, да и шанс порезать руки значительно уменьшится.
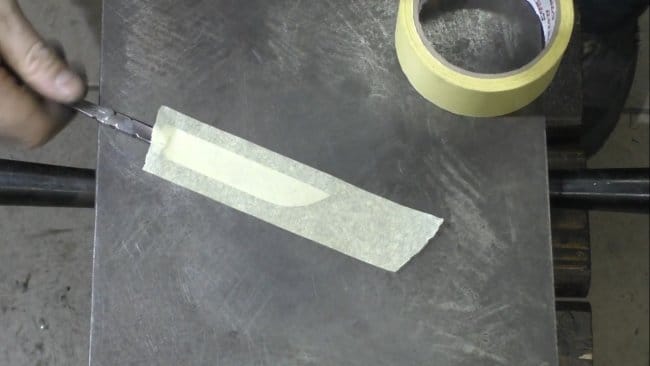
Теперь можно приступить к изготовлению рукояти. И здесь тоже без вариантов, только подручные материалы. Остался у автора кусочек яблони от прошлых самоделок – сгодится.

Отпиливаем все лишнее, но оставляем заготовку с запасом для последующей обработки. Отверстие делаем сверлом диаметром 4 мм под толщину хвостовика. Здесь главное сильно не закосить, чтобы клинок стоял в одной плоскости с рукояткой.
Получилось вроде хорошо, можно вклеивать. Клеим на двухкомпонентный клей, здесь нужно делать все быстро, но аккуратно, потому что клей схватывается довольно таки быстро и если он схватится в рукоятке, то придется все переделывать, а это нам совсем не нужно.
В качестве зажима автор применил токарный станок, получилось довольно таки неплохо, здесь кто на что горазд.
Прошел где-то час, хотя клей сохнет всего 10 минут, но автор решил все-таки перестраховаться. Теперь можно заняться и черновой обработкой. Для начала можно все грубо сбить рашпилем и болгаркой, тут уж кому как больше нравится.


Ближе к финальной стадии отрезаем лишний кусок рукояти и загоняем окончательный размер.


Ну что ж, получилась вот такая рукоятка:
Довольно неплохо и в руке лежит хорошо. Теперь для большей эстетики пропитаем рукоятку маслом, тем самым выделив ее структуру и предав древесине защитные свойства.


Окончательная доводка на коже и можно бриться (шутка конечно).

Ну и как показывают все ножеделы — тест на бумаге:


Автор даже сам не ожидал такого результата, можно даже бриться, но тут уже без шуток:


В общем вот такой ножик получился. Ну а сегодня мы сделали целых 3 полезные самоделки, но самое главное из них — это конечно кухонный нож, сделанный от начала и до конца.



Благодарю за внимание. До новых встреч!
Видео:
Источник
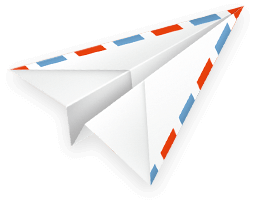
Получайте на почту подборку новых самоделок. Никакого спама, только полезные идеи!
*Заполняя форму вы соглашаетесь на обработку персональных данных
Становитесь автором сайта, публикуйте собственные статьи, описания самоделок с оплатой за текст. Подробнее здесь.Нож из напильника, плюсы и минусы, необходимы материалы и инструменты
Нож – это инструмент, которым ежедневно пользуется каждый взрослый человек в различных целях. В последнее время довольно сложно купить высококачественный нож в магазине или на рынке, так как распространилось много подделок из низкосортного материала. А если покупать настоящее фирменное изделие, то его цена будет весьма внушительной. Можно стать обладателем прекрасного предмета, если изготовить нож из напильника, выполненного из высокопрочной стали. Для изготовления не обязательно приобретать новый напильник, вполне подойдет старый, у которого поверхность из рельефной превратилась в гладкую от многократного использования.
Плюсы и минусы
Нож из напильника своими руками можно соорудить как универсальный кухонный, так и для охоты, рыбалки, туризма и даже складной. Независимо от разновидности, каждый инструмент, выполненный самостоятельно, обладает рядом преимуществ:
- Длительный срок эксплуатации. Изделие прослужит долго, так как закаленная сталь очень прочная, не будет гнуться и ломаться при разрезании твердых предметов.
- Доступность материалов. Старые напильники имеются у многих, а трудоемкость процесса компенсируется получившимся дешевым ножом.
- Толщина ножа получается больше 6 мм, поэтому он не будет относиться к категории холодного оружия.
Помимо достоинств у самодельного инструмента имеются некоторые недостатки. Процесс изготовления является сложным, требует внимания и аккуратности. Ошибки при работе недопустимы, так как изделие может получиться недостаточно прочным или совсем непригодным к применению. Кроме того, из стального полотна не получается гибкое лезвие, и оно может на изгибе просто рассыпаться, нанеся травму. Нож из напильника имеет плюсы и минусы, но в целом изделие получается крепкое, прочное, долговечное.
Необходимые материалы и инструменты
Для производства ножа своими руками нужен напильник, ширина его не должна превышать 3 см. Лучше всего, если он изготовлен в советские времена, то есть особо прочный. Наиболее подходят для изготовления ножа сталь марки У10, которая оснащена углеродом, или современные улучшенные стали. Сечение инструмента должно быть плоским или в виде ромба. Кроме напильника требуются другие подручные материалы и инструменты. К ним относятся:
- хлорное железо для процесса травления лезвия;
- эпоксидка;
- магнит, которым проверяется степень закаленности;
- заклепки из латуни;
- магнит;
- тиски;
- наждачная бумага, которой будут обрабатываться поверхности.
Обработка будет производиться с помощью шлифовальной машинки или болгарки. Помимо инструментов и материалов для выполнения лезвия, требуются материалы для будущей рукоятки: металл, дерево. Необходимо перед работой сделать эскиз будущей конструкции, который выполняется на бумаге.
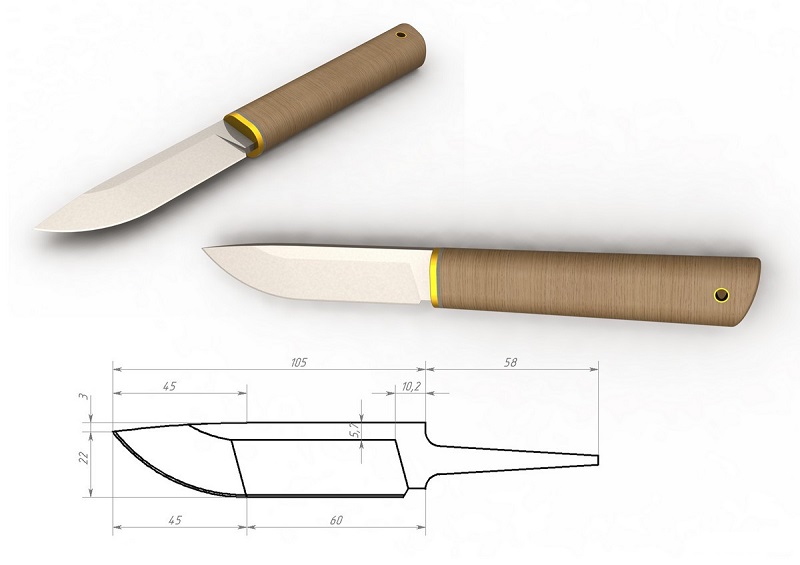
Чертеж
Обжиг заготовки
Металл, используемый для производства напильников, является очень твердым, поэтому не удастся просто ободрать полотно и сформировать режущую кромку с помощью обточки на станке. При нагревании на точильном оборудовании, режущая поверхность не будет держать заточку и, возможно, будет крошиться. Поэтому напильник обязательно следует обжигать, то есть возвратить сплаву технические параметры, которыми он обладал до его обработки в заводских условиях. Чтобы обжечь напильник, его нужно поместить в огонь: костер, емкость (бочка), печка, газовая плита. Важно, чтобы огонь был постоянным, на протяжении 4-6 часов. Тогда напильник приобретет температуру до 700 градусов.
Если обжиг производится на газовой плите, то достаточно накалять тот участок, который станет лезвием, не обязательно нагревать заготовку целиком. Но жара от конфорки не будет хватать, чтобы достичь необходимой температуры для обжига. Поэтому опытные специалисты рекомендуют разместить на решетку плитки, по боковым частям изделия, своеобразные ограничители из металла с толщиной, которая должна быть больше, чем толщина заготовки, к примеру, болты. На них размещается металлическая пластина, но не очень тонкая, кастрюля, чайник. Таким образом, предмет из металла отражает тепло, которое поднимается вверх.
Контролировать температуру горения поможет обыкновенная поваренная соль, используемая на кухне. Солью посыпается поверхность напильника, и, если она не плавится, то не хватает температуры, следовательно, ее надо добавить. Заготовка внешне должна иметь цвет расплавленного металла, а ее окрас должен быть равномерным в течение 3-4 часов. Интенсивность горения уменьшается плавно, приблизительно в течение часа, минимум – 50 минут. Остывание также производится постепенно, лучше оставить заготовку на месте, где происходил обжиг, пока она полностью не остынет.
Формирование
Напильник после остывания зажимается в тиски и подвергается снятию лишних участков и приданию ему формы в соответствии с выполненным предварительно чертежом. Можно воспользоваться для обточки абразивным диском Если требуется изготовление ножа из напильника с небольшим лезвием, то не стоит отрезать лишнюю часть от заготовки. Она пригодится для выполнения полноценной рукоятки или послужит основой, в которой проделываются отверстия, чтобы закрепить пластины из дерева, пластика, металла. Рисунок вырезается из листа бумаги, к нему прикладывается заготовка. На напильнике маркером обводится контур макета.
На заготовке формируется переход обуха клинка в режущей кромке, что обозначается пропилом небольшой глубины. От места пропила берет начало острие клинка. Затем следует этап формирования спусков на острие, который осуществляется с применением наждака или напильника. При этом очень важно, чтобы расположение было симметричным, а поверхности гладкими. Финишную обработку ножа следует проводить с помощью наждачной бумаги, которой оборачивается брусок из дерева.
Нож после обжига готов, но он является мягким материалом, поэтому его нельзя использовать в полную силу!
Как правильно закалить
Некоторые мастера совершают закалку, ориентируясь на свечение нагретого напильника, хотя это является ошибкой. О том, как закалить нож из напильника правильно, вы узнаете из последующего описания. Нагревать заготовку следует в старом масле-отработке до тех пор, пока клинок не приобретет темно-красный цвет. Но, поскольку по цвету сложно определить степень готовности даже бывалому мастеру, то используется магнит. Холодная сталь магнитится, но если она нагрета до нужной температуры, то магнититься не будет. После того как достигнута нужная степень закаливания, предмет резко опускается в емкость с отработанным маслом. Чтобы охлаждение происходило быстрее, емкость помещается в другую, с налитой в нее холодной водой. Закаленное таким образом изделие оказывается при эксплуатации прочным, твердым, надежным.
Чтобы проверить твердость материала, нужно провести ножом по стеклу. Если сталь закалена качественно, то на стекле остаются бороздки.
Далее производится травление изделия в хлорном железе, вследствие чего на металле появляется оксидная пленка. Эта пленка станет защитой ножа от коррозии. В случае, если нет хлорного железа, вполне могут подойти уксусная кислота, сырой молотый картофель, сок из лимона.
Изготовление рукоятки
Перед тем, как начать делать ручку, необходимо изготовить гарду, которая располагается между рукояткой и лезвием. Изготавливается она из любого материала: сталь, латунь, железо. Сама рукоятка может быть выполнена из дерева, металла, кости, пластика, кожи, текстолит.
Дерево
Наиболее распространенным материалом является древесина различных пород. Для изготовления деревянной ручки берутся куски материала, которые склеиваются между собой с помощью эпоксидной смолы. Для наиболее прочного и быстрого склеивания изделие лучше всего положить под пресс. После того, как куски дерева приклеились, все лишнее обрезается пилой, обрабатывается крупной, затем мелкой наждачкой. На готовую рукоятку наносится лак, предохраняющий древесину от влаги и порчи, можно ручку затемнить с помощью морилки.
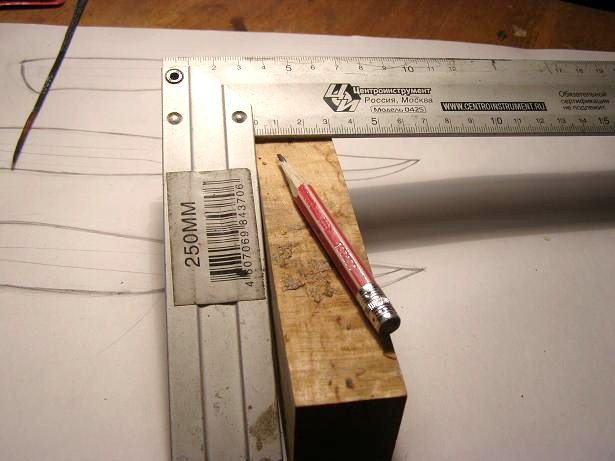
Размечаем деревяшку по всем плоскостям
Текстолит
Из текстолита вырезается кусок, длина и ширина которого зависит от того, какую рукоятку вы хотите сделать. Обычно длина составляет от 7 до 12 см, ширина – до 2 см. Чтобы сцепление было крепче, на хвостовике напильником делаются насечки. В центре куска текстолита просверливаются отверстия под хвостовик. Рукоятка крепится на эпоксидку, которой обильно смазывается хвостовик изделия, а также сама ручка внутри. После высыхания на рукоять желательно наклеить трафарет, вырезанный из эскиза. Затем рукоятке придается любая конфигурация с помощью наждачного станка, напильника или гриндера.
Кожа или брезент
Чтобы обмотать заготовку, берется довольно длинный кусок материала и наматывается на место для рукоятки. Для проверки количества намотки, нож можно взять в руку, по ощущению будет понятно достаточно ли материала: насколько комфортно ощущается заданная толщина в руке. Если недостаточно, следует наматывать еще, а когда появится ощущение комфорта, материал следует отрезать. Затем обмотка снимается, основа ручки покрывается специальным клеем, и наматывание производится снова, только уже более аккуратно и тщательно.
Наборная рукоятка
Интересным оригинальным вариантом выполнения является наборная ручка. Чтобы ее изготовить, требуется пробка или береста, из которых нарезается много кусочков прямоугольной формы. Их число зависит от длины будущей рукояти. По центру каждого прямоугольника просверливаются дырочки, в них войдет хвостовик. Все детали со всех сторон хорошо смазываются эпоксидным клеем. Чтобы придать оригинальности изделию, между кусочками бересты или пробки можно вставить такие же детали из тонкого пластика.
Сборка
Собираются детали будущего ножа из напильника без ковки с помощью заклепок. Специальные заклепки продаются в специализированных магазинах. Они производятся чаще из стали, реже латунными, медными, алюминиевыми. Выглядят заклепки как металлический стержень со шляпкой. Чтобы соединить детали, в них нужно просверлить отверстия, равные по диаметру стержню. Заклепки вставляются в дырочки, шляпка при этом опирается на наковальню, острый конец расплющивается с помощью молотка. Соединение рукоятки заклепками получается прочным, неразъемным. Лучше всего применять вытяжные заклепки, с которыми можно работать без использования молотка. Соорудить элементы крепления можно самостоятельно, используя в качестве исходного материала распорные гильзы, гвозди.
Чистовая обработка и заточка
В конце работы нужно сделать чистовую обработку ножа, которая заключается в придании ручке окончательной формы и заточке. Рукоятка, в зависимости от материала, шлифуется, натирается воском. Но основной и самый сложный этап – это заточка лезвия ножа. Производить заточку лучше всего вручную на обычном точильном камне. При использовании электрического станка металл может перегреться. Править лезвие хорошо на круглом стержне с насечками, который называется мусат, и часто имеется в комплекте с кухонными ножами.
Заточка готового изделия производится под различными углами, она зависит от предназначения инструмента.
Вид инструмента и назначение | Угол заточки в градусах |
Столовый | 55-60 |
Для кухни в домашних условиях | 30-35 |
Для поваров профессиональные | 25-30 |
Для разделки и обвалки | 25-30 |
Профессиональная разделка рыбы | 25 |
Обработка различных овощей на предприятиях | 35 |
Для охоты и складные ножи, если нужна острота | 30-35 |
Для охоты и складные, если нужная хорошая устойчивость к затуплению | 40-45 |
Конечно, каждый может заточить готовое изделие по своему усмотрению, но это общепринятые правила, которым желательно следовать.
Самодельные ножи из напильника может сделать любой на свой вкус: для работы на кухне, для разных других целей. Инструмент, выполненный своими руками, станет предметом гордости мастера. Прочный нож из напильника будет служить долго, он надежный, а также имеет неповторимый дизайн.
Видео
Нож из напильника, который режет стекло
Приветствую всех любителей помастерить, сегодня мы рассмотрим, как изготовить стильный и безотказный нож из старого напильника. У автора клинок получился настолько крепким, что нож легко режет стекло. Клинок был изготовлен без ковки, однако вам понадобится печь для термической обработки стали.
Накладки ножа изготовлены из текстолита и закреплены на винтах, так что рукоять не боится ни воды, ни грязи. Чтобы клинок не ржавел, автор выполнил травление, в итоге нож обрел интересный черный налет. Самоделка в изготовлении не сложна, если проект вас заинтересовал, предлагаю изучить его более детально!
Материалы и инструменты, которые использовал автор:
Список материалов:
— старый напильник;
— текстолит или G10;
— винты.
Список инструментов:
— печь для термической обработки;
— болгарка;
— ленточный шлифовальный станок;
— дрель или сверлильный станок;
— бормашина;
— карандаш;
— ножовка;
— метчик для нарезания резьбы;
— ленточный отрезной станок;
— напильники;
— наждачная бумага.
Процесс изготовления ножа:
Шаг первый. Отжиг
Для начала нам нужно подготовить напильник к дальнейшей обработке. Напильник подойдет старого образца, в котором использовался качественный металл, в современных напильниках внутри металл плохой. Обычно при резке углеродистой стали летят яркие желтые искры, которые образуют на концах звезды, искры похожи на те, которые образуют бенгальские огни.
Напильник сам по себе закален, так что обрабатывать его тяжело, чтобы решить проблему, кидаем напильник в печь, раскаляем до 800°C и даем постепенно остыть. После этой процедуры напильник станет мягким и пластинным, его можно будет обрабатывать другим, закаленным напильником.
Шаг второй. Первичный профиль
Далее вырезаем первичный профиль, автор рисует его от руки при помощи карандаша прямо на напильнике. Для резки автор использует болгарку, изгибы можно вырезать частями. Для более тонкой обработки проблемных участков автор использовал бормашину.
Далее профиль останется обработать по контуру на ленточной шлифовальной машине.
Шаг третий. Спуски
Сделаем на клинке спуски, их сперва рекомендуется разметить, чтобы не путаться во время шлифовки. Для работы автор использует ленточную шлифовальную машину в сочетании со специальным держателем для клинка. Учтите, что сталь может сильно разогреваться при шлифовке, лучше время от времени опускать клинок в воду.


Шаг четвертый. Доработка профиля
В завершении автор решил нарезать на обухе зубчики, они используются как декор. Для начала автор прорезает канавки при помощи ножовкой по металлу, ну а далее на помощь приходит бормашина с соответствующей насадкой.
По обуху проходимся напильником, нам нужно сточить острые грани.
В завершении сверлим отверстия в рукояти и нарезаем резьбу, они нужны для крепления накладок винтами.
Шаг пятый. Термическая обработка
Приступаем к закалке клинка, при помощи этой процедуры мы сделаем сталь максимально твердой. Автор разогревает клинок до 800°C, при этом надо следить, чтобы клинок светился равномерным цветом. Раскаленную сталь опускаем в масло.
Теперь сталь закалена и она хрупкая, нам нужно, чтобы клинок пружинил и мог выдерживать большие нагрузки. Для этого отправляем клинок в печь, и греем при температуре 180°C около часа. Теперь сталь закалена и отпущена, у автора сталь получилась довольно крепкой, клинок режет стеклянную банку.
После закалки можно обрезать лишнюю часть «хвоста» и выполнить шлифовку клинка.
Шаг шестой. Накладки
Изготовим накладки для ножа, в качестве материала можно использовать текстолит или G10. Такой материал крепок, не боится воды и грязи, а также он долговечен, да и по стилю в нашем случае подходит. Вырезаем две накладки и сверлим отверстия под винты. В задней части рукояти между накладками останется зазор, сюда автор вклеил еще один кусок текстолита. Заготовки устанавливаем на нож и приступаем к шлифовке рукояти на ленточной шлифовальной машине. Финальную обработку производим при помощи напильников. Вот и все, теперь у нас есть две отличные накладки для рукояти.
Шаг седьмой. Травление
При желании можно произвести травление клинка, металл станет темным, он будет неплохо защищен от окисления. После травления автор решил отшлифовать лезвие ножа до блеска.
Шаг восьмой. Финальные штрихи и сборка
В завершении автор решил в задней части рукояти сделать отверстие треугольной формы под шнурок. Для начала сверлим обычное круглое отверстие, а затем растачиваем его надфилями и треугольным напильником. Вот и все, рукоять можно собирать, заворачиваем винты и все готово. При желании можно выполнить тонкую шлифовку рукояти мелкой наждачной бумаги.
Нож собран, смотрится он великолепно, да и технические характеристики такого ножа будут на высоте. На этом проект окончен, надеюсь, вам самоделка понравилась. Удачи и творческих вдохновений, если решите повторить подобное. Не забывайте делиться с нами своими идеями и самоделками!
Источник
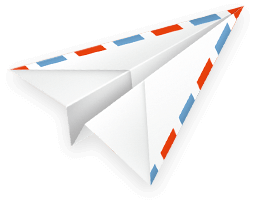
Получайте на почту подборку новых самоделок. Никакого спама, только полезные идеи!
*Заполняя форму вы соглашаетесь на обработку персональных данных
Становитесь автором сайта, публикуйте собственные статьи, описания самоделок с оплатой за текст. Подробнее здесь.как сделать клинок своими руками
Чтобы получить необходимые характеристики ножа из напильника, следует нарисовать на плотной бумаге его эскиз. Это позволит сделать максимально точную окантовку заготовки.
Сам инструмент лучше брать со стёртой насечкой. Напильник изготовлен из высокоуглеродистой стали, поэтому нож будет хорошо резать без постоянной заточки. Можно использовать и другой металл, а затем его закалить.
Плюсы и минусы
Создание ножа из напильника своими руками может казаться нецелесообразным, так как на рынке представлено большое количество готовой продукции. Но такой инструмент даст фору большинству заводских собратьев. Также он будет полностью уникальным. Чтобы клинок получился твёрдым и качественным, следует для заготовки выбирать только высокоуглеродистую сталь.
В изготовлении ножа из напильника есть несколько минусов:
- Процесс создания инструмента очень трудоёмкий. От человека требуется большое внимание к техническим тонкостям. Ошибки в работе допускать нельзя, иначе заготовка может просто испортиться.
- Из напильника не получится сделать гибкое изделие. Такая сталь имеет структуру, которая при боковых нагрузках может рассыпаться.
Но у самодельного ножа из напильника есть и свои неоспоримые плюсы. Они заключаются в выбранной заготовке. Основные достоинства:
- Материал очень долговечный и крепкий. Это придаёт мастеру уверенности при выполнении любых работ.
- Напильник — вещь, доступная каждому. Его можно найти практически в любом доме. Процесс изготовления вполне окупает стоимость дорогого изделия.
Ножом собственного производства даже можно гордиться, если он получится качественным и красивым. Если соблюдать все инструкции, то изготовление не вызовет особых сложностей.
Общие характеристики
Если знать из какой стали производят напильники, можно понять, почему именно их используют в качестве заготовок для изготовления самодельных ножей. Делают шлифовочный инструмент из высокоуглеродистой стали (У10А, Х12М).
Большое количество углерода в сплаве позволяет закалять материал до 66 единиц по Роквеллу. Это даёт изделию высокую прочность, поэтому сделать нож из напильника будет наилучшим решением.
Качественный нож умельцы производят из таких заготовок:
- Сверла по металлу. Но здесь нужно помнить, что закалке подвергается только рабочая часть.
- Поршневого шатуна.
- Рессоры.
- Напильника.
- Торцевого ключа.
Чтобы профессионально сделать финку, необходимо материал подвергнуть предварительной ковке. Удобнее всего это осуществлять с напильником, так как у него подходящая форма. Ковка позволяет сделать металл более эластичным.
Толщина надфиля слишком большая, поэтому необходимо снять часть металла, чтобы появилась возможность сформировать спуск. Ковочные работы подразумевают не удаление слоя металла, а создание другой формы. Ковка занимает гораздо меньше времени, чем изготовление заготовки на станке.
Если у человека есть опыт и соответствующее оборудование, он легко сможет создать профессиональное изделие. Но встает вопрос о необходимости выполнения ковки, ведь заготовка уже имеет подходящую форму.
Ковка нужна по следующим причинам:
- Металл станет более твёрдым и эластичным.
- Заготовка имеет слишком большую толщину, что делает необходимым снятие части металла во время формирования спусков. Ковочные работы убирают это требование.
- На конечную обработку потратится гораздо меньше времени.
Также этот процесс позволяет убрать насечки. Конечно, это и не обязательно, ведь так изделие становится более оригинальным.
Когда нет специального оборудования, сделать изделие можно и без ковки. Если применять качественный материал, результатом будет отличный клинок. На современном рынке очень много китайских инструментов. Желательно использовать напильники советского производства, но найти их не так-то и просто.
Проверить металл довольно легко. Необходимо один край будущей заготовки зажать в тисках, а по второму сильно ударить молотком. Если изделие закалённое, оно сломается. Легированный напильник лишь чуть-чуть прогнётся. Также для проверки можно использовать и точильный станок. Если искры короткие, то металл высоколегированный. Но всё равно придётся проводить термическую обработку.
Обжиг заготовки
Первым делом необходимо будет произвести обжиг инструмента. Идеальным вариантом считается выдерживание заготовки на протяжении 5 часов в горящей печке. Остывать материал должен медленно. Также можно применять и обычную плиту. Но нужно помнить, что это не рекомендация, а выход из положения.
Суть обжига заключается в том, чтобы раскалить и удерживать сталь при температуре минимум в 600 градусов по Цельсию, а затем дать медленно остыть. Можно обжигать и только ту часть, которая в будущем будет использоваться в качестве лезвия.
У домашней газовой печи маленькая температура, из-за чего придётся соорудить тепловой экран. Делается это довольно просто: нужно над заготовкой создать возвышенность из болтов и гаек, а на неё уложить металлическую пластину. Так можно снизить рассеивание температуры в окружающую среду, что увеличит нагрев самого напильника.
Важно использовать соль в качестве индикатора. Если во время обжига она расплавится — всё прошло успешно, если же нет, то температуры было слишком мало. В этом случае придётся повторять процесс. Розовый цвет следует поддерживать на протяжении 4 часов (минимальная длительность).
Снижать температуру нужно очень медленно. Сначала необходимо убавить горение примерно на 25%. Через некоторое время ещё немного уменьшить. Это повторяется до полного остывания. Если сталь охладится быстро, то она попросту раскрошится.
Изготовление режущей части
Форма лезвия может быть абсолютно любой. Она выбирается исходя из сферы применения.
Основные виды:
- Прямой клинок, сделанный в виде треугольника. Такая форма позволяет отлично выдерживать нагрузки от равномерных ударов. Также имеет хорошее сопротивление к резке.
- Вогнутый. Такая форма не способна выдерживать большие механические нагрузки. Чем глубже, тем выше становится сопротивление.
- Выпуклая линза. Эти ножи необходимы для тяжёлых работ.
Следующий этап начинается после охлаждения изделия. Нужно аккуратно его обработать. Процесс состоит из таких этапов:
- С помощью ножовки врезается необходимый контур, в задней части вырезать хвостовик. Нужно максимально точно создать лекало, чтобы уменьшить время работы на станке.
- Заготовка зажимается в тисках. С использованием напильника создаются оптимальные спуски. Чтобы сохранить симметрию, можно с помощью металлической трубы создать специальное приспособление, на которое будет закрепляться инструмент.
После грубой обработки необходимо доработать изделие при помощи наждака. Чтобы было удобнее, можно бумагу обернуть вокруг бруска.
Закалка готового лезвия
Чтобы клинку вернуть его твёрдость, необходимо правильно произвести процедуру закалки. Для этого его нужно разогреть до 900 градусов по Цельсию. После этого нож следует быстро охладить.
В домашних условиях можно использовать для нагрева паяльную лампу. Струю пламени нужно располагать так, чтобы она шла вдоль лезвия. Важно следить за равномерностью прогрева.
Можно применять и обычный древесный уголь. В него необходимо закопать клинок. Разогрев также следует производить паяльной лампой. Во время нагрева нужно обеспечить правильную температуру. Это можно определить по цвету заготовки, который изменяется при разной степени накала. Когда температура достигнет 900 градусов, клинок станет малинового цвета.
Охлаждать нужно в воде или отработанном масле. Процесс осуществляется следующим образом:
- Если применяется вода, в неё обязательно нужно добавлять рассол или соль. Без этого нежелательно проводить охлаждение. Чтобы металл не согнулся, следует опускать нож вертикально.
- Отработку нужно налить в железное ведро. Нож должен быть привязан на какой-нибудь проволоке, чтобы можно было опускать его в жидкость. Вязкость отработанного масла оптимизирует процесс теплообмена. Полное остывание наступит через несколько минут. Нужно помнить, что масло может загореться.
Недостаточный прогрев не позволит качественно закалить железо. Если сделать всё правильно, нож получится твёрдым и крепким.
Секреты отпуска и создание ручки
Процесс закалки позволяет улучшить качественные характеристики изделия. Но это и повышает его хрупкость. Если ударить металлом об какую-нибудь твёрдую поверхность, клинок может попросту расколоться. Чтобы убрать такой эффект, необходимо отпустить сплав. Отпуском называется вид термообработки.
На протяжении часа нож нужно прогревать при 200 градусах. Для нагрева подойдёт обычная духовка. Охлаждение происходит постепенно на открытом воздухе.
Можно проводить отпуск и в расплавленном свинце, но его температура слишком большая (327 градусов). Выполнение процедуры таким образом повлечёт уменьшение твёрдости.
Ручка делается из двух деревянных накладок, которые крепятся к хвостовику ножа. Для прокладок можно брать кожу. Её следует вырезать в точности по контуру деревянных элементов. В металлической, деревянной и кожаной частях просверливают отверстия. По его сечению отрезаются 3 трубки.
Все эти элементы тщательно промазываются клеем и собираются воедино. Через несколько часов клей затвердеет. Все незначительные дефекты удаляются с помощью наждачной бумаги. Чтобы готовый нож был хорошо защищён от различных факторов, вызывающих коррозию, его следует отполировать.
Изготовление ножа из напильника собственными руками в домашних условиях является довольно кропотливым процессом, но результат стоит этого. Клинок будет соответствовать всем требованиям, которые выдвигаются для выполнения какой-то конкретной задачи. Сталь у напильника имеет высокие качественные показатели, что отражается и на ноже.
Подробнее читайте тут Оцените статью:(7 голосов, среднее: 4.3 из 5)
Поделитесь с друзьями!Простой нож из напильника | Мастер-класс своими руками
На барахолке я нашел старый напильник и решил из него сделать нож. У меня не было желания предавать его термической обработке или часами шлифовать лезвие. Поэтому при минимальной обработке, я постоянно поддерживал температуру клинка холодной. Работа заняла около 2 дней (включая время высыхания клея).
Дизайн ножа
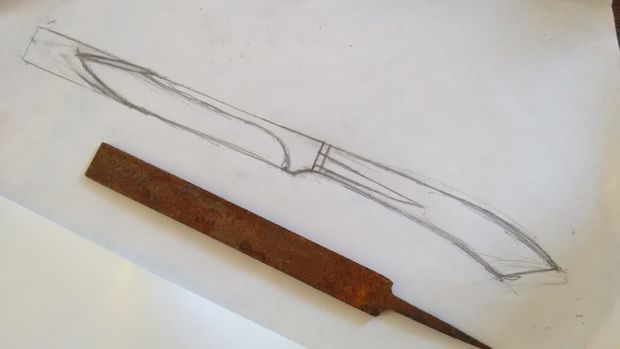
Я вручную набросал дизайн будущего ножа (с учетом ширины и толщины напильника). Но не ставил на нем точку, и в процессе готов был подкорректировать форму.
Обработка напильника
Сначала я обработал хвостовик, потом перешел к острию. Все это делал на точильном станке. Затем на глаз начал вытачивать спуск, который вышел неплохо – не идеальный, но мне понравился. В процессе обработки я не давал напильнику нагреваться, время от времени окуная его в стакан с водой, чтобы сталь не становилась мягкой. Это было легко допустить, так как чем тоньше становился напильник, тем быстрее он разогревался. Что-то привлекло бабочку, и она осталась на моей руке в течении всего процесса.
Обработка лезвия ножа
Затем, используя наждачною бумагу с зерном P60, я сделал поверхность более гладкой. Насечки были оставлены, потому что их шлифование заняло бы много времени. Лезвие получилось с вогнутыми спусками, потому что заточка проводилась на круге точильного станка. Я не ожидал, что поверхность будет более ровной.
Рукоять
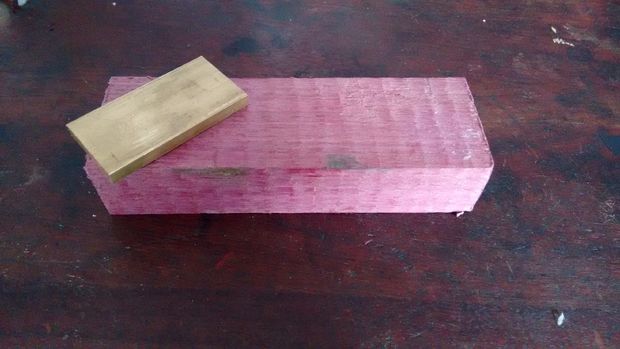

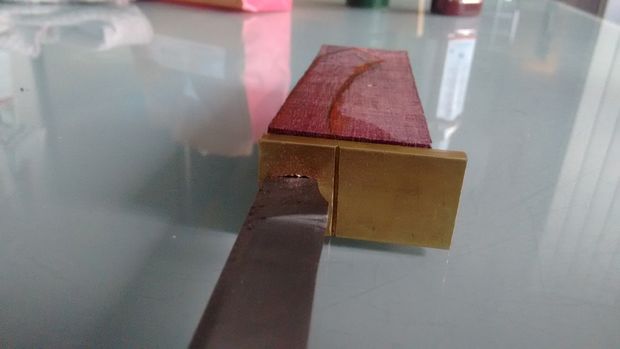
Рукоять изготовлена из пластины латуни толщиной 6 мм и бруска пурпурного амаранта. Я выбрал их, потому что латунь и пурпурный цвет хорошо сочетаются. В латуни я высверлил два 5 мм отверстия и соединил их с помощью дрели и полотна ножовки. Обычно в таких случаях люди используют разные надфили, но у меня их нет, да и к совершенству я не стремился. Хвостовик через больстер был вставлен в 5 мм отверстие в дереве, предварительно наполненное эпоксидной смолой.
Придание формы
Я дал клею высохнуть в течении ночи, после этого приступил к обработке рукояти. Сначала я разрезал брусок надвое, приблизив его длину почти к желаемой. После этого я зажал нож струбциной и приступил к обработке с помощью диска шлифовальной машины с зерном P120. При работе с больстером нужно соблюдать осторожность, так как дерево в сравнении с латунью, стачивается гораздо быстрее. После того, как профиль обрел желаемое очертание, я приступил к шлифовке боков, придавая им округленный вид. Весь процесс занял около часа.
Полировка
Обработав рукоять при помощи наждачной бумаги с зерном P240, используя полировальный круг, я сделал ее поверхность более гладкой. На ней все еще оставались царапины, но мне они понравились. После этого дерево было пропитано датским маслом (4 слоя с легким шлифованием в промежутках). Потом я придал остроту торцу рукояти оселком.
Дерево амаранта, окисляясь со временем, становится более пурпурным, а на фото кажется еще более красным.
Спасибо за внимание!
Original article in English